GE Intelligent Platforms on April 27 announced the availability of its Quad PAC redundant controller technology offering an innovative “quad” redundancy control solution that virtually eliminates downtime risk, enabling companies to protect against lost productivity, profitability and customer satisfaction. The system addresses the increased demand for more redundancy with higher speeds, real-time communications and deterministic data transfers. This unique and innovative approach virtually eliminates downtime risk – enabling companies to protect against lost productivity and profitability for a sustainable competitive advantage.
According to Electric Power Research Institute, companies in some industries can lose as much as $6.45 million per hour of downtime. Even at an average size company, one hour of downtime can cost $10,000, which translates to a loss of $3.679 million per year with a 5 percent power availability loss. Consequently, companies increasingly share the same demand: to ensure the highest level of system reliability and availability at the control layer, which is the heart of any backup power solution.
“The business impact of an unplanned outage can range from lost productivity to lost customers, depending on the business model and application, but it is clearly costly and disruptive,” said Mark Reitzel, commercialization leader for GE Intelligent Platforms Applied Solutions. “In addition, because many companies host critical data and services that impact other stakeholders, any loss is usually multiplied – leading to even higher total costs – both financial and operational.”
A quad redundancy control system has four redundant controllers—a Master Controller and three synchronized backup controllers. It leverages Ethernet-based I/O that can seamlessly arbitrate its I/O control from one of the four controllers. If the Master Controller or any of the system components fail, the system identifies the best backup controller to take over and provide the system with the most capability to withstand the next sequence of multiple or cascaded system failures.
The Quad PAC application consists of two redundant pairs of GE Intelligent Platforms’ PACSystems RX7i controllers working in unison, for a total of four RX7i controllers and their associated items (racks, power supplies, etc.). The controllers are connected via redundant high-speed fiber optic modules, which provide synchronized logic solving and data transfer between the controllers. Similar technology is used via network hubs to tie all four controllers into a cohesive quad-redundant solution.
The Quad PAC I/O system involves GE Intelligent Platforms’ PACSystems RX3i Remote I/O and redundant Ethernet LANs. Each remote I/O rack supports redundant network interfaces and provides all four controllers with the system inputs and outputs in a fully arbitrated format. The remote I/O racks may be grouped into either a single (one I/O rack), redundant (two I/O racks), or triple redundant (three I/O racks) rack configuration, in which each I/O rack communicates independently with all four controllers, and each controller shares the same input and output point addresses from each I/O rack.
The Quad PAC solution features “Smart Redundancy,” a patent pending algorithm that continually calculates the relative system availability in real time and delivers predictive analysis on key process input variables to clearly identify the next Master Controller most capable of surviving a system failure while maintaining maximum system availability.
“Continuity of operations is critical, and a quad redundancy control system ensures that any process can continue without interruption by having one of its three backup counterparts assume control if failure occurs,” Reitzel said. “In addition, this type of high availability system can also help reduce costs by enabling maintenance or exchange of individual system components without system interruption and no loss of system redundancy/availability.”
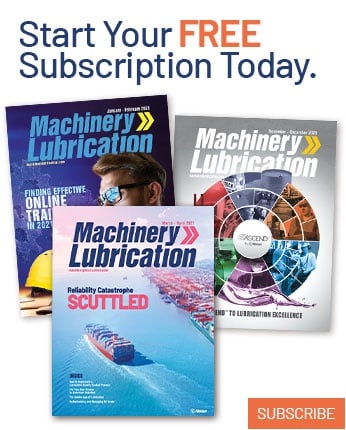