After decades of continuous development, enterprise-wide applications have come to offer very comprehensive functionality. With sufficient budget and organizational resources, a middle-market to large manufacturer can likely find enterprise software that includes functionality for virtually any business process with which they might be involved.
But whether we are talking about the broad and all-encompassing area of enterprise resource planning (ERP) or the more focused world of enterprise asset management (EAM), while functionality may be available to meet various needs, what has been lacking is proper attention to usability. Some enterprise software vendors are beginning to pay attention to usability with regard to ERP, but it is equally important in the area of EAM. Within an EAM application, functionality might exist to allow technicians to retrieve and enter data and allow executives to assess asset health, but if these tasks are difficult or time consuming, that EAM system will deplete valuable enterprise resources instead of contributing enterprise value.
In this article, we will examine the different usability problems manufacturers encounter with EAM software, how these problems drain enterprise resources, and specific EAM characteristics and features that can lead to enhanced usability.
Disparate systems
By far, the most common usability problems encountered with EAM are caused the lack of fully integrated applications.
What I see frequently within manufacturing maintenance departments and maintenance repair and overhaul (MRO) organizations is technicians a using one-point solution to manage their work orders, scheduling and planning, and an entirely different system to manage their inventory and potentially another system to handle their purchasing. Yet other systems are used to manage human resources, and to track the credentials and availability of people capable of performing specific types of work. Technicians, managers and executives working in two or three different systems are then forced to learn two or three completely unique process flows and navigation schema. This makes systems less intuitive, increases the amount of training necessary, and prevents users from having the time and inclination to fully explore and leverage the higher-end and more advanced functionality their various software packages might offer. Who has time to become a power user of not just one but two, three or more software packages? This is a drain on the professional time of technicians and executives and also ensures that they will not realize the full value or capability of any of the systems they are relying on because they simply lack the bandwidth to do so.
Usability is further reduced when a collection of point solutions are used for EAM because of the potentially huge amount of data re-entry and rework necessary to keep multiple systems current. Almost inevitably there will be some level of double entry, if for instance, on a work order, I used a part that actually needs to be issued by a second system.
In some other situations, manufacturers may be running home-grown systems that, as they were developed, expanded and added onto in-house over a period of years, became more and more complex and convoluted. Packaged software can, similarly, grow in complexity over time and suffer from suboptimal design, presenting usability challenges. Some packaged software used for EAM in fact consists of bundled point solutions that have been acquired by the vendor integrated in a point-to-point fashion. Of course, this may eliminate some rework, but still presents the usability challenges outlined above.
Why usability is important during selection
Maintenance technicians are intelligent enough to figure out the byzantine and confusing EAM systems they might be forced to use, and we certainly don’t want to discredit the intellectual capacity of the people who are using these systems. They are after all talented people who have the ability to repair complex systems. But manufacturing companies that employ these technicians did not hire them as computer operators, but rather to use their skills to keep production systems running and to keep capital equipment operable for its intended use. The technician is not employed to serve the needs of the EAM system, but rather the EAM system is there to help the technician get their job done as efficiently as possible, and it therefore needs to be selected because it is the right tool for that job.
This means that one main consideration in selecting EAM ought to be ensuring that technicians do not need to spend an inordinate amount of time navigating through the system – either to find and access the information necessary to perform their jobs or to enter information into the system in the course of reporting on work they have completed. It is essential that a selection committee consider the number of key strokes or clicks that they have to perform to get information into or out of the system.
Also important to consider is the amount of system-specific knowledge necessary to perform these tasks. How much training is necessary to understand the basics of how the EAM system works? After all, the way things are repaired hasn’t fundamentally changed over the last 100 years. Something is broken, and we fix it. The complexity of the capital assets and components we are working on have increased over time, and more recent innovations allow us to gather data that allow us to predict when something is about to break so we can replace it proactively. EAM supports this process by ensuring we are notified that something is wrong, getting a description of the problem, giving us the information necessary to make the repairs and defining what those repairs were including the amount of time spent and the materials and tools used. That information then needs to be visible to others in the organization responsible for finance, maintenance inventories, personnel scheduling and other related disciplines including manufacturing operations. An EAM system needs to be very intuitive and easily understood by anyone who is intimately familiar and experienced with these core processes.
But in the many maintenance departments I have visited or worked in over the years, I have seen the same suboptimal usability problems again and again that generally reduce an eight-hour shift for a technician to a mere five hours. What I have seen is the technician or planner forced to work in one or multiple systems each time a maintenance event comes up, and whether it is a planned maintenance activity or an imminent maintenance activity, these sub-optimal systems drain time and energy and slow down the repair. After the job is completed, technicians need to take additional time to enter data on the repair into the system, which slows their response time for the next work order that needs to be executed.
A standard benchmark for availability of manpower across an eight-hour shift is about six hours of productive time. If part of those six hours of productive time is doing computer entry, there is really no way to meet that benchmark. You have now cut into that six hours and now you are potentially 5.5 or even five hours in a shift. That is a productive loss of almost 17 percent! The productivity of maintenance technicians and maintenance planners has gone down because they are expending additional time working as computer operators, which of course is not what they were hired to do.
In a suboptimal EAM system, it is typically difficult to automate data capture using tools like RFID or bar code scanning on handheld devices. This means that technicians need to take long hand notes on pads they keep in a pocket on their coveralls and manually enter that data at the end of their shift. That disconnect between work and data entry creates the opportunity for human error, and by default forces technicians to record their work twice – once in their notepad and once in an EAM or CMMS system. Separate work management, inventory, human resources and other functions at the very least makes it a lot more expensive to solve this problem as the systems integration challenges become considerable.
Figure 1. EAM software needs to streamline the process of entering data on work performed. Here is the Quick Report In Work screen from IFS Applications.
How to assess usability during software selection
Obviously, the baseline requirement for EAM software usability is an integrated suite that includes the various disciplines and functionality that planners, technicians and executives need to touch. The more complete functionality that differentiates EAM from simple work management or computerized maintenance management systems (CMMS) includes:
- Inventory and supply chain management to marshal the parts and materials necessary to maintain the asset.
- Human resources functionality to ensure the availability of qualified workers to perform the required work.
- Financial functionality so that the entire cost of maintaining and operating the asset can be analyzed and the lifecycle of the asset can be managed strategically.
- Integration with manufacturing operations so that scheduling so that maintenance and production scheduling can dovetail gracefully.
- Sometimes, integration with CRM so that maintenance tasks can be scheduled to allow for urgent customer orders or other needs.
Once all of these functions are housed in a unified enterprise environment, preferably developed as part of a complete EAM suite, less time is spent learning different systems with different navigational schema. Less time is spent re-entering data. And the unified nature of the functionality makes it easier and significantly more affordable to automate data capture, eliminating a lot of the time that technicians spend working in the EAM system. If they can use a simple handheld device to capture data on parts and materials used as they use them, and perhaps even record their time and make other notations that get entered directly into the system wirelessly, non-value-added work is automatically eliminated and the EAM system becomes easier to use by an order of magnitude.
Integrated systems and automation can allow technicians to spend less time using the EAM system. But when technicians, planners, managers and executives do need to use the EAM system, they will find it a lot easier if that system mirrors computer functionality they are already familiar with. Almost any EAM system will require end users to go through at least some minimal level of training. But if the overall navigation, look and feel of an enterprise application can borrow key concepts from web navigation conventions, less training will be required and users will more rapidly feel comfortable in their mastery of the EAM software environment.
Of course even the web was not the most user-friendly of places before text-based search engines like Google and Alta-Vista. Before search, the web was a place where, in order to find something, you had to already know where it was. That is one reason so many web sites of the 1990s featured “links” pages. In most organizations, an EAM or ERP system works in much the same way. There are specific screens that users must know about and navigate into in order to query and find various pieces of data. There may even be “links” pages where people can store links to the screens they use most frequently.
Usability is enhanced when searches become intuitive much like a Google search is today, where you just enter a search string into a single, centralized search engine and the EAM system finds all of the different places that string occurs. This means that you don’t need to find the right place in the application to conduct your search, define numerous parameters and hopefully get the information you need. Instead, you can enter a requisition number, customer name, invoice number or supplier name and immediately get appropriate information. Advanced embedded search tools allow you to further specify the type of data you would like to find in order to deliver more targeted results.
An EAM system that offers a powerful search engine as an embedded feature delivers a high degree of usability. The other way to deliver a fully functional search feature is by adding complexity and cost with add-on enterprise search software.
Figure 2. Above are results of an embedded IFS Enterprise Application Search for “Wet End.” And below, are search results for work orders and tasks for a specific employee working in IFS Applications.
Figure 3.
Locating specific bits of information in a huge EAM system is one usability task that ought to be a consideration. But making sense of large blocks of data is another. Whether you are inputting all data manually or have automatic data capture feeding information on faults directly into an EAM system, making sense of huge amounts of asset data is another usability challenge. A usability-enhanced EAM system will provide managers and executives with intelligent ways to organize and visualize asset data for decision support.
Tree maps are one useful tool for management by exception because they do allow, at a quick glance, separation of the critical few elements that require attention from the many elements that do not. Executives in an asset-intensive environment are often managing by exception. When assets are running within normal parameters, they do not require attention. But when operations deviate from these parameters, an executive or manager must know about and be able to quickly ascertain what corrective steps need to be taken.
Figure 4. In this tree map from IFS Applications, the number of faults is represented by size and criticality by color. Users can drill down in the big red squares to find the reasons behind the problems.
Figure 5. In some cases, a manager or executive can be given much more information in a single screen, but can drill down to reveal greater detail on critical items. Here is an example of such a comprehensive screen in IFS Applications.
Figure 6. This screen within IFS Applications provides a simple and comprehensible view of production stops coded by reason.
Conclusion
Selecting EAM software on the basis of usability can be relatively simple if we remember our main points above.
- EAM needs to offer all of the key functionality necessary to support the asset in a single, unified system. This eliminates rework, prevents users from being forced to learn multiple systems and makes it easier to add automated data capture, further reducing time spent in the system.
- Web-like navigation and powerful embedded search is necessary to reduce the amount of training necessary. It is easier to recognize than it is to remember, so if users can intuitively understand how to use the EAM system based on their experiences with the Web, usability increases immensely.
About the author:
IFS North America senior business analyst Mike Auer has more than 25 years of experience in aerospace, power generation and high-speed manufacturing industries specializing in the implementation of predictive/preventive maintenance processes. Prior to joining IFS, he held industrial maintenance, engineering and other positions with Pergo Inc., Commonwealth Edison, Ford Aerospace and other major corporations. He holds a degree in business management from the University of Georgia.
EAM tools contain an enormous quantity of data. EAM software that presents intelligent options for visualization of this data will be more usable for executives and managers looking for real-time asset performance data for decision support.
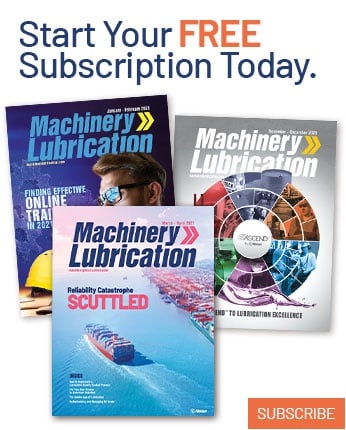