The number of industrial chemical spills in North America is continuing unabated. The U.S. National Response Center and Environment Canada report that, on average, there are more than 40,000 reported spill events annually in North America. In Canada alone, there were 175,000 tons of chemicals released into the Canadian water system in 2007 (as reported by National Pollutant Release Inventory [NPRI]).
Despite industry having a best practice for managing incidents, accidents will happen, and managers must undertake due diligence to evaluate every possible contingency.
Whether spill containment planning requires redundant systems or external containment systems, response time is elemental to minimizing the risk and its long-term effects. Many facilities entrust their spill containment procedures to offsite, third-party contractors. A time gap exists between the reported incident and the arrival of the offsite contractor. On-site, manually deployed solutions are most commonly used and often do not have enough capacity. There are several reasons why companies should invest in spill containment technology:
- Fines dramatically increased in the last five years. Ontario is one of numerous jurisdictions in North America that has adopted aggressive measures. In Ontario, it is Bill 133, the “you spill, you pay” law. In 2005, the Ontario government amended its Environmental Protection Act of 1990 to include Bill 133, whereby owner-operators and directors have legal liability in the event of chemical release. Fines have dramatically increased, up to millions of dollars.
- The cost of cleanup includes the cost of contractor, chemical removal and facility downtime. Once the chemicals leave your facility and enter the environment, you lose all control. The cost can reach hundreds of thousands of dollars.
- The regulator expects you to have a solid plan and the ability to execute it. Failure to meet compliance or be merely reactive to dynamic situations can be very costly to the bottom line, can impact shareholders and can damage a company’s public image for an enduring period.
- Insurance costs are currently very high and will skyrocket if a chemical spill occurs at your site.
- In today’s business environment, the bad press that follows a nasty spill often carries an irrecoverable damage.
- Executives and directors are held personally liable for chemical spills. Every director has to ask whether he or she can defend company practices in the court room. Is having a pile of absorbents and rubber mats in one of your warehouses a defendable practice in court?
No matter where you stand with regard to the environment, any one of the reasons above mentioned will impact you or your company in many ways.
To date, there are two methods used to contain chemical spills: manually deployed solutions and permanent immobile solutions such as dikes, oil water separators and containment tanks. The most commonly used solutions are the “magic” spill kit, but the spill kits certainly carry no magic. It takes long to deploy, they are limited to treat only small quantities, and they expose employees to hazardous chemicals. What would you use in the case of a 10,000-liter spill?
Permanent immobile systems may offer a better solution than manually deployed systems but require a large investment in infrastructure. Moreover, although each may provide adequate environmental protection in some circumstances, all have glaring weaknesses that limit their effectiveness. For example, dikes are a good way to contain chemical spills around drains, but there is a need to leave an opening to allow rainwater to drain. Therefore, when a spill occurs, the opening has to be blocked with emergency mobile solutions described earlier. Other shortcomings of using a dike are the space required and the high cost and time to complete the project.
If you could design the perfect chemical spill containment system, what features would it have?
- The solution needs to be able to contain the spill on site within seconds of detection. As long as the release is contained within the facility, a release to the environment and its potential liability will be reduced or eliminated. Consider the difference between cleaning up 10,000 liters of oil from your facility’s parking lot vs. remediation from a river or lake.
- Automation is crucial for large facilities. Automation also will decrease the amount of employee exposure to chemicals during spill containment.
- The containment system must be able to prevent any amount of chemicals from going down the drains and into the water system.
- Investment in infrastructure must be kept to a minimum. Most facilities will want to avoid digging and building on-site.
- Management capabilities: The perfect spill containment system would have C3 capabilities (command, control and communication). It should include containment control over the entire site and a communication system (e-mail, text messages, phone). This will enable the operator to contain and control the spill without ever leaving the operations room.
Case study
An example of a proactive company is St. Mary’s Cement in St. Mary’s, Ontario. Following a thorough analysis of the company’s chemical spill practices, it recently installed a state-of-the-art system. The analysis led St. Mary’s Cement to identify potential points of failure in the facility. The system that they installed addressed that issue. The map taken from the software can be seen at Figure 1. The software enables plugging drains around the facility by pressing the numbers on the map. It is important to note that the system St. Mary’s Cement chose is the one that it found best suited its needs. There are other systems available and companies have to choose the one best suited to needs.
Figure 1. Photo of St. Mary’s Cement used in the containment control software. Each number correlates to a drain controlled by the system.
Conclusion
To sum up, chemical spills have stayed the same; it is our society, awareness and rules that have changed. We can no longer hide behind the “we didn’t know” excuse. It is time for industry to catch up and put an end to chemical spills contaminating our water and soil. The technology is out there. Think of how much cleaner our water would be with a large portion of the 40,000 spills occurring every year contained. Think of all the animals and habitats we will save. Think of all the fines we will never pay.
Everyone is talking about clean energy, recycling and everything green, yet one of the dirtiest and most evident damage to the environment – chemical spills – is almost never addressed properly. We can become the leaders in changing our planet. All we have to do is step out of the box and adopt new ideas.
About the author:
Shachar Parran is CEO of ChemiGreen Inc. ChemiGreen’s wireless spill containment system (WI-Plug) provides a solution for industrial chemical spill containment. The WI-Plug system prevents spills from leaving the property and turns an emergency into a routine cleanup. For more information, visit www.chemigreen.com.
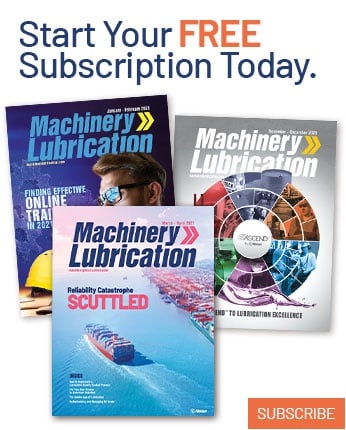