It has been 12 months since you completed implementation of your plant’s enterprise asset management (EAM) system and celebrated the system “Go Live”date.
You accomplished all the right things during the implementation. You employed an experienced EAM implementation consultant. You formed an internal implementation team to provide input and complete tasks. You documented business processes. You gathered data and entered it into the EAM. And, you conducted training sessions. But, the EAM is not providing the information required by the various function managers to support business decisions.
What went wrong? Where do we go from here? Is it the system, the data or the people? Is the required information contained in the system and if so, how do we access it? What do we, as the EAM system administrators, do to correct this problem?
These are just a few of the questions that are asked by every organization when decision-making information is needed and seems to be unavailable. If this situation continues, upper management may begin to question the logic behind the purchase and implementation of what is usually an expensive system. They will soon be asking when the return on investment (ROI) will be realized, or if it ever will be realized. System users will begin questioning whether the new system is better than no system as before. Support for continued system usage may decrease, or may be questioned.
Regardless of what may have gone awry, you can determine how to get more from your EAM. It may just be a case of determining where to look. It may also just be a case of what to look for. All EAM systems contain the same basic capabilities in support of your maintenance, reliability and materials functions. How you implement and use these capabilities will determine what data is available when needed. You must first develop a plan of action (Where do we go from here?).
The following (in no priority order) are several of the basic activities that should be included in your plan.
1) Determine what business decisions are to be made and what information is needed to support these decisions. Excessive effort can be expended reviewing and updating system data only to learn that it is not needed for decision making. Determine the format of the data requirements and document these requirements so that all parties involved will remain focused on the same objective(s).
2) Conduct a review of the system implementation to determine if an area was overlooked or not completed. Did you skimp in one area in order to complete an area that was perceived to have a higher priority? Did you complete all the actions the plan called for? And, did the implementation consultant do what he or she was contracted to do?
3) As stated, all systems contain the same basic capabilities; however did the selected system support your documented business process or did you attempt to change your processes to fit the system? A successful, results-producing EAM will be implemented to fit the plant business processes. Review the business processes and ensure they are being followed as documented. Review the EAM implementation to ensure it supports the documented processes.
4) Review the EAM users’ manual that was developed during the system implementation. This manual should contain procedures to be used by various roles when using the EAM system. Are the system users following the established procedures? Do the procedures collect and record information that can be used for decision making? Do the procedures require revision to ensure meaningful data is being collected? This manual should also have been used as the basis for training users.
5) Review training records to determine if training sessions were conducted for each role level and that all system users attended this training. Review training materials to determine that the system user’s manual was used to develop the training materials. Talk with system users to determine if refresher training is needed. If necessary, schedule refresher training for all system users.
6) Review the tools used during the system implementation to collect data to be uploaded into the EAM. These may be in the form of manual spreadsheets, electronic databases or a combination of the two. In some cases, this data may have been provided by the supplier/vendor. Include the following in your data review: nameplate data for assets (equipment), materials inventory data, preventive and predictive maintenance procedures, employee (worker) data, etc. Review the process followed when uploading this data into the EAM system. Was this process complete and thorough?
7) Review the system codes developed in the EAM system in support of the business processes. Were they entered correctly? Do they support the decision-making process? Are the system users employing them correctly? Do these codes require modification in order to provide data necessary for decision making?
8) Review each system module to determine the standard fields available for recording data. Determine if these standard fields, when populated correctly, will provide the requested information. Determine whether the capability exists to create additional fields in the various modules. Determine if additional fields were created during the system implementation and if they are documented in the system user’s manual.
9) Review each module contained in the EAM system to understand the completeness and applicability of the data contained. The various modules should include: asset (equipment), inventory, task list (PM/PdM procedures), work orders, asset history, etc. Determine if the system users’ manual described what data was required by each module and how to enter it properly. Determine if training was conducted to ensure that each user understood these requirements and their importance.
10) Determine what standard reports are available from the EAM system. Use the system users’ manual developed during the implementation to determine if data fields contained in these standard reports were addressed in the various procedures for data collection and entry. Compare the fields of these standard reports with the information required by management to determine if the correct data is being collected, entered into the system and retrieved by the reports.
11) If necessary, enlist the aid of an information technology (IT) representative to create custom reports to attempt to retrieve the requested data from the EAM system database. Use the requirements of management to develop these reports. Determine from these reports if the data is being entered in the correct format and if it is being entered into the correct record field. These reports should indicate if data is available to support the business decision-making process. If the data can be retrieved, the decision must be made whether to keep the report format and have it available for use by others or to maintain it as a special report to be used when necessary. If data cannot be retrieved, it is an indication that more investigation or possible system modification may be required.
This list of activities is a starting point for getting more out of your EAM system. Not all activities may apply to your system. The system in use and the business processes established will determine what activities must be undertaken and in what order they should be accomplished. For all necessary activities, it’s important to complete them in their entirety and properly document results. Continue to ask questions until you receive answers or the situation is corrected. Most importantly, document the results and re-communicate and train all users. Make it important!
We can also determine from this activity list that an EAM system is a software package (tool) that requires and, in some sense, demands the discipline of any corporate software package. This tool will not be effective unless people receive proper training, use the system according to defined processes and provide feedback for continuous improvement. An EAM system is like any other software package – its success depends on how it is implemented and, more importantly, how it is used.
About the author:
Mike Willard, CMRP, is a senior consultant for Life Cycle Engineering (LCE) with more than 30 years of maintenance and reliability experience. Throughout his career, Mike has worked with industrial, facilities and government organizations to implement reliability processes within various work streams including work control, planning and scheduling, reliability engineering, materials management, operator care and EAM systems. You can reach Mike at mwillard@LCE.com. For more information on LCE, visit www.LCE.com.
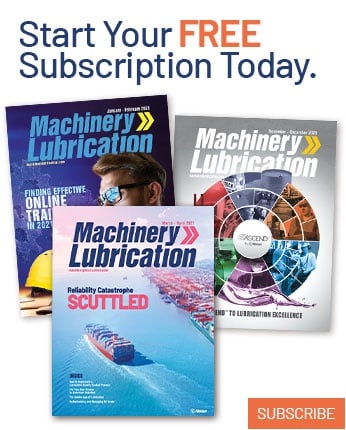