Even the most careful drivers can sometimes be the victims of circumstance and end up in an accident. Thanks to some "smart dummies" employed by Ford, however, these unfortunate occurrences may carry less dire consequences.
Ford uses approximately 18 different advanced crash-test dummies to conduct the myriad crash tests required by the federal government as well as many Ford-specific in-house tests.
Each of the dummies mimics the human shape, size and weight and is tailored for a specific test. Adult frontal-crash dummies include a small female (103 to 105 pounds), mid-size male referred to as the 50th-percentile male (175 pounds) and a large male dummy that equates to a 6-foot, 3-inch man who weighs about 225 pounds. Child dummies include 6-, 12- and 18-month olds, and 3-year-old, six-year-old and 10-year-old siblings.
The SIDs family (side impact dummies) consists of one small adult female and three mid-size adult males. BIORID, a mid-size adult male, is used for rear impact "whiplash" tests.
"Data is gathered from head to toe," says Risa Scherer, supervisor of Ford's Anthropomorphic Test Devices Laboratory. "The typical body regions monitored are the head, neck, chest, pelvis and legs. For side impact, we also monitor the abdomen and shoulders."
Depending on the dummy size up to 212 channels of data are sent to the computer during the crash sequence. The data is used to determine if changes need to be made to the restraint systems or vehicle designs. The data also helps to support computer modeling, allowing engineers to build more precise virtual models.
"Once the models are validated with the data gathered from the dummies," says Scherer, "then the virtual dummies can be used in computer crash simulations."
Scherer says the technology has advanced significantly over the past 10 years. Instrumentation and data collection systems have gotten smaller. More transducers can now be packaged into a smaller area yielding even more data.
"Data collection systems are incorporated into the dummy so we don't need to carry any extra weight on the vehicle. Their small size also reduces their influence on the performance of the dummies."
The Virtual Crash Test Dummy
The future automotive crash test dummy is currently being developed inside a computer. Ford safety engineers are working on the Human Body Model, a Finite Element Analysis (FAE), or computer tool that will help engineers better understand what happens to the human body during a crash.
Ford began building the human body model in 1993, creating the regions of the body such as the head, neck, rib cage, abdomen, thoracic and lumbar spine, internal organs of the chest and abdomen, pelvis, and the upper and lower extremities. These regions were brought together in 2004 to create the full body model.
The human body model represents an average adult male and is constructed using technologies like data gathered from MRI scans and topographies from human body anatomical texts. Validation of the computer model is done through cadaver and volunteer human testing.
The model features such things as a highly detailed spine with all the vertebrae segments and cartilage attached, and a very comprehensive brain model that has been used to determine the extent of injuries that can occur during a crash.
Saeed Barbat, manager, Passive Safety Research and Advanced Engineering, Ford Motor Company says that in the future, virtually-pressurized "blood vessels" may be developed to help determine how internal organs react during specific types of crashes.
"The Human Body Model will help reduce physical testing on component and full-scale levels during vehicle development," says Barbat. "It will also be used to develop more sophisticated instrumentation that could lead to more human-like crash dummies."
The data gathered using both actual and virtual crash test dummies will help Ford develop and bring to market innovative safety technologies faster than ever and in advance of possible future government regulations.
A Long History of Crashing Dummies
The test dummy dates back to 1949, when Alderson Research Labs (ARL) developed "Sierra Sam" for the U.S. Air Force. Sam was used to test jet fighter ejector seats, a job that had become too dangerous for human test pilots. By the early 1950s these crude crash dummies were already delivering data that helped automakers design safer cars.
In 1971, the first standardized automotive crash test dummy, the Hybrid I, was introduced by the Alderson Research Labs, the creator of Sierra Sam. Today's Hybrid III has a spine made out of metal discs, a movable neck, a steel rib cage, vinyl skin and knees that designed to respond to impact like the human counterpart.
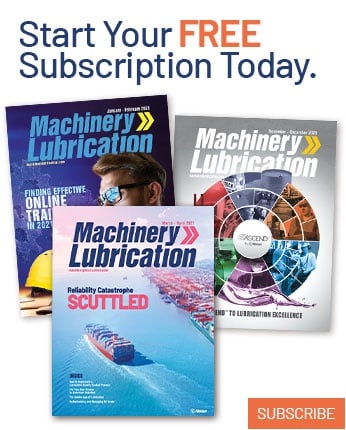