Too often in reliability engineering, we focus narrowly on equipment and equipment-related problems when tasked with removing variation from our manufacturing process. But, what about “human reliability”?
Human reliability is defined in the Springer Series in Reliability Engineering as the probability that a job or task will be completed successfully by an individual within any given stage of a process, within a given timeframe. Human error (reliability) occurs when the individual’s mental-models are not aligned with current circumstances. This misalignment is caused by the person’s prior knowledge of the process or system and the fact that the system or process has changed. So we ask the question, how can training limit variation?
It’s fundamental, really. As our systems or processes change, so must our understanding of the asset and how it is used. Even if our task analysis indicates that the individual is performing the same task, we must retrain each person on the new circumstances.
For example, we train operators on how to start, load and stop a pumping system, and they then demonstrate those competencies every day. However, what if the pumping system function changes from a fresh water application to a viscous slurry application? Will the procedure for starting, loading and stopping change even though the operator is performing the same tasks? Yes, because the application of the pump has changed and now requires new knowledge of how to slowly, incrementally load the pump to prevent overloading the drive motor when the slurry makes contact with the pump impeller.
Training helps to minimize variation due to human performance by effectively illustrating the differences between new and old circumstances, and by teaching individuals how to let go of the old and embrace the new.
Training, in a manufacturing process, should be an evergreen process or program. In lean manufacturing, your organization is in a constant state of change. This is, after all, the definition of continuous improvement. Standards of practice for operators or maintainers continually evolve as innovations and more efficient practices are revealed and implemented. Therefore, your program for training operators and maintainers must be evolving as well.
Follow these steps to improve your training program in order to minimize variation due to human error:
1. Verify that a job-task-analysis (JTA) is required within the pre-commissioning checklist of your improvement/installation process.
2. Modify this JTA to ensure that a functional comparison is made between existing and future asset applications, identifying the new skills required.
3. Develop an auditing process that is capable of determining if individuals are operating the asset the old way, or if they have effectively changed their mental models to the new.
4. Refine your training program to include routine evaluations of the asset and how it is expected to function within the manufacturing process.
For more information on managing assets by criticality, contact Life Cycle Engineering at www.LCE.com.
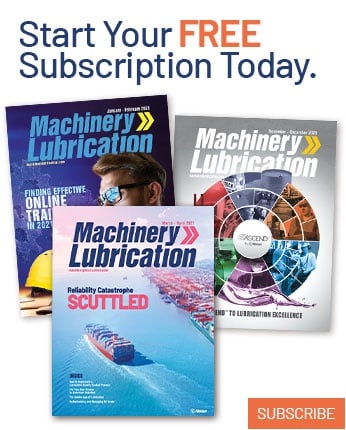