![]() |
![]() HondaJet in Flight |
Program Update
In preparation for first flight of conforming aircraft in the first quarter of 2010, Honda has completed major structural assemblies including the fuselage, wing, empennage, landing gear and other components for the first conforming aircraft. These components were completed or delivered in September 2009. Fabrication of conforming aircraft has commenced under the strict supervision of Honda and FAA quality control representatives, while Honda's manufacturing engineering team focuses on the optimisation of assembly processes.
Honda also has completed successfully a number of important qualification tests, such as rejected take-off (RTO) brake tests and crew- and cabin-seat crash tests, as well as critical structural parts tests.
Honda continues to work very closely with the Federal Aviation Administration (FAA) regarding certification of the HondaJet and completed an Interim Type Certification Board Meeting (ITCBM) in August 2009. A formal agreement has been reached and implemented with the FAA regarding the manufacturing conformity process for the type-certification test aircraft. This process currently is being used for the build of the first conforming aircraft. In addition, Honda and the FAA are engaged in detailed discussions to finalise the requirements for the first Type Inspection Authorization (TIA), which allows the start of FAA flight testing.
To expedite the build of conforming aircraft and establish precise, high-quality fabrication processes, Honda has chosen to manufacture conforming aircraft wing assemblies at its R&D complex on its world headquarters campus in Greensboro, N.C. In addition, in-house cutting-edge 5-axis milling capabilities provide Honda with maximum efficiency and the highest quality in the creation of detail parts for conforming aircraft fabrication.
Honda also has completed preparations for on-site static and fatigue structural testing. Honda's advanced MTS FlexTest structural test system incorporates 61 hydraulic actuators and a 2,600-channel data acquisition system within a structural test fixture designed exclusively for HondaJet testing and capable of testing the entire aircraft to prove static and fatigue strength under various flight and ground load conditions. Honda's test facility includes an environmental chamber to simulate hot-wet conditions, which is required testing for the validation of composite structures.
"We are pleased to have achieved such positive results in the completion of major structural assemblies for conforming aircraft, and we are now fully focused on final assembly of the first conforming aircraft. We are now ready for FAA structural testing. Although we face many challenges ahead, every Honda associate is diligently working towards first flight early next year," said Michimasa Fujino, Honda Aircraft Company president and CEO.
New, Advanced HondaJet Avionics Suite
The production HondaJet flight deck will feature a Honda-customised Garmin G3000 next-generation all-glass avionics system incorporating a class-leading layout with three 14-inch landscape-format screens and dual touch-screen controllers for overall avionics control and flight plan entries. The HondaJet Avionics Suite provides a significantly enhanced pilot interface compared to flight decks incorporating the previous generation Garmin G1000 Suite.
The HondaJet Avionics Suite is the most advanced glass flight deck available in any light business jet and provides state-of-the-art integrated avionics functionality featuring split screen MFD capability, satellite weather, graphical synoptics, digital audio and optional Synthetic Vision.
"The HondaJet Avionics Suite, integrated into our human-centric cockpit design, represents a significant enhancement in both capability and user experience. The large-format displays, advanced features, and intuitive touch-screen multi-function controllers provide a low-workload user interface that is ideally suited to our high-performance light jet aircraft," said Fujino.
Advanced Systems Integration Test Facility (ASITF)
On October 7, Honda Aircraft Company accomplished the successful first flight of the HondaJet Advanced Systems Integration Test facility (ASITF) located within the company's R&D complex on its Greensboro, N.C., campus. This event represents a critical milestone for the HondaJet program and is another significant step toward the first flight of conforming aircraft. The HondaJet ASITF facility was developed internally by Honda Aircraft Company engineers.
The HondaJet ASITF is an aircraft systems integration facility, primarily consisting of two major elements: the aircraft test facility, and the Real-time Test and Simulation System (RTSS). The HondaJet ASITF is a test facility that incorporates actual aircraft systems hardware and software, installed in a spatially-representative manner, and interconnected with actual aircraft electrical harnesses. The RTSS provides the systems, environmental and aerodynamic simulation, supported by dSPACE real-time hardware and I/O hosting Honda-developed high fidelity 6-DOF aerodynamic and real-time engine models. Additional simulation capabilities have been integrated to provide real-time simulation of navigation RF data, including GPS.
The HondaJet ASITF also includes a fully representative primary flight control system with a high-fidelity control-loading system. The avionics configuration during the HondaJet ASITF first flight included the new HondaJet Avionics Suite.
"The HondaJet ASITF has successfully integrated the best attributes of a systems test lab, engineering simulator, and 'Iron Bird' in one facility," said Fujino. "This facility allows thorough evaluation of all systems integration for enhanced aircraft safety and will significantly support accelerated development of both systems and conforming aircraft."
HondaJet Cabin Management and In-flight Entertainment System
Honda Aircraft Company has confirmed that the production HondaJet will optionally offer EMTEQ's SkyPro integrated cabin management and in-flight entertainment system featuring all-digital high-definition touch-screen interface technology. The HondaJet cabin management and in-flight entertainment system will include audio/video on demand (AVOD), interactive 3-D high-definition moving map, and extensive cabin control capabilities such as cabin/cockpit communications, climate control and interior lighting, among others.
AVOD is available through the system's removable media storage unit, which is capable of storing virtually an entire media collection. Passengers can interface through the onboard system's multiple media inputs with audio, video, or gaming systems brought onto the aircraft and play content on cabin speakers and HD monitors. HondaJet also will offer an XM® Satellite Radio option, where the system will interface with XM and allow passengers to select their desired station presets at their seats.
"The concept HondaJet cabin management and in-flight entertainment system was exceptionally well-received by customers. In order to meet strong customer demand, we will offer on the HondaJet a class-leading system with a unique Honda-designed interface providing maximum functionality and ease of use," commented Fujino.
Flight Ready Maintenance Service Program
Honda has unveiled its HondaJet Flight Ready maintenance service program, which is designed to maximize flying time and minimize variations in maintenance costs. Flight Ready makes HondaJet-authorized materials and maintenance services available when and where customers need them. Program participation allows aircraft owners to plan on one hourly maintenance rate based on selected coverage and tailored to expected aircraft utilization. The program offers three levels of coverage to meet the diverse needs of HondaJet customers.
Flight Ready Protection - P¹ ("P-One") is included in the purchase price of all new HondaJet aircraft. In addition to other OEM support services, it provides a comprehensive warranty program including airframe, avionics and engine warranties.
Flight Ready Performance - P² ("P-Two") is designed for customers who have access to facilities with qualified and trained technicians. It provides various services, including airframe and avionics exchange component coverage that extends to both scheduled and unscheduled maintenance events.
Flight Ready Precision - P³ ("P-Three") was created for customers who want the convenience of one-stop servicing. In addition to coverage in the P² plan, it also includes labor expenses for scheduled and unscheduled maintenance performed at authorised HondaJet maintenance facilities. This plan is Honda's "Nose-to-Tail" service option.
All HondaJet Flight Ready plans are fully transferrable. Extended engine coverage - provided through GE Honda Aero Engines - is available up to full engine overhaul, including all major components and systems.
HondaJet Production Facility
Construction of the HondaJet production facility on Honda Aircraft Company's world headquarters campus in Greensboro has begun with the completion of ground preparations and the commencement of piling installations. The 250,000-square-foot facility is scheduled to be completed in February 2011 and will house all HondaJet production activities, as well as test flight operations and pilot training facilities. Honda has partnered with Flight Safety International to provide pilot training utilising industry-leading full-motion Level-D flight simulators that will be installed in the HondaJet production facility.
While construction of the production facility continues, Honda's world headquarters building and R&D complex on campus are in full operation. Build of conforming aircraft currently is taking place in Honda's 187,000-square-foot R&D complex that also incorporates ongoing research and development activities. The R&D complex has full production capabilities, including all necessary quality control and testing resources, paint booths, and maintenance support facilities. The HondaJet world delivery center also is located within Honda's R&D complex.
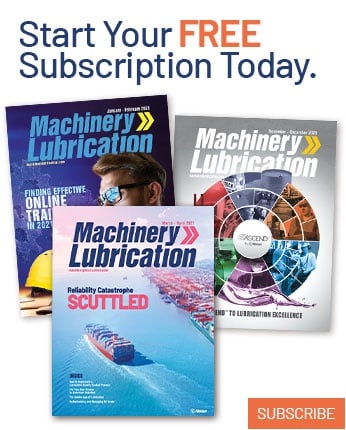