Most facilities don’t prioritize the cost of operating compressed air systems – they just want to get the job done. A recent market study1 found that only 17 percent of compressed air users valued efficiency as a compressed air system management goal. Nine percent were concerned with containing energy costs.
Seventy-one percent simply wanted to deliver a consistent, reliable air supply.
Compressed air experts have noticed that many shop-floor personnel behave as though compressed air is free, using it to blow excessive oil off machined parts, sawdust off woodworking devices, dust off the floor, etc. In reality, delivering compressed air requires expensive equipment that consumes large amounts of electricity and requires substantial maintenance.
The initial cost for a 100-horsepower compressor can run from $30,000 to $50,000, and it can consume $50,000 in electricity annually. At the same time, annual maintenance costs can be as much as 10 percent of the initial cost of a system.2 Still, the same source reports, “Many facilities have no idea how much their compressed air systems cost on an annual basis or how much money they could save by improving the performance of these systems.”
For many facilities then, improving compressed air efficiency is a golden, overlooked opportunity to not only save money in energy costs, but to achieve an even more reliable compressed air supply.
Figure 1.
First, know your system
In improving the efficiency of a compressed air system, it is important to view your system as just that, a system. When you change one thing in the system, that change affects everything else. For example, fixing a leak will increase the pressure in the system, making other, smaller leaks bigger. So, repairing leaks and eliminating other cases of what is called artificial demand (unproductive air use) is not a complete solution by itself. Lowering artificial demand must be dovetailed with strategies for improving energy use and improving your control system. The first step is to know your system, its requirements and how those requirements might be adjusted for energy savings.
Determine your operating costs
The principal costs of operating a compressed air system are maintenance and power. Maintenance costs can be determined from your asset management system or by auditing payments to your compressed air system service contractor, if you use one.
Options for determining your system’s electricity costs:
- Calculate operation running at full load, using the compressor motor nameplate rating (in break horsepower), the motor nameplate efficiency (or an estimate), annual hours of operation, and cost of electricity per kilowatt-hour. Annual electricity cost is the product of these four variables3
- More precisely determine full-load electricity consumption and, subsequently, energy costs by using a clamp meter or multimeter to measure current and voltage into the compressor at full load
- Use a power logger to determine real power usage in kilowatts and test for power factor
Determine demand requirements
Estimate your compressed air load profile in terms of how demand in cubic feet per minute changes over time. Facilities with varying load requirements often can benefit from advanced control strategies, while facilities with relatively brief periods of heavy demand can benefit from air storage options.
To establish a load profile, measure flow and pressure throughout the system under different demand conditions. Note the effect of various loading on the compressors. Significant variations in operational requirements may require a day or more of monitoring. You can use a data logger to gather and store demand profiles and power consumption profiles. This will show you when and why peak and minimal demands occur.
Record system pressures
Use pressure gauges, a pressure/airflow meter or a pressure module attached to a digital multimeter to take measurements at various points in the system:
- Compressor inlets (at the inlet filter)
- On lubricated systems, the differential across the air/lubricant separator
- The inter-stages on multistage compressors
- Pressure differentials across various components (e.g., aftercoolers, dryers, filters, etc.)
Record system flow
Use a handheld airflow/pressure meter or a mass-flow meter to measure total flow at various places in the system and during different shifts.
- Determine air consumption during operations
- Establish benchmarks to measure improvements against
- Estimate leak load during non-production
Log system temperatures
Use temperature to evaluate system health. Generally speaking, equipment that runs hotter than expected is not performing optimally and needs servicing. For maximum efficiency, use an infrared thermometer to record surface temperatures of the following components:
- Aftercooler outlet temperatures – remedial action may be necessary if aftercooler outlet air exceeds the maximum inlet temperature of 100 degrees Fahrenheit
- Outlet air temperatures of rotary, lubricated compressors. Normal operations require temperatures less than 200 degrees F
- Inlet air temperature at compressors
Take a system approach to improvements
The three basic strategies for improving the performance of industrial compressed air systems are to lower artificial demand, improve control strategies and improve energy use. Keep in mind that progress in one area will likely affect the other two, making this an ongoing process.
Lowering artificial demand means repairing leaks and finding different ways to perform tasks that waste compressed air. Observe shop floor practices and look, for example, for the use of system air for cleaning parts and equipment. Then, educate personnel that compressed air is not free.
The first step in leak control is to estimate leak load. Some leakage (less than 10 percent of capacity and power) is to be expected, but leakage of 20 to 30 percent is both common and unnecessarily wasteful. Determine leak loads as a benchmark to compare improvements against.
Since control systems vary, so do methods for estimating leak load. If yours is a system with start/stop controls, simply start your compressor when there is no demand on the system (between shifts, or during an off-shift if your operation is not 24/7). Take several readings to determine the average time to unload the loaded system due to leaks.
Leakage (%) = (T x 100) ÷ (T + t), where
T = on-load time (minutes), and
t = off-load time (minutes)
In systems with more complex control strategies, place a pressure gauge downstream of the receiver and estimate the system volume (V, in cubic feet), including all secondary receivers, mains and piping. Again, with no demands except leakage on the system, bring the system up to its normal operating pressure (P1, in psig). Select a second pressure (P2, about one-half the value of P1) and measure the time (T, in minutes) it takes for the system to drop to P2.
Leakage (cfm free air) = [(V x (P1 – P2) ÷ (T x 14.7)] x 1.25
The 1.25 multiplier corrects leakage to normal system pressure, thereby accounting for reduced leakage with decreasing system pressure.
Once you have this benchmark, you can find and fix leaks by using an ultrasonic leak detector that recognizes the high frequency hissing associated with air leaks. This method of detection is faster and less messy than the old way of applying soapy water with a paintbrush to suspect areas.
The most common area for leaks is at the point of use. Pay special attention to couplings, hoses, tubes, fittings, threaded pipe joints, quick disconnects, FRLs (filter, regulator, lubricator combinations), condensate traps, valves, flanges and packings.
Improving control strategies, including adding components such as demand expanders (pressure/flow controllers), should occur in conjunction with controlling leaks and other artificial demands.
The goal is to provide the plant with compressed air at the lowest stable pressure while supporting unexpected demand with adequate high-pressure air storage. Replenishing stored air should use minimal compressor horsepower.
Monitor compressor use and look for:
- Compressors running needlessly;
- Compressors, other than trim compressors, running at less than full load;
- Operations that fail to maintain relatively low average pressure; and
- Operations that sometimes deliver less than minimum system requirements.
Through leak repairs and improved control strategies, you may be able to eliminate one or more large compressors (in multi-compressor systems), significantly reducing energy usage. You may also add back
a small compressor to keep the system charged during low demand and eliminate the inefficiencies of large compressors operating at less than full load. Improving energy use involves improving equipment efficiency on both the supply and demand side of the system. The efficiency of the entire system depends on the proper selection, correct installation and rigorous maintenance of each component.
On the supply side, consider the following components:
- Your compressors’ prime movers
- Compressor controls
- Air-treatment equipment
- Dryers
- Filters
- Receivers
- Storage vessels
Also, it’s easy to overlook the way air tanks handle the accumulation of condensate. Some simply let water fill up, reducing capacity and risking system damage. Others have an old automated system that opens a valve on a timed basis, whether that’s necessary or not. This is basically a leak; a better solution is a valve that opens only when needed and closes as soon as the water is removed.
Finally, size and lay out the entire system so that the total pressure drop from compressor to points of use is significantly less than 10 percent of the pressure at the compressor discharge.
On the demand side, pay attention to the following components:
- Condensate/lubricant separators
- Air/lubricant separators
- Heat recovery systems
- Point-of-use systems
Tie system performance to production
Ultimately, increased productivity is the final measure of the success. Using the strategies described here, periodically correlate findings such as system output (cubic feet per minute at psig) and energy consumption (kilowatt hours) to units of production. In general, expect improvements to cause energy use to decrease unless production increases along with corresponding increases in compressed air loads. If production does not increase as pressure increases, adjust controls as required.
For more information, visit the Fluke Corporation Web site at www.fluke.com.
Notes
1See “Appendix D” of Improving Compressed Air System Performance: a Sourcebook for Industry online at http://www.compressedairchallenge.org/library/index.html#Sourcebook. Study commissioned by commissioned by the U.S. Department of Energy (DOE) with technical support from the Compressed Air Challenge (CAC).
2Improving Compressed Air System Performance: a Sourcebook for Industry: Section 12, “Compressed Air System Economics and Selling Projects to Management,” p. 69.
3See Ibid., Section 10, “Baselining Compressed Air Systems,” p. 61. and also Section 11, “Determining Your Compressed Air System Analysis Needs.”
Quantifying Energy Costs
In a typical U.S. industrial facility, generating compressed air consumes about 10 percent of the total electrical bill. In some cases, it’s more than 30 percent, at an estimated cost of 18 to 30 cents per 1,000 cubic feet of air.
Meanwhile, the efficiency of a compressed air system can be as low as 10 percent. For example, operating a one-horsepower air motor at 100 psig requires a supply of 7 or 8 horsepower to the air compressor.
Here’s how to calculate the dollar cost of compressed air:
Cost =(bhp x 0.746 x operating hours x $/kWh x % run time x % full-load bhp), motor efficiency,
where
bhp= motor full-load horsepower, frequently higher than the motor nameplate horsepower,
0.746= the conversion factor between horsepower and kilowatts,
percent run time= percentage of time the compressor runs at its operating level,
percent full-load bhp= bhp as a percentage of full-load bhp at the operating level and
motor efficiency= motor efficiency at the operating level
Suppose a manufacturing facility has a 200-horsepower compressor that requires 215 bhp and operates for 6,800 hours annually. If it is fully loaded 85 percent of the time (motor efficiency = .95), unloaded the rest of the time (25 percent full-load bhp and motor efficiency = .90) and the aggregate electric rate is $0.05/kWh, then
Cost when fully loaded = (215 bhp x 0.746 x 6800 hrs x $0.05/kWh x 0.85 x 1.0), 0.95 = $48,792,
Cost when unloaded = 215 bhp x 0.746 x 6800 hrs x $0.05/kWh x 0.15 x 0.25), 0.90 = $2,272 and
Annual energy cost = $48,792 + $2,272 = $51,064.
Source: U.S. DOE Compressed Air Tip Sheet #1, “Determine the Cost of Compressed Air for Your Plant,” August 2004.
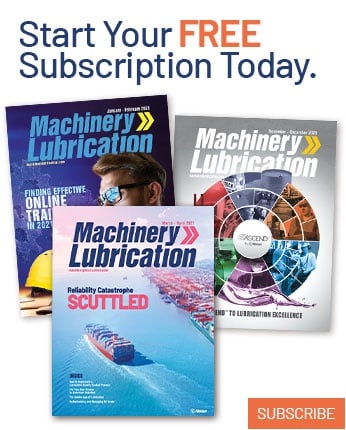