Regenerative thermal oxidizers (RTOs) and other types of thermal oxidation systems have proved to be a highly effective and energy-efficient method of abating volatile organic compounds (VOCs) and other pollutants emitted by industrial plants. However, particulate matter in the emission stream can be a particularly vexing problem resulting in the fouling and plugging of media beds. Therefore, careful attention should be given to selecting the shape and material of the heat exchange media to mitigate potential problems with particulate matter and to ensure reliable, economical and safe operation of thermal oxidation systems.
Regenerative Thermal Oxidation
Thermal oxidizers are essentially incinerators that thermally or catalytically convert pollutant-laden emissions into carbon dioxide and water vapor. The oxidation process typically achieves better than 99 percent destruction/removal efficiency (DRE) levels for VOCs, hazardous air pollutants (HAPS) and odors.
Regenerative thermal oxidizers minimize fuel consumption by “regenerating” or reusing heat generated by the system. Fans draw air from paint-booth collection systems and other sources, and the air is pre-heated by heat exchanger media to the thermal oxidation temperature, typically 1,400 to 1,600 degrees Fahrenheit. The air then moves into a combustion chamber for the specified residence time (0.5 to 2.0 seconds), where an exothermic reaction takes place, converting the VOCs to carbon dioxide and water vapor. Prior to being exhausted to the atmosphere, the hot, purified air passes through a media bed to capture heat energy that will be used to pre-heat incoming air. Valves continually alternate the flow between media beds: a cycle with incoming cool air into a media bed that has just been heated by hot exhaust, followed by a cycle with hot exhaust air flowing through the media bed to reheat it.
RTOs can operate at thermal efficiencies of 85 to 99 percent, reducing or eliminating the need to burn natural gas in the combustion chamber. RTOs are particularly effective for process streams with low to moderate solvent loading and can being self-sustaining at moderate lower explosive limit (LEL) levels. In other words, once the system is sufficiently heated, the natural gas burners can be turned off if enough flammable gas is present in the exhaust stream.
Other Thermal Oxidizers
For lower solvent loading levels, below 4 percent LEL, a catalytic system is often recommended. A regenerative catalytic oxidizer (RCO) has a similar design as an RTO, except that the ceramic heat exchange media closest to the combustion zone is coated or impregnated with precious metals that function as a catalyst that enable oxidation at significantly lower temperatures (600 to 1,000 degrees Fahrenheit). A catalytic system requires the presence of the type VOCs that will oxidize at these lower temperatures. RCOs utilize the same principle as catalytic converters in motor vehicles that oxidize carbon monoxide and unburnt hydrocarbons to carbon dioxide and water.
For exhaust streams with high LEL levels, a simple thermal oxidizer can be used, without any thermal regeneration capability. In such cases, high solvent loading can support combustion without pre-heating and often with very little or no burning of natural gas.
For air streams with relatively low VOC concentrations, rotary adsorbers can be used to concentrate the stream and increase LEL level, to enable the use of an oxidation device that is smaller and/or more energy efficient. The pollutant-laden process exhaust passes through the rotary adsorption unit where the VOCs are adsorbed on zeolite or activated carbon media. The purified air is exhausted to atmosphere, and the solvent is then removed from the media by desorption with a smaller stream of hot air, which is then delivered to an oxidation device.
Upstream Particulate Removal
Although oxidizer systems are used primarily for the abatement of VOCs, all emission streams contain some quantity of particulate matter, and these particles can lead to bed fouling, performance degradation and even to dangerous and destructive fires. Some methods of upstream particulate removal methods include cascade (water wash), baffle and media filtration. Others, such as wet and dry electrostatic precipitators (ESP) and cyclone dust collectors, can reduce, but not eliminate particulate matter entering the RTO.
Impact of Particulate Buildup
Particulate that penetrates deeper into the media bed will tend to burn off. However, chemically reactive particles can cause problems even when they penetrate deep into the media.
A portion of the particulate that enters the RTO will collect on the cold face of the media bed. Depending on the design of the media, the particulate build up can rapidly lead to plugging of the media bed. Plugging causes several significant problems. Blocking airflow results in a rise in pressure drop, forcing the induced draft fan to work harder and consume more electricity. The capacity of the RTO is reduced, as the media bed becomes less effective at transferring heat, because “dead zones” mean reduced surface area exposed to the air stream and less media mass available to retain heat energy. Moreover, build up of particulate presents a serious fire hazard.
The only remediation solution for these symptoms is wash-out or bake-out of the media bed, processes that involve costly downtime. Over time, the frequency of wash-out and bake-out procedures typically increase until the only viable solution is a complete media change out.
Types of Media
Over the past few decades, several different types of heat transfer media have been used for RTOs. Three main categories are random packing, monolithic structured block and corrugated structure packing.
Random packing: Originally, in the 1970s, a wide variety of random packing materials were employed in RTOs, including gravel, ceramic balls, and shapes of all kinds. The packing material was randomly dumped into the RTO to form a media bed. Random arrangement was preferred in order to prevent nesting that would constrict flow and cause dead areas that collect particulate.
In the 1980s, RTO manufacturers and owners discovered that the ceramic “saddles” developed for chemical mass transfer operations provided an optimal shape for RTO random packing. Relative to other types of random packing, the saddle shape minimized pressure drop (for lower electricity consumption by the induction fan) and maximized surface area (for higher heat transfer efficiency).
Over the years, RTO media suppliers have refined the design of ceramic saddles. For example, Koch Knight LLC has developed a unique 3-rib Low Pressure Drop FLEXISADDLE® Random Packing design (or LPD® Random Packing), which provides a high open area and aerodynamic design that limits nesting and reduces pressure drop by 20 percent compared to standard saddle media. [See photo]
Several manufacturers coat or impregnate this LPD saddle with a metal catalyst for use in RCOs. The FLEXISADDLE packing is also available in a glaze resistant Alumina to resist exposure to alkaline chemical attack, which may result from cleaning chemical fumes or the metallic salts used in electroplating applications.
Monolith Structured Block: Another alternative for very clean, low particulate streams, such as the imported Cordierite ceramic honeycomb monolith, is available from Koch Knight LLC. Monolith block is a form of structured packing that is placed in a formal arrangement, rather than randomly dumped. Cells extend through the block in a straight channel perpendicular to the cold face.
The advantage of this design is that it theoretically provides a straight, aerodynamic channel for the air stream. The disadvantage is that if particulate plugs a channel at the cold face, where the inflow enters the block, then this entire channel becomes a dead zone.
Corrugated Structured Packing: The most advanced ceramic heat exchange media for RTOs is corrugated structured packing, developed by Koch Knight engineers. [See photo] FLEXERAMIC® Ceramic Structured Packing is constructed of corrugated sheets of ceramic. The angle of inclination of the corrugations of adjacent sheets is reversed, ensuring excellent distribution of air flow throughout the media bed. Even if an area of the media bed became plugged by particulate, the mixing and spreading effect of the alternating corrugation prevents down zones above the plugged area.
Field studies have shown that, upon installation, RTOs with corrugated structured packing consume the same amount of natural gas as RTOs with monolith structured block, although the former has superior air flow distribution, and the latter has slightly higher heat storage capacity. The advantage of the corrugated solution becomes dramatic over time because of the vastly superior ability to resist fouling caused by particulate buildup.
Life-Time Cost of Operation
Owners of thermal oxidizers have a number of options available when installing a new system or replacing the media bed of an existing system. For VOC abatement systems in the finishing industry, where particulates can be a concern, corrugated structured packing should be considered. This advanced solution may cost more to purchase and install, but it will provide lower pressure drop, higher heat transfer efficiency, more reliable operation, and longer useful life compared to the alternative media. The significant long-term reduction in energy consumption alone can far outweigh the additional cost of installing advanced heat exchange media.
About the author:
Paul Sims is Southeast Region Sales Manager at Koch Knight LLC. He can be contacted at paul.sims@kochknight.com.
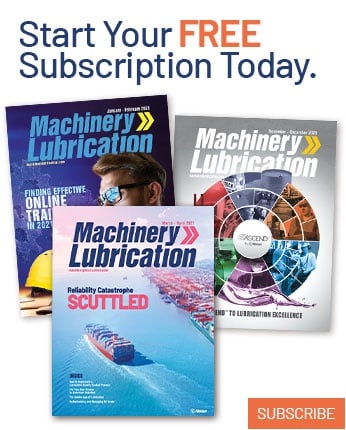