A coal-fired power plant operating in the western U.S. was experiencing short gearbox life in their coal pulverizing operation. After an annual gearbox inspection, oil analysis results indicated that the AGMA 6EP (ISO 320) gear oil recommended by the original equipment manufacturer failed to provide adequate lubrication and protection based on oil analysis results and gearbox inspection after one year of operation. This was confirmed by excessive wear metals and lower viscosity levels in the used oil reports. After further analyses of the used EP gear oil, excessive build-up of particulate contaminants in the lubricant and depletion of the EP additive package was responsible for the faulty gearboxes. The particulate contamination consisted primarily of dirt, coal dust and metallic particulates being generated by bearing and gear tooth wear, resulting in a chain reaction of excessive wear.
Pulverizer Gearbox Description and Operating Costs
The plant’s pulverizer gearbox design dates back to the early 1960s. Gearbox design consists of a steel worm gear driven by a large 800 rpm electric motor that drives a bronze bull gear directly connected to a grinding table. The sump holds 255 gallons of gear oil, with temperature controlled by an integral water-cooled heat exchanger. The unfiltered ISO 320 EP gear oil is recommended to provide lubrication to the bronze-on-steel gears and bearings.
Although this gearbox design is rugged and simple, maintenance costs were becoming excessive and maintenance outage/overhaul intervals did not support power generation schedules at the plant. In fact, typical maintenance costs and intervals for each pulverizer gearbox were as follows:
• Oil changes were required every 12 months at a cost of $5,000 in material and labor and $20,000 to $50,000 in lost electrical production, typical of most coal-fired power generation units of this time frame.
• After 10 years of operation, the bronze bull gear was rotated to expose the unworn gear teeth. This required four weeks of turnaround time and included maintenance work at a total cost of $300,000 per unit.
• After 20 years of operation, a complete rebuilding of the gearbox was required. Parts and labor for this effort exceeded $450,000 per gearbox, with lost production costing another $250,000 per pulverizer.
With 13 coal pulverizers operating at the plant, maintenance and downtime costs quickly added up.
Breaking the Wear Chain Reaction
Careful preliminary analysis of worn components indicated that the bronze gear face was experiencing significant sliding contact and spalling. As time progressed, the bronze gear face wear became more and more significant. Plant personnel began to search for a better lubrication system to break the wear chain reaction.
Plant personnel suspected that the wear patterns on the bronze bull gear faces were attributed to several factors, including high particulate loading of coal dust and dirt in the gear oil and catalytic reactions between the gear oil additives and some of the particulates generated. Additionally, chemical attack of the EP additive package during operation was creating high levels of copper in the gear oil, most likely due to sulfur-phosphorus EP additive being active on the bronze bull gear resulting in high levels of copper in the gear oil
It quickly became clear that these issues needed to be addressed. Plant personnel sought for methods to better seal the gearbox from particulate ingestion, primarily in the form of coal dust. Additionally, great lengths were taken to implement filtration methods and options for the gear oil to quickly capture the particulates and generated wear particulates, and enhanced lubricant technology (both base oil and additive packages) was applied to provide extended maintenance intervals without energy use penalties.
Problem Resolution
After a period of trial and error in which a variety of solutions were tested for effectiveness, success at breaking the wear chain reaction was achieved via particulate ingress, filtration method and customer requirements.
Particulate ingress was successfully controlled through the use of breather desiccant filters on the gearbox vents and by very close attention to the grinding table seals. Initial ISO Cleanliness Code of 23/21/18 (per ISO 4406-1999) was achieved with aggressive breather filtration. Prior to the implementation of particulate ingress, employees were unable to establish the target ISO cleanliness level due to the very high levels of particulate. Historically, the ability to filter ISO 320 and 460 gear oils in a coal pulverization environment had proven very difficult.
However, plant personnel determined that a kidney loop filtration system would be one of the better options for removing particulate contaminants from the pulverizer gearbox and addressing the gear wear issue. An effective kidney loop filtration system must have the following characteristics:
• High dirt holding capacity
• Low maintenance requirements. (Filter changes should not be needed more than monthly under normal operating conditions)
• Obvious gear oil improvement within one week pf preformed maintenance
• Continued gear oil clean-up and effective maintenance of target cleanliness code 18/15/11 per ISO 4406-1999
• Pre- and post-filtration sampling points for evaluation of filter effectiveness
• Skid mounting installation
• Suction and discharge locations designed to eliminate fire hazards, and a turnover of the entire gearbox oil sump every 30 minutes
• Filtration skid size that does not interfere with normal maintenance activities
Advances in Filtration Technology
Advanced filtration technology that would meet the above requirements for this application was determined to be readily available for heavy gear oil. An off-line kidney loop filtration package using a high-efficiency, high-dirt-holding-capacity, synthetic filter media was installed using two filter housings mounted in series with a common sized element in both housings.
The filter elements initially recommended for the trial installation were rated at Beta 25=200 in the first stage and Beta 10=200 in the second stage. Oil flow was delivered by a vane pump rated at 10 GPM for a 460 cSt (2,500 SUS) gear oil. Temperature ranges of the system fluid varied from a low of 65 degrees Fahrenheit (18 Celsius) when idle up to 130 F (54 C) during normal operation. The filtration package was installed with the suction line coming into the filter bank directly from the bottom of the reservoir and the outlet, or filtered discharge line, was piped directly into the top of the reservoir.
Presently, the filter element condition is monitored by differential pressure gauges installed on each filter housing, with a target of 25 to 28 psig as an indicator of element loading; the elements were changed out prior to allowing the internal bypass valve. Other features of the filtration package include upstream and downstream sampling valves to allow gear oil samples to be taken without having to shutdown the system.
Advances in Lubrication Technology
Over the course of the system update, it was recommended that an AGMA 6EP (ISO 320) gear oil for pulverizer gearbox be included in the system design. Evaluation of the wear patterns on the gear teeth indicated that the EP additive package in this gear oil was too active on the bronze bull gear and in conjunction with the contaminants in the gearbox, was causing premature wear and failing to provide adequate protection for the gears. Analysis of used gear oil samples confirmed that the EP additive package was being depleted from extended contact between the steel on bronze gear face and sliding wear. IR thermographic imagery indicated that this extended contact between time resulted in higher gear face temperatures. What’s more, very high dirt and particulate loading was confirmed by the ISO Cleanliness Code.
After consulting with the lubricant supplier, it was determined by all parties that AGMA 7 R&O (ISO 460) synthetic gear oil would best protect the gearbox in this application. The higher viscosity grade and improved lubricity of this synthetic gear oil, coupled with R&O additive chemistry, was able to provide a higher oil film strength than that recommended by the OEM, and would extend the life of the gearbox, taking into account the temperature requirements and gearbox longevity. The physical properties of the synthetic gear oil are shown in the table.
In the past, plant personnel considered the feasibility of using a synthetic gear oil in the pulverizer gearbox, but determined the high dirt loading in the gearbox made these uneconomical with frequent oil changes. However, with recent filtration improvements enabling a potential oil life of at least three years, the economics of using a synthetic gear oil could be justified. The synthetic ISO 460 R&O gear oil offered several benefits, including:
• Enhanced pumpability at lower temperatures and with enhanced filterability
• Higher oxidation resistance and thermal stability
• Higher film strength at high and low temperatures
• Extended service life in a clean, filtered environment
Operational Results
In the end, the pulverizer gearbox was overhauled and all major rotating components were replaced except for the steel/worm gears. The gearbox was wiped clean and dried with lint-free rags as part of the overhaul process. The steel worm and bronze bull gears were precision aligned and blue checked. The reservoir was flushed with an ISO 460 mineral oil and was then filled with the synthetic ISO 460 gear oil. A baseline gear oil sample was drawn from the reservoir and analyzed for particle count per ISO 4406-1999, with ISO Cleanliness Code results coming in at 23/21/18. Finally the pulverizer gearbox was put into service along with the filtration system. Following three hours of run time, the particle count was reduced to 21/19/11.
After 48 hours of run time, the plant installed a set of Beta 5=200 filter elements in each housing to further reduce the system contamination and achieve target ISO Cleanliness Code 18/15/11 more quickly. The pulverizer gearbox and filtration system continued to run for another two weeks with element condition being monitored using differential pressure gauges. As a result of using the 5-micron media during these two weeks, the target ISO Cleanliness Code 18/15/11 was reached.
Filter element service life was also monitored during the trial installation; results showed that the high-dirt-capacity media exceeded expectations given the initial clean-up of the system. Plus, the service life during ongoing usage has been beyond expectation. In fact, during the trial installation, oil samples were taken and analyzed for physical and chemical properties, particle count and analytical ferrography. The results showed the wear metals were reduced significantly and the oil cleanliness was maintained.
Conclusions
Given the success of this initial installation, the power plant continues to achieve the following benefits by using the ISO 460 R&O synthetic gear oil and new filtration system:
• Significantly improved gear and bearing lubrication
• Minimal to non-existent wear metals in the gearbox based on the oil analysis reports
• No increase in drive motor energy consumption thanks to a higher viscosity synthetic gear oil (some plant instrumentation measurements indicated a 1 percent drop in motor amperage with 4160 VAC motors)
• Accurate predictive/proactive maintenance using particle count and analytical ferrography
• Extended gear oil life that provides the additional benefits of reduced disposal costs and reduced environmental impact/waste oil generation
• Significantly extended gearbox life
• Eliminated contamination related downtime
• Extended maintenance intervals
Since applying the lubricant upgrade and filtration package and closely monitoring the results, the power plant purchased and installed their second unit in the fall of 2005.
Acknowledgements
• John Kinion and Maintenance personnel, Pacificorp Naughton Plant, South U.S. Highway 189, Kemmerer, WY 83101
• Chris Tully, Project Engineer, Pacificorp Naughton Plant, South U.S. Highway 189, Kemmerer, WY 83101
• Ken Knochel, Technical Services, Schroeder Industries LLC, 580 West Park Road, Leetsdale, PA 15056
Mechanism for Reducing Wear Particulates and Extending Gear Life in a Coal Pulverizer Gearbox Page 6 of 7 Winslow, Naman, Nicholas
References
1. ISO 4406:1999. Hydraulic fluid power. Fluids. Method for coding the level of contamination by solid particles
2. ISO 16889:1999 Hydraulic fluid power filters. Multi-pass method for evaluating filtration performance of a filter element
3. Sheffield, Schroeder Industries, "Changes in Filtration and Contamination – Switching Directions for the Filtration Industry". Machinery Lubrication Magazine, January 2005
Appendix I
8120-3Feb05.pdf
Mechanism for Reducing Wear Particulates and Extending Gear Life in a Coal Pulverizer Gearbox Page 7 of 7 Winslow, Naman, Nicholas
About the authors
Ken Nicholas is the director of lubrication market services at Schroeder Industries. Richard Winslow is a senior lead engineer at PacifiCorp’s Naughton power plant in Kemmerer, Wyoming. Ted Naman is the technical coordinator for industrial lubricants and greases at ConocoPhillips.
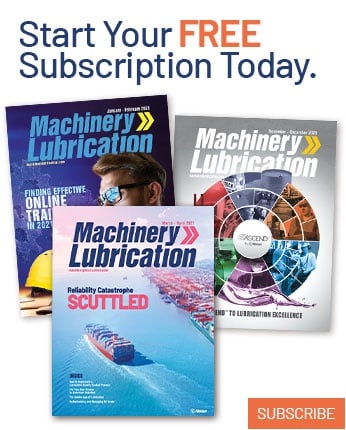