Goodrich Corporation recently completed the first test assembly of the GP7200 engine in its preparation to support production activity for the Airbus A380 program. Engine
In addition, Goodrich installs engine build-up kits consisting of the: pneumatics and starter systems; hydraulic and fuel systems; pylon drain; fire extinguisher; and several electrical harnesses are also installed, including the Variable Frequency Generator (VFG) harness.
Finally, Goodrich installs a package of Airbus Buyer-Furnished Equipment on the bare engine which includes: engine mounts; thrust links; hydraulic pumps; fuel and hydraulic lines; pressure valves; and VFG. The VFG itself has Goodrich origins. It is manufactured by Aerolec, a joint venture between Goodrich and Thales. While compact in size at 19.7 inches by 11.8 inches and 143 pounds, the VFG plays a key role on board the A380, producing electricity for the entire aircraft.
According to Jean Luminet, president, Goodrich Aerospace Europe, "Our team is proud to be part of another milestone in the development of this very high profile aircraft as it makes its way into the global fleet. We're also pleased with our team's application of Lean Manufacturing tools and practices which allow us to continually meet our customer's deadlines. Planning for the GP7200 engine assembly began as far back as January 2005 and involved a delicate balance of many technically challenging tasks. We even had to modify our infrastructure to accommodate the assembly. For example, we installed pedestals, as well as an ergonomically designed shipping stand for 'marrying up' the propulsor and fan cowl."
In addition to providing the build-up of the GP7200 engine for the A380, Goodrich has a number of systems and technologies on board the aircraft. The company's evacuation slides played a key role in the Airbus A380 full-scale evacuation test which was successfully completed this past March in
Goodrich, as one of the world's largest suppliers of landing systems, also provides both the main body and wing landing gear for the aircraft. Though Goodrich was already a major supplier for Airbus, it was the first time the company had been selected to provide landing gear for an Airbus aircraft. The components for the landing gear system are produced by Goodrich's Landing Gear division and involve manufacturing facilities in
Goodrich's innovative High-Density Discharge (HID) and LED-based exterior lighting and flight controls, that take advantage of the latest power-by-wire technology, are also on board the aircraft. And Goodrich will provide the primary and standby air data systems.
Goodrich is also supplying an automatic ice detection system, and will bring its experience in aircraft materials and structures to bear in the development of the aircraft's cargo system and with several structural components.
Goodrich's Aerostructures team also provides the sail fairing, or Rear Secondary Structure, an aerodynamic surface that serves to reduce drag associated with the trailing edge of the A380's pylon. It also encloses a number of aircraft systems which must be easily accessible through various doors and removable panels. The company provides the aft pylon fairing, which also reduces aircraft drag and protects the primary and secondary pylon structures from temperature extremes. In addition, Goodrich will provide the center and rear fan case sections as well as the engine sensor suite for the Rolls-Royce Trent 900 engine option on the A380.
Furthermore, as the A380 enters service, Goodrich's Component Support network and Maintenance, Repair and Overhaul facilities are being equipped to provide the aftermarket services necessary to keep the A380 in the skies.
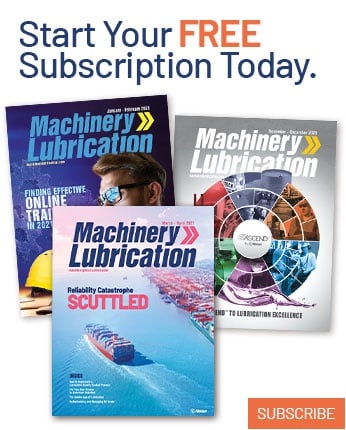