Electric motors in U.S. industrial applications account for more than 60 percent of electricity use; even small increases in efficiency improvements can make a big difference in energy savings. Two new motor technologies now available commercially offer breakthrough efficiency and reliability opportunities for industry.
The copper rotor motor technology offers high efficiency, performance, and reliability.
Copper Rotor Motors are ‘Ultra-Efficient’
A new line of motors featuring the copper rotor motor technology has entered the U.S. industrial market, providing significant energy savings potential for manufacturers. Siemens Energy & Automation’s induction AC motors include die-cast copper rotors which offer increased electrical energy efficiency, lower operating temperature, extended motor life, and reduced weight and size. In fact, these ultra-efficient motor designs have total losses that are 6.6 to 15.5 percent below those of comparable NEMA Premium efficiency motors while exceeding the NEMA Premium full-load efficiency standards by up to 1.4 percent.
The die-cast copper rotor motor technology is the result of several years of research and development by both the Copper Development Association Inc. (CDA) and Siemens to achieve superior efficiency by substituting copper for aluminum in the squirrel cage induction motor. CDA led the way on manufacturing processes and high-temperature mold materials to enable cost-effective production of copper rotor motors. The Siemens project team developed design methods and conducted an extensive modeling program to optimize the motor for the high conductivity copper rotor. The result is a motor technology that offers high efficiency, performance and reliability. According to the CDA, in the United States alone, a 1 percent increase in motor efficiency could save 20 billion kilowatt-hours (kWh) per year, or $1.4 billion in electricity (at 7 cents per kWh).
Siemens was instrumental in bringing the technology to the commercial market. The company incorporated the high-conductivity copper rotors into their motors, which include aluminum and cast-iron frame models. Other improvements include optimized rotor and stator design, low-friction bearings, redesigned cooling system, polyurea-based grease, dynamically balanced rotors and precision-machined mating surfaces for reduced vibration. Specially designed insulation enables use with variable speed drives. The new line of motors is available up to 20 horsepower.
Motor Controller Increases Efficiency and Improves Comfort
A new technology for variable speed control of single-phase AC induction motors in HVAC fan systems provides a low-cost, energy-efficient solution for indoor climate comfort and noise reduction. The Adaptive Climate Controller from Opto Generic Devices V-HVAC Inc. uses multiple, closed-loop signals, analog optical-based control, and sensor input to deliver climate and moisture control, healthy air quality, and proven electricity savings of 30 to 50 percent.
With help from DOE’s Industrial Technologies Program Inventions & Innovations program, Opto Generic Devices (OGD) Inc. created an optical programmable encoder and controller combination that offers:
- Continually adaptive/variable speed
- Optimized commutation
- Dynamic vector control
- Real-time feedback
- Application tuning
- Signal enhancement for operating AC motors
Based on this technology, OGD’s subsidiary, OGD V-HVAC, developed the Adaptive Climate Controller (ACC) (PDF 399 KB) (Download Adobe Reader). This unique technology is an alternative to digital controllers that can be complex, expensive, and can cause motors to run hot and generate noise. This intelligent and adaptive controller maintains temperature for the human comfort zone by gently mixing room air depending on needs of the space. By gradually ramping up fan speeds, energy is conserved by using only the electrical and thermal energy necessary to satisfy the demand. In addition, noise from electrical, motor and air flow is reduced.
The ACC technology was commercialized in 2005 and has sold more than 2,500 units. Projected annual energy savings from the technology is 2.9 million Btu of electricity per 5,000 units.
This article appeared in the Summer 2008 issue of Energy Matters, the U.S. Department of Energy’s newsletter.
Read more Energy Matters articles on these topics
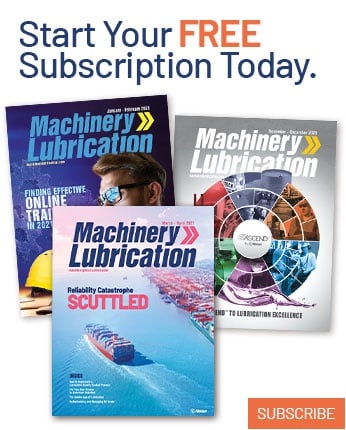