Manufacturing plants use a wide variety of power tools. From electric drills and impact wrenches to reciprocating saws and air chisels, power tools are utilized throughout the facility by maintenance and production workers. But, how are your power tools distributed to these plant-floor employees? How are your employees using a particular tool? How are they expected to access it? And, how does an employee find a tool when it isn’t where it’s supposed to be?
An electronic locker system can house power tools, hand
tools and a myriad of other MRO (maintenance, repair and
operations) products.
Speeding up the process of distributing power tools on the shop floor eliminates a great deal of downtime. Effectively tracking where the tool was used, who used the tool and what it was used on can take the guesswork out of the life and journeys of that power tool. Using a point-of-use distribution device that enables the employee to easily access needed tooling on the shop floor, and leaves him or her with the mind-set that they are accountable for its return, can overcome most of the difficulties associated with power tool distribution.
![]() |
Hunting for power tools can be a pain, and replacing “lost” ones can be expensive. Point-of-use electronic lockers make it easy to find and return these items. |
THE TYPICAL SCENARIO
At some plants, tool crib personnel are responsible for issuing and receiving a tool.
But what if the machine it will be used on is a half-mile away at the other end of the shop? The maintenance or production employee needing the tool must shut down the machine they are working on and walk to get that tool from the crib. Is that an effective use of time and a way to get the most production possible from that machine? And, what if that employee walks to the tool crib and the crib manager says, “Somebody must have gotten that on the afternoon shift yesterday and didn’t write it down.” The crib manager then starts walking to try and find the drill. All the while, the technician or operator still has the machine shut down. The crib manager finds out that Joe had the drill but gave it to Melissa on rolling mill No. 4 and she hasn’t brought it back. So, the crib manager walks again to find Melissa.
This scenario is very common for facilities that don’t have an effective way of distributing power tools. A huge amount of time is wasted chasing them around.
![]() |
LOCK THEM UP
Electronic lockers are an effective solution for securely storing, tracking and distributing power tools.
A number of companies that specialize in inventory management solutions have taken the “school-kid” locker concept to the industrial workplace, and a number of different types of systems are available. Some lockers are similar to those you
had in high school, but these attach to machines that vend keys to enable access. Other lockers are electronic and driven by software. These track every movement
of the tools that they distribute on the shop floor.
Both types of systems allow point-of-use distribution, so a plant employee no longer encounters lengthy downtime because he or she has to walk a half-mile to the tool crib. Both types of lockers increase your ability to distribute tools on the shop floor. Software-driven lockers, though, have advantages over manual, key-type locker systems.
Software-driven models are ideal for not only distributing tools, but also for tracking usage and tool movement.
Electronic lockers allow you to:
- securely store your tools with easy access
- set security for product access control
- track tool usage by cost center
- easily return the item to the locker
- automatically generate tool usage reports
- eliminate theft
- give users a feeling of accountability
- reduce stockouts
REDUCE THEFT,
MISSING TOOLS
Any manufacturing facility that uses power tools on a daily basis knows how costly it is to replace tools and how frustrating it is to hunt for tools. With electronic lockers, your operation immediately puts an end to missing tools and begins instilling a stronger sense of accountability among employees. Tools no longer float from machine to machine on the shop floor, or get deposited in lunch boxes when the shift is over.
How can storing tools in lockers reduce theft and missing tools? Just storing them in lockers won’t. A software-controlled locker system is more than a storage unit. A good electronic locker system tracks a tool’s every movement.
For instance, if Joe takes a cordless drill from the locker at noon and another employee walks to the locker and finds the tool gone, he or she can easily access the software with a touch screen monitor to find out who currently has the tool.
When employees know that everyone can see who used the tool last, their care for the tool increases. If something did happen to the tool, your employees are more inclined to report it at the time it happens. A responsible employee isn’t going to take a tool home or let someone else on the shop floor use the tool, knowing that the lockers have logged him or her as the person currently using it.
SIMPLE AS 1-2-3
It’s easy to use electronic lockers. Here are the steps that Joe would follow:
- He walks to the electronic lockers and types his password on the touch screen, or scans his employee badge with a bar-code scanner.
- The touch screen shows him the tools he can access.
- He selects the tool he needs and the locker door opens automatically. There are no keys to lose before he returns the tool.
When Joe is finished using the tool, returning it is also easy.
- He walks to the lockers and scans his badge or enters his password.
- He selects “return mode” and the touch screen shows him all of the tools for which he is currently accountable.
- He selects the tool he is returning.
- The electronic locker door opens, he returns the tool and he is no longer accountable for it.
Simple operation sets the electronic locker system apart from key-operated devices.
QUESTIONS
AND ANSWERS
At the start of the article, you were asked, “How are your power tools distributed? How are plant employees using the tool? How are they expected to access it? And, how does an employee find a tool when it isn’t where it’s supposed to be?”
When answering those questions earlier, did your answers make sense? Did each answer include the word “effectively”? And, are you comfortable with the way your company is distributing power tools? If you answered “no” to any of those questions, you and your plant need to rethink its current system.
Electronic lockers could be the solution. System setup is nearly “plug and play,” and a good electronic locker system enables your organization to take total control of its power tools and stay in control of its budget. You’ll get to the next level of tool control without a great deal of time and money.
Robert Holmes is the marketing director for WinWare Inc. For more information, e-mail robert.holmes@wwga.com and visit www.cribmaster.com.
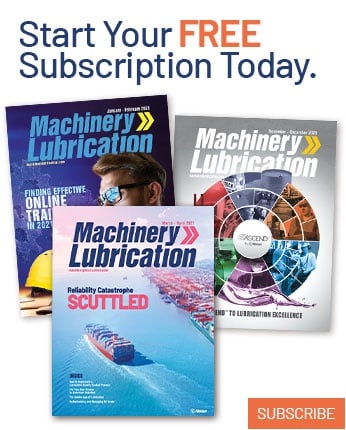