We are all aware of the impact outages have on business. In many cases, as much as one-third to one-half of the maintenance budget is consumed during this timeframe. Factor in the cost of lost production during this time and the costs are tremendous. To offset the cost of lost production and the cost of maintenance, we have to maximize the amount of work accomplished in the shortest amount of time, yet at the same time be effective in what work is performed and how it is managed.
Outages can have elaborate schedules, but often are unsuccessful due to ineffective advanced planning, which results in inefficient work execution and outage schedule overruns. Outages can only be successful when the outage work is planned effectively before the work is scheduled and/or started.
Many maintenance organizations, in an attempt to manage their outages more efficiently, have created planner positions to address outage work planning. However, more times than not, the planners end up running certain sections of the outage, managing contractors or running down materials; little or no advance task planning takes place. Thus the success of the outage is still questionable.
This article will focus on four of the eight areas of planning that are often overlooked or ineffectively addressed. If outage planners are given the opportunity to concentrate their efforts on effective outage task planning and address these eight areas, scheduling and execution of outages will have a much higher success rate. The eight areas for consideration are:
- Determination of outage tasks
- Task scope definition
- Identification of task hazards or obstacles
- Task step methodology
- Determination of materials, tools and equipment
- Work group coordination
- Labor resource estimation
- Task planning completion
This paper covers four areas: determining outage tasks, defining task scope, identifying task hazards and/or obstacles, and completing task planning completion. This in no way diminishes the importance of addressing the other four areas or their overall impact on the successful completion of an outage.
Before we progress further, we need to establish several baseline definitions. First, what is the objective of an outage? The objective should be to accomplish the identified tasks with a high level of precision, so that equipment and or processes restart with minimal problems or scrap losses, and operations will have the confidence that equipment and processes will operate at desired rate and quality until the next scheduled outage.
Second, what is the objective of outage planning? Outage planning’s objective is to minimize the impact of delays, waiting, obstacles and bottlenecks during work execution to allow on-time completion of work and on-time equipment/process startup while managing outage planned costs within the outage budget.
Here are several facts that reinforce these objectives. Maintenance shutdown costs can be reduced by 30 to 50 percent from historical levels if startup after the shutdown occurs smoothly and predictably. Since 1973, operating and maintenance costs for power production plants have increased by more than 400 percent. Many plants spend as much as 40 percent of their maintenance effort on reactive tasks.
Potlatch Cloquet’s paper mill implemented low-cost maintenance shutdown management techniques focusing on type, quality and timing of work, which contributed to an 83 percent drop in maintenance cost per ton(1). It is vitally important that the outage work list be kept as short as possible.
Keeping the list short is both the means to reduce costs and the primary method of focusing on work that can only be performed during a major outage. All other work should be addressed during a time outside of the outage window.
“Companies that are running truly optimized schedules, on average, have improved work orders completed per day per technician by 20 percent, service contract compliance by 25 percent, and increased wrench time by 18 percent.”(2)
When a facility decides to identify major outage work far in advance, and the work is carefully planned to maximize ease of execution, the result will be lower costs. Outage work task identification starts the day after startup from the last outage. Here is a suggested planning timeline:
3 to 10 years out: Rough work list developed
18 to 24 months out: Work list reaches the budget, and planning commences
12 months out: Monthly outage meetings begin
6 months out: Work list is locked down. Planning is 90 percent complete
0 month: Outage occurs, 100 percent of work is planned and scheduled
1 month post outage: Post-outage critique meetings occur
Successful maintenance organizations identify their outage work list from various sources, all of which should be in alignment with the outage objectives. These sources include:
-
Work requests generated as a result of the post-outage critique meetings. These requests capture work items that were identified during the previous outage.
-
Regulatory issues generate additional work and in some cases drive the frequency of many outages.
-
Outage and equipment history should be another major source of identification of outage work items.
-
PM/PdM activities, backlog or carryover work from previous outages.
The planning process can commence, once the outage work list has been established and approved. The key is that outage work task identification is critical and successful outage planning and scheduling depends on important events occurring far in advance.
In the timeline, we state that the work list should be locked down six months prior to the outage. The lockdown date is essential to effectively managing and planning outage work. If a lockdown process is not in place there will be a never-ending flood of last-minute work items being added to the outage that will not be planned, and this will result in excessive costs, reactive response and increased probability of outage schedule overrun.
Part delivery issues and labor availability become a problem when work is added after the lockdown date. The implementation of a lockdown process is a concept that some individuals may find difficult to accept, especially if in the past they have been allowed to add work with no regard to the impact on the overall outage budget and schedule. A process to address add-on outage work must be developed and in place that requires the requestor to justify the need and identify what existing work items will be sacrificed.
Management must seriously enforce the lockdown time frame, following the established process and gain agreement from all parties that it will be followed. Any work proposed for addition after the lockdown date should be carefully scrutinized and justified before approval. It is important to remember that planning work is expensive. It is extremely wasteful to cancel a job that is already planned (with parts on order or onsite), in order to do unplanned work.
As outage tasks are identified, the task scope has to be defined. In many instances, the identified work task is all the scope that is provided. In this case, workers assigned to accomplish the work are at a disadvantage, because they are left to determine the scope based on their knowledge, which may not be the intended scope at all. When this occurs, inefficiencies, delays and costly overruns usually result.
Clearly defined work scope is essential to successful outage planning, scheduling and work execution. If the following questions are answered, a clear work scope will result:
- Does the work request adequately define what the task expects to accomplish?
- Is there a specific starting and ending point for the task?
- Will this require testing or acceptance criteria to be met?
- Will the task impact health, safety or environmental aspects?
- Who or what department will have the final say on the priority of the work?
As a part of defining and refining the scope of work, the planner will be required to conduct site visits at the location of the requested work to determine the five basic elements of work planning:
- The labor requirements (how many, skills, how long) for the task
- The specific location of the work (asset and physical location)
- When the work needs to happen (sequence in the scheduling process)
- The materials, tools and equipment to perform the work
- The information, specifications, safety, permits that support quality work execution.
To accomplish this level of planning, it is very important that adequate personnel be dedicated full time to the planning of outage work packages. If this is not done, planners most likely will be placed in the role of supervisors, craftsperson, parts-chaser or all-around go-fer. None of these activities will increase the efficiency of maintenance activities at the magnitude that effective advance planning will provide.
Previously, we stated that outage planning’s objective is to minimize the impact of delays, waiting, obstacles and bottlenecks during work execution to allow on-time completion of work and on-time equipment/process startup while managing outage planned costs within the outage budget. To meet this objective, advance planning must be thorough. The identification of job hazards, safety issues and obstacles that impact job progress is often overlooked.
All can be avoided or taken into account if addressed during the planning process. Some of the most common items include the complexity of the lockout/tagout, permit requirements (line breaks, confined space, excavation and building permits), air and water discharges, barricade requirements (will the barricaded work area interfere with normal traffic patterns?), and whether the work site will support equipment weight and height requirements. These items cannot be fully considered if work planning is done on the fly or planners attempt to plan from their desk. Site visits are an essential part of effective outage planning.
As the planning process approaches the six-month cutoff date, the outage work planning should be finishing up. Work packages should be fully planned and usually waiting on identified parts and materials to arrive. How do we determine that we have completed the planning process for the outage work?
First, all of our outage work should be managed through our work order process. With that in place, we can evaluate each work order with a series of questions that, if we answer them truthfully, will determine if the work order planning has been completed. The evaluation process should include these questions:
-
Is the scope of work clear, concise and easily understood?
-
Have all aspects of the task have been evaluated and addressed?
-
Have the job hazards, safety, permit requirements and potential obstacles been identified, addressed and communicated within the work order?
-
Does the task sequence make sense, is the methodology defined, and does it include special instructions, specifications and testing/quality checks?
-
Have all determinable material, parts, tools and equipment requirements been addressed and actions taken to provide the necessary items with delivery within the prescribed “need by” dates?
-
Have the specific work groups been identified and the coordination of task steps been addressed to minimize non-value effort?
-
Have realistic labor estimates and labor resource requirements been established using the best methods available, including task duration and total labor hours?
-
Do all work packages include all supporting documentation, prints, schematics and pictures?
If the planner can truthfully answer “yes” to each of these questions, there will be confidence the work package will fulfill the objective of outage planning. The end result, when the work order is scheduled and executed, will be more work being executed with fewer people and in far less time.
The repair quality will increase and the cost for each repair will significantly decrease. In some cases, the cost savings could be as high as 90 percent. On average, an unplanned repair work order that would take eight hours to complete can take less than two hours to execute when planned. This is due to a combination of better instructions, easy access to parts, tools, equipment and materials, and better coordination of labor resources.
Experienced outage planners come up with great tricks of their trade. Identifying these tools help them to manage their time more efficiently thus allowing them to provide a better planned outage. Several of their experiences include:
-
Sorting their work lists by work groups (crews). It is easier to manage than working from the entire backlog.
-
Developing spreadsheets of piping systems that require blinds to be installed, then tracking when a blind has been installed and when the blind is removed. This can prevent many headaches during startup.
-
Identifying tasks that require scaffolding and, where possible, have the scaffolding installed prior to the outage start date. Again, this reduces the potential for delays waiting for installation.
-
Include notes to schedulers about jobs that may be under a crane lift. This will reduce delays or safety issues of working under suspended loads.
An outage is a unique situation. Effective planning can provide Maintenance the opportunity to accomplish work under controlled circumstances resulting in more work completed, precision work accomplished, startups that are controlled with minimal losses, and equipment or processes that run reliably at desired quality and rate until the next scheduled outage.
All work that is placed on the outage schedule must be fully planned. If this is not done, it effectively places the burden of planning the job on the craftsperson. This slows the work tremendously and creates numerous opportunities for delays, mistakes, confusion and unsafe acts.
We have covered four of the eight items that directly impact the effective execution of an outage. Our discussion has specifically focused on the planning process and not on the scheduling process, because scheduling depends on knowing how much work is available, how long each task will take, how many labor resources are required per task, and the priority or criticality of the task. Each of these factors is directly related to how effectively the planning has been performed.
Effective outage planning will result in a meaningful schedule that can then be developed with a high percentage of probability that it will be successful. However, the success of a schedule depends on the execution of the work. Scheduled work expectations have to be communicated to the supervisors and workers responsible for work execution with progress monitored daily. Daily schedule updates are essential; without these updates, on-time completion of the outage is in jeopardy.
Outage management is an effective tool for reducing costs and increasing plant productivity. When the decision is made to identify major outage work far in advance and then carefully plan the work for maximum ease of execution, the result will be lower costs. If, at the same time, disruptions to the process (such as late add-on work) are kept under control, there will be sufficient resources available to continually refine and improve the outage model for even greater savings.
References
Kister, Timothy C., and Bruce Hawkins. Maintenance Planning and Scheduling: Streamline Your Organization for a Lean Environment. USA: Elsevier, 2006
Brown, Michael V. Audel Managing Maintenance Planning & Scheduling. USA: Wiley Publishing, 2006
(1) Krings, Dave. “Proactive Approach to Shutdowns Reduces Potlatch Maintenance Costs.” http://www.idcon.com/article-approach.htm
(2) Vigoroso, Mark. Field Service Optimization Benchmark Report. Aberdeen Group, May 2005.
About the author:
Tim Kister is a planning and scheduling subject matter expert at Life Cycle Engineering. Tim’s practical experience in the application of best practices allows him to assess client work control practices, develop processes, training and coaching strategies to influence cultural changes that optimize the client’s transition to a proactive culture. A dedicated educator, Tim has facilitated more than 100 workshops and seminars focused on maintenance management and planning & scheduling, and has co-authored the book “Maintenance Planning and Scheduling Handbook; Streamlining Your Organization for a Lean Environment.” You can reach Tim at tkister@LCE.com. For more information about LCE, visit www.LCE.com.
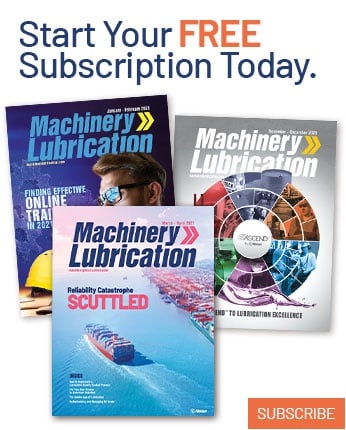