Ball bearings are crucial components in many types of medical devices, from blood analyzers and infusion pumps to dialysis equipment and aspirators. However, until now, precision-mounted ball bearings have been available with shaft diameters no smaller than one-half inch, making them unsuitable for medical equipment designed to meet space constraints.
To accommodate the needs of shrinking equipment platforms, Spyraflo Inc., an inventor and manufacturer of self-clinching and self-aligning bearing technology, is meeting the demand.
“What makes our product unique,” says chief operating officer Peter Allen, “is the fact that nobody else supplies mounted miniature bearings.”
Miniature ball bearings place special demands on bearing assemblies, Allen says. “At that size, the nature of the inner and outer race and the balls becomes very critical, partly because of the relationship between the diameter of the shaft and the speed at which you wish to rotate it.” Thus, as bearings decrease in size, the assembly into which they are pressed requires a bearing mounting hole or device with ever-greater precision.
“To install miniature bearings, designers in the past had to either produce some form of bearing mount, including a precision bearing-locating hole, or accurately machine a precision locating hole in the machine panel. Expensive machining had to be carried out before the bearings could be installed,” Allen says. “So we eliminated the need for design engineers to be concerned about precision machining and the installation of the bearing. Now we have a preassembled housing that consists of a straightforward two-bolt hole mount.”
Spyraflo’s mount consists of Annular Bearing Engineers Committee (ABEC) 3 Japanese-manufactured stainless-steel ball bearings with shaft diameters ranging in size from one-eighth to three-eighth inch. The assembly’s aluminum body and stainless-steel bearing combination result in corrosion resistance.
The design consists of an aluminum pillow block with a precision hole in the center that is produced with a tolerance of approximately 0.0002 inch, according to Allen. Then, the bearing is positioned inside the mount, resulting in precise dimensions from the base to the central line of the bearing. If the mounting hole is too large, the bearing falls out, and if it is too small, the bearing seizes up, causing the assembly to run hot at very high shaft speeds. “Thus, the diameter of the hole into which the bearing is placed is critical,” Allen insists. “And we’ve taken that concern away from the designer.”
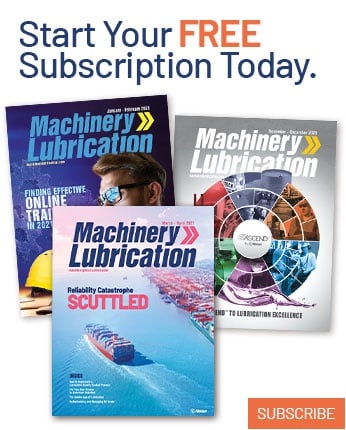