In simple terms, benchmarking is a continuous improvement tool that, in the case of lubrication, allows you to rate your company’s practices against those of the front-runners in the industry or those that are considered “world-class.” Whether you're building a lubrication program from scratch or working to improve an existing program, knowing where you stand and which gaps are most important to fill is critical.
Below are 12 top aspects of lubrication to consider. If you don't have documented processes related to each of these areas, you are likely missing a cost-saving opportunity. Once you have identifed which to improve first, you'll need the right support to get the work done. That may mean training existing employees or even outsourcing lubrication work to a service provider who can offer you skilled labor without increasing headcount.
Let's consider each area and what processes are involved.
1. Contamination control:
Contamination control plays a vital role in the overall reliability and life of any lubricated component. Control of contamination – that is to say excluding its ingression, the ability to remove it and a method to monitor it – is a holistic endeavor that begins with lubricant supplier contracts and continues to the point at which the lubricants are removed from service.
2. Oil analysis:
Often, oil analysis is viewed as a go/no-go oil change indicator. However, oil analysis can be a useful predictive tool for lubricant and machine failure. Using oil analysis to its potential will not only give you an indication of when a lubricant needs to be changed, but it can provide early warning of the contaminants (and other information) that will reduce the life of a lubricant and a machine.
3. Oil sampling:
Sampling goes hand-in-hand with oil analysis. A poor oil sample will give you poor data. As the saying goes, garbage in, garbage out. Specific methods and procedures for oil sampling need to be utilized to ensure consistent and accurate samples.
4. Lubrication practices:
The way we lubricate and relubricate our machines and components can affect their overall reliability. It is critical that we confirm the right oil is applied at the right time to the right component in the right quantity.
5. Procedures:
Procedures ensure consistency and continuity in everything we do in lubrication. It is vital to understand the difference between a full procedure and a task instruction. Procedures require enough detail for the lubrication technician to perform the task accurately. Details such as what lubricant and what quantity are required at a minimum.
Procedure creation is the perfect time to seek out the expertise of certified veteran lube techs, such as those trusted by IFM. The paramount importance of accuracy involved in creating procedures which follow best practices cannot be understated. If there is a mistake in your procedures, you should expect to witness a decrease in efficiency and an increase in downtime and even machine or component failure.
6. Standards and consolidation:
It is important that standards are applied to lubricants within the plant. Standards for cleanliness, dryness and procurement are common. Consolidation is a hot topic in many facilities that consume large volumes of lubricants. It is important to understand the risks associated with consolidation. In many cases of consolidation, concessions need to be made to apply one lubricant across different components in different environments. The risk of compromise may outweigh the benefit of consolidation. Optimization is a more strategic approach that factors the context of operation of specific machines into lubricant product decisions.
7. Storage and handling:
Your lubricant storage area is the nerve center for lubrication. Poor practices here will resonate through all other areas of lubrication. Strategic improvements in the way you store and handle lubricants will provide a solid foundation for improvements in all other areas.
8. Safety and leak management:
Safety is a priority in all areas of maintenance, and lubrication is no different. Ensuring that those involved in the handling of lubricants are fully aware of the risks and how to mitigate those risks is essential. Leak management goes hand-in-hand with safety. Proactively managing leaks will not only promote a safer working environment but will help improve overall equipment reliability.
9. Training and certification:
Lubrication is a skill-based occupation which requires significant training. Lubrication technicians today are well-educated, skilled employees that hold the responsibility of ensuring our critical assets are lubricated with precision. Therefore, training is essential and certification is required to support the skill of the technicians.
10. Program management:
Those who manage lubrication within your facility have a responsibility to manage the program with appropriate support. Ideal program managers understand the relationship lubrication has with reliability.
11. Metrics:
We all know that what gets measured gets done. Lubrication metrics are important for ensuring important areas of lubrication are not overlooked. Metrics provide a constant visual scorecard for areas in lubrication so they can be continuously considered for improvement.
12. Continuous improvement:
There is always room for improvement, especially in lubrication. Focusing on areas of poor performance, it is important to keep improving on the progress already made.
The difficulty when benchmarking your own facility is that you may not have a full understanding of what best practice or world-class means. It is required that the person conducting the benchmark analysis educate himself or herself in the 12 key areas to fully understand exactly what is considered to be industry best practice. In many cases, especially in lubrication, the aid of a lubrication professional is helpful when benchmarking. Lubrication consultants have an enormous amount of experience in many different facilities in all types of industries and have a significant understanding of exactly what constitutes best practice and world-class. A lubrication consultant can help guide you through the process of benchmarking to ensure accuracy and success.
Whether the problem is a lack of knowledge or employees heeding outdated tribal knowledge handed down through generations of workers, the results are often the same: contamination running rampant through machines, causing accelerated wear and premature machine or component failure. Contracting lubrication technicians can create an opportunity for your workers to learn from experts in the lubrication field. IFM Lubrication Technician Services offers outsourcing by experienced lube techs backed by Gaubert Oil’s arsenal of equipment.
Though there is no universally accepted methodology for benchmarking, most methods follow similar steps to achieving an accurate benchmark.
Step 1: Identify your problems areas
In many cases, understanding the areas in lubrication that you have problems with is very easy. One look into your lube room or a survey of what training and certification has been completed by the lubrication team will usually provide the answer(s) you’re looking for. Some areas, however, will require a little more investigation to uncover real problems. For example, under-lubricated bearings do not appear to have problems on the surface, but a review of bearing repairs and replacements may uncover that the life cycle of specific bearings is unusually low and the cause is a lack of proper lubrication.
Step 2: Identify other facilities with similar processes or equipment
In many industries, this can be very easy. A facility that operates in a business unit with several other facilities and shares a lot of similar and like equipment and processes will have a wealth of information within arm’s reach. Other niche facilities will have to research and investigate which companies have processes and equipment in common.
Step 3: Identify facilities that are leaders in lubrication or specific areas of lubrication
This is a very difficult task when discussing lubrication. Lubrication accomplishments are details that are rarely published and talked about. In extreme cases, some companies have received awards and industry acknowledgement for their successes in lubrication. But those that are doing well in some areas and excellent in other areas and poorly in many areas will not have anything published that lets you know. It is likely that within your own business unit, some facilities are doing things in lubrication much better than others. If you can tap into information within your own company or business unit, the leaders will likely emerge.
Step 4: Visit those facilities you consider to be best practice
Some companies are very open to having people from other companies visit their facilities and will discuss their accomplishments with pride. Other companies operate very secretly and do not allow outsiders to evaluate their processes. For instance, one brewery may not want to showcase their pitfalls and successes to another competing brewery. However, much of the equipment found in a brewery will also be found in another beverage facility not competing for market share. Also, it is always important to remember to visit other facilities within your own organization. While visiting these facilities, your task is to understand the problems they were having that led them to attain a best practice. You then want to understand what specific practices they are following for them to be considered best practice or world-class.
Step 5: Create a survey to measure your own practices
Once you have identified those that are front-runners in lubrication, you will need to measure your own facility against these leaders. Lubrication is not black and white, and the gray areas can be huge. When developing your survey, create survey questions that allow for a range of answers. Each answer will then have a weighted score based on the effectiveness of the current practice. For example, a question regarding the pre-filtering of new lubricants could have a best-practice top-score answer such as: “We always pre-filter our new oil with a filter that corresponds to our machines’ cleanliness control targets.” An answer to the pre-filtering question that would receive a zero score would be: “We do not pre-filter our new oil.”
Step 6: Implement best practices
At this point, we know what is best practice with regard to lubrication in our plant. Based on the survey results, we now know which areas of lubrication require the most attention or focus. Using the results of your internal survey, you can begin to make changes to the most critical areas on which you scored poorly. If your current staffing is not able to meet your lubrication needs, it can be helpful to talk to provider of contract lubrication technicians. Contract workers who have a strong background in lubrication are able to bring best practices to your program without the need to add headcount.
Step 7: Continuously improve
Once implementation of best practices has begun, it is important to keep the momentum moving along. One of the best ways to do this is to re-benchmark via a re-survey at predefined intervals. Administering the survey will provide valuable feedback on which areas are improving and which are still falling short of best practice.
Benchmarking provides a much-needed scorecard for areas of lubrication that may not be obvious or often considered for improvement. It is true that we “don’t know what we don’t know.” Until we move our focus beyond our own facility, we may not realize that there is a better way to do things. Benchmarking allows us to identify the faults in our own facility compared to the successes of others.
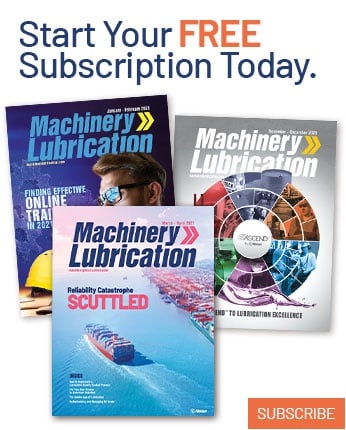