There appears to be an ongoing shift toward operator involvement in machine relubrication practices. During my last several seminars, I’ve asked the audience to identify themselves if their plants have plans to involve operators in lubrication practices. I recently inquired into the details of the lubrication practices at a few of the plants represented and was surprised to hear there were no prescheduled lubrication practices (the work is entrusted to mechanics and lubrication specialists). This is not advisable even when the technicians are dependable and have a high degree of knowledge. It spells trouble where there is a pending change in responsibilities. While some machine types are forgiving of leakage and low volumes, that certainly is not the case for high-speed equipment.
Machines fail with differing rates of degradation. Machines with high loads and high speeds can go from a state of constancy to a state of disaster in moments. The higher the machine speed (surface interaction) for a given time, the quicker a machine will fail. Load is relevant. Assuming a given speed, higher dynamic loading increases destructive forces and destructive potential. Nonetheless, even lightly loaded machines can self-destruct rapidly. High speeds and high loads provide the equipment operator with little to no margin of error. This is the case with high-speed blowers, fans, turbines and various other similar applications.
“Best practice” for machine lubrication requires all of the following criteria:
- Proper handling and care of the lubricant throughout its life cycle
- Proper selection of the product by viscosity, additive structure, stiffness (grease) and product performance capability
- Proper resupply of the lubricant by volume, frequency, cleanliness and application method
- Proper analysis of the lubricated system
- Proper management of the lubricant following placement in the machine
While all of these are necessary to achieve long-term reliability goals, one item in particular has the power to interrupt production without warning: lubricant resupply. The degree of influence that resupply has on the drive train is dependent on machine speed and load for the reasons stated above.
The resupply requirement for liquid lubricant sumps is intuitive, perhaps even obvious. Oil-filled sumps generally have external level indicators. Nearly all either have internal or external indicators. Many sumps, including gearboxes, bearing baths, and circulating and hydraulic system, can run at borderline acceptable levels for a brief period. Given these parameters, the majority of oil-filled sumps should be observed on a daily to weekly basis, at the very minimum weekly. Machines with higher criticality, forced feed systems and/or higher speeds (greater than 2,400 RPM shaft speed) should be checked more frequently. Systems with high machine criticality limits should receive shorter intervals. The guideline box below suggests the maximum time between inspections.
Table 1. Grease Interval Correction Factors
Resupply for grease-lubricated components is more difficult, and the poor reliability of greased components (i.e., bearings, gears, cables) bears this truth out. Since grease-lubricated plain surfaces are relocated to slow surface velocities, resupply volume and frequency decisions mostly pertain to various types of element bearings.
The question of volume can be somewhat easily answered based on surface area (for sliding contacts) and/or volumetric (for rolling contacts) replacement. SKF provides a simple formula that is suitable (for element bearings):
Volume Q = W x OD x F
Where: Q = Volume in ounces
W = Bearing element width
OD = Bearing element outer diameter
F = .114, the replacement factor for imperial units (it’s .005 for metric)
Table 1. Grease Interval Correction Factors
With the question of volume provided as a constant, bearing dimension and machine operating conditions influence relubrication frequency. FAG Corporation has provided a simplistic formula that incorporates common machine environmental factors for the baseline regreasing interval in hours, as follows:
t = K • [[(14•106) / (n•(d1/2))] – 4•d]
Where: t = hours between relubrication events
K = product of all correction factors (Ft•Fc•Fm•Fv•Fp•Fd)
n = RPM
d = bore diameter (in millimeters)
F = correction factor (see Table 1)
When plugging numbers into the equation, a negative product suggests that grease relubrication is a poor option, and should be avoided. Since there are no ready visual indicators of the condition of the grease lubricant within the sump, it’s difficult to tell when the matrix between the oil and the thickener is degrading. Further, it’s impossible to judge localized oxidation, degradation and deposit formation, and it’s impossible to judge contamination conditions at the dynamic interfaces. All of these factors can dramatically degrade lubricant effectiveness, regardless of what may seem evident from the outside.
Grease durability itself will influence whether the interval is a best fit or not. Bearing greases can be rated by service life, as is shown in Table 2. Since grease lubricants degrade at differing rates, it’s important to understand grease life-cycle measurement and how that information should be used to modify the frequency calculation.
Remember, with high speeds and loads comes high risk of failure from poor top-up and resupply practices. Assign a timeline and reinforce those practices, especially if there is a planned shift toward operator involvement.
References:
“Grease Service Life: Theoretical Considerations and Practical Applications.” Weigand, M; Vadic, T; et al; Lubcon, GMBH.
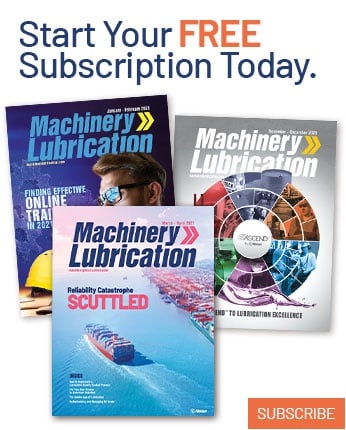