The breathtaking speeds in Formula One are achieved with the help of advanced tooling block technology.
There is no doubt that precision engineering is a linchpin of Formula One racing. Indeed, in the relentless quest for greater speed, a constant objective of F1 engineers is to make their teams’ cars lighter. This is achieved by using carbon fiber materials throughout the car. Apart from the engine and tires, virtually everything else, including the steering wheel, seat, chassis, and even the fire extinguisher bottle, is manufactured from this incredibly strong, yet extremely lightweight material.
Trelleborg supplies the vast majority of F1 teams with epoxy tooling blocks, which constitute the starting point of the process in carbon fiber component manufacturing. “It’s basically a three-step procedure,” says Chris Mellings, manager, AEM Sales Group, Trelleborg, Skelmersdale (UK). “A F1 customer would block our boards together with a specially formulated industrial adhesive before putting it on a five-axis CNC machine to profile it into the desired component shape. The product is then sealed to create the master mold.
“From the master mold, the customer makes composite tooling using pre-impregnated carbon fibers cured in an autoclave. Once it hardens, the result is a composite laminate that is exactly the profile of the master mold itself. From this composite tool, the customer develops the individual carbon fiber component,” explains Mellings.
Trelleborg offers a range of seven different tooling blocks, of which the TB650 is used by approximately 75 percent of F1 teams. Considered the highest quality tooling block in the market, it has been made by Trelleborg since the mid 1970s.
“Our boards deliver a valuable combination of benefits, namely superior stability, low density, high-quality surface finish and very good machinability,” says Mellings. “It is this unique blend of attributes, together with an increasingly automated process of tooling block manufacturing, that sets us apart and puts us in pole position to supply F1 for many years to come.”
Looking at tooling blocks
Tooling blocks are essentially a combination of epoxy resins, glass microballoons and hardeners, which are mixed together and cured in an oven until hard. They are cast into standard size “boards”, which are joined to form a block larger than the component to be made.
For larger components, a key factor is the actual weight of the tooling blocks. Trelleborg supplies an option weighing 400kg/m³, effectively half the weight of standard market variants.
Equally important in component manufacture is the co-efficient of thermal expansion (CTE), since any level of expansion during curing would result in the shape of the final component differing from the original master mold. Therefore, a lower CTE equates to a reduced probability of expansion, something of paramount importance within Formula One, aerospace and similar sectors requiring ultimate precision.
As industries move away from older manufacturing methods to a more hi-tech approach, new application areas for composite materials, and hence epoxy tooling blocks, are emerging. The European tooling block market is currently valued at around 11 million euros and tooling blocks are supplied to a growing number of sectors in which composite components are manufactured. These include a broad section of transport applications, including rail, marine, aerospace and general automotive; sporting goods manufacture, such as tennis rackets and golf clubs; and increasingly, the renewable energy industry, most notably wind farms.
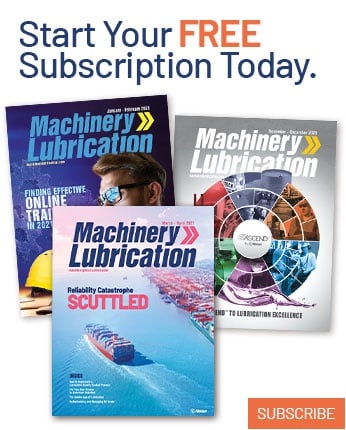