Whenever a new component is about to be commissioned, the first thing you need to address is the lubricant. A typical original equipment manufacturer’s (OEM) recommendation will usually state something like “use a high-quality turbine oil with a viscosity of ISO VG 32.” This leaves much to the imagination.
In this case, the OEM has not indicated what types of additives the lubricant should have, what base oil should be used and how to adjust the viscosity requirement based on the ambient conditions of your facility vs. the test-facility conditions the OEM used to determine these values. However, imagination aside, a keen technician can recognize some of the requirements specified by the OEM and select the proper lubricant to get the job done.
Start by reading between the lines of the OEM’s general lubrication recommendation. The OEM has guided you to use a high-quality turbine oil with a viscosity of ISO VG 32. If you pull this statement apart, you arrive at three distinct specifications.
WHAT’S ‘HIGH QUALITY’
First, the OEM states that the lubricant must be of “high quality.” You may guess that the OEM is simply saying to buy a product with which you have had previous success with regard to its quality. This could include the quality of service from your local distributor, quality delivery times, quality selection of products, quality sales representatives, etc. These items are all important. But the trained technician may recognize this description as an indicator of which American Petroleum Institute (API) base oil category to use in this component. In this particular case, high quality may mean a higher API category.
Looking at the description of the most common API base oil categories in Figure 1, you can tell that as the group number increases, the price per gallon increases. There are several reasons for this, including the refining used to process the base oil and the amount of impurities they can separate out during that particular refining process. The comparison of Group I base oils to groups II and III displays the difference in how effective the refining process is at separating these unwanted impurities.
![]() |
![]() |
So, how does this relate to the OEM guidelines for lubricating a component? The OEM recommends high quality, and did not specifically mention to use a synthetic. It’s likely a push to use a lubricant produced to meet Group II or Group III criteria, and not a synthetic.
CLARIFYING ‘TURBINE OIL’
The second hint the component OEM provides in its generic lubrication specification is to use a turbine oil. There are several turbine oils on the market today that are commonly made from either Group II or Group III base oils. But the generic term “turbine oil” is usually synonymous with a premium-quality lubricant with excellent oxidation stability, one that has been fortified with rust and foam inhibitors.
This is enough information to start searching for the component’s required lube. There are many categories of oils with these properties, but the turbine oil group of lubricants tends to have just the said oxidation-, foam- and rust-inhibiting additives and not much else. In other instances, additional rust- and oxidation-inhibited oils (hydraulic oils, for instance) may also include additives not required for this application.
EXAMINE THE ENVIRONMENT
Third, the component OEM gives you the most crucial piece of information yet. This component requires a lubricant with a viscosity of ISO VG 32 at 40 degrees Celsius (104 degrees Fahrenheit). This is not a hint. This is a specific requirement laid out in black and white. But beware, the OEM has not provided information on the operating environment of the component when using this recommended viscosity. It’s also likely that this component will end up in several climates around the world and be subjected to temperature extremes requiring lubricants outside of the ISO VG 32 recommendation.
Recognize that OEM recommendations don’t cover the broad application of their components around the globe. As stated earlier, the OEM, in this case, likely developed this requirement based on favorable conditions. It’s the task of the trained technician to recognize and adjust to an extreme condition, based on the ambient environment and the demands of the component.
CONCLUSION
Where does this leave you? You need a premium-quality lubricant, made from Group II or Group III base stock, with excellent oxidation stability and rust and foam inhibitors, and it needs to have a viscosity of ISO VG 32 at 40 C. With this information, you can now procure the required lubricant and be confident that it’s the right one.
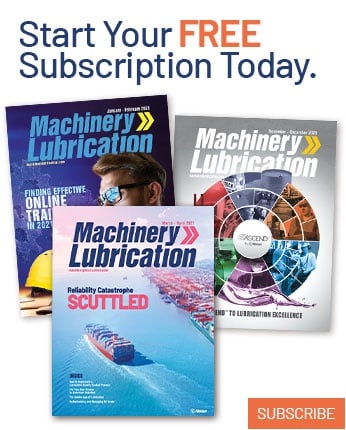