Facing rising energy costs, corporate fiscal concerns and global competitiveness, more and more U.S. companies and utilities are focusing on the leading reliability and maintenance improvement opportunity in industrial facilities: electric motors. A sound reliability-centered motor maintenance program can help manufacturers achieve significant energy and cost savings. This article outlines steps to help you implement a program at your company.
Establish a motor maintenance management plan to save energy and costs.
Why Consider Motor System Management?
Since the 1990s, a variety of motor management program ideas have been presented to industry. Many of these programs are actually “energy-efficient electric motor retrofit-or-repair-versus-replace” ideas, and they represent only a small portion of all the opportunities for managing electric motor systems. Preventive and condition-based maintenance, and other motor system management techniques, are often left out of such programs, creating a narrow view of the overall system. A complete motor maintenance curriculum considers all aspects of the motor system, including energy, environment, life-cycle costs, and a robust reliability and maintenance (R&M) program.
A survey of motor decision-makers found that more than 70 percent emphasize reliability as the first consideration of their motor programs (see Figure 1). Even in the current environment, which stresses energy efficiency, the first priority for a plant in a reactive failure condition is getting equipment back online and in production. More than 60 percent of companies are operating their R&M practices in a reactive mode, so energy policies related to manufacturing and support equipment have become secondary. However, with a proactive R&M program in place, companies can improve energy efficiency and extend the life of the equipment, boosting the bottom line.
Figure 1. Survey of Motor Decision Considerations
Source: H. Penrose, Electrical Motor Diagnostics and Motor Health Study (2003).
The impact of a full reliability-centered maintenance and management (RCMM) program for motor systems is multifold. In the United States alone, approximately $1.2 trillion is invested annually in maintenance programs; up to $750 billion of that amount is the direct result of poor R&M practices. An additional $2.5 trillion in potential business opportunities is lost per year as a direct result of poor R&M practices, or 20 percent of the annual U.S. gross domestic product. A majority of these are industrial motor systems.
Moreover, motor system maintenance and management provide significant opportunities for improving energy efficiency and productivity. The U.S. Department of Energy’s United States Industrial Electric Motor System Market Opportunity Assessment (PDF 6.6 MB) states, “In 1994, electric motor-driven systems used in industrial processes consumed 679 billion kilowatt-hours (kWh) – 23 percent of all electricity sold in the United States. Implementation of all well-established motor system energy efficiency measures and practices that meet reasonable investment criteria will yield annual energy savings of 75 to 122 billion kWh, with a value of $3.6 to $5.8 billion” and an equivalent reduction of 74 megatons of greenhouse gas emissions. Furthermore, the E-Source DrivePower Atlas at www.esource.com reports that, “The efficiencies of mechanical equipment, in general, can be increased typically 10 percent to 15 percent by proper maintenance.”
A Reliability-Centered Motor Management Program
To begin developing a reliability-centered motor management (RCMM) program, first identify the equipment that will be included in the program. Figure 2 shows an overview of the program, which begins with a facility asset census. Set up a pilot area for developing the program, and expand the program incrementally to ensure its success.
Figure 2. The Reliability-Centered Motor Management Map
Source: H. Penrose, Electrical Motor Diagnostics: 2nd Edition (2008).
Once a facility asset census is completed, establish a critical equipment list based on the following criteria:
Impact of Equipment Include
Personal safety Any equipment that affects personal safety if it fails
Regulatory Equipment that involves regulatory issues such as the environment
Production Equipment that affects production; the greater the impact, the higher the ranking
Cost Equipment that surpasses a repair or replacement value cost
threshold; average industrial value for consideration is $25,000
Other Working environment, marketing/sales considerations, equipment
deemed important by the organization.
Perform an equipment condition assessment in parallel with a preventive maintenance optimization and development of condition-based maintenance practices. In an equipment condition assessment, critical equipment is evaluated through tests and inspections such as those used in Reliability-Centered Maintenance (RCM). Keep results on record, and repair or replace equipment that is in poor condition; significant energy improvements can be considered at this time.
The preventive maintenance optimization process can be as simple as reviewing existing processes to eliminate redundancies or as complex as advanced commercial preventive maintenance optimization processes. In almost every case, from one-third to two-thirds of existing planned maintenance procedures can be eliminated or combined. Compare the remaining preventive maintenance tasks to the results of a condition-based maintenance review, which determines when to perform corrective maintenance to maximize equipment and component life. This involves processes such as RCM or a maintenance effectiveness review.
A maintenance effectiveness review evaluates the testing that is currently being performed and compares that to the failure rate and modes of the equipment. If failure rate and modes exist and are as high as (or higher than) they were before the application of condition-based maintenance, consider improving the program. The process also provides an opportunity to decrease maintenance and identify new inspections, tests, or processes. Conduct a maintenance effectiveness review periodically; the equipment included in this review is usually selected by an experienced RCM analyst.
Select root-cause analysis procedures and train personnel in their application. Internal or external facilitation can aid teams in using more rigorous processes. In addition, consider applying other process-based best practices, such as the following:
-
Motor Repair vs. Replace Decision-Making
-
Motor Repair Specifications
-
Lubrication
-
Storage
-
System Energy Improvements: These include right-sizing and using variable-frequency drives (VFDs). In addition, use ITP software tools such as MotorMaster+, AirMaster+, Pumping System Assessment Tool (PSAT), and Fan System Assessment Tool (FSAT) to optimize motor-driven systems.
All of the findings and feedback support each of the other parts of the overall RCMM program map.
Key Performance Indicators
When applying an RCMM program, consider the appropriate best practices and a method of measuring the application of the program. Maintenance managers should develop a series of key performance indicators that relate to the program’s components. The details of each component within the key performance indicators depend on the company and its goals. Be sure to consider the following key performance indicators.
Electrical Maintenance: A solid electrical maintenance program must be in place for a program to succeed. At a minimum, consider the following components:
-
Documentation and drawings of critical equipment
-
General electrical maintenance practices
-
Arc flash and personal protective equipment program
-
A review of load and power quality of critical equipment
-
An active electrical root-cause analysis program
-
Electrical safe work practices and corporate safety program
-
An emergency repair plan for critical equipment.
Motor and Driven Equipment Selection Program: Outline a process for the selection and specification of components for the motor system, including right-sizing, selection of controls and VFDs, and optimal selection of driven equipment for the complete motor system.
Commissioning: Inspect and test new and repaired equipment before application or storage. This ensures the reliability of the component and that changes have not been made that may reduce the component’s energy efficiency.
Operations and maintenance: This includes repair vs. replace decision-making, maintenance training, failure analysis, testing technologies, lubrication, and inspections.
Electric motor system repair: Repair processes, procedures, and specifications, including the qualifications of the repair shop for specific equipment types and sizes. The primary purpose is to ensure reliability or energy efficiency.
Plant inventory and records: Motor system components in operation and maintained as spares; includes storage procedures and processes.
Utility management: This is the energy efficiency component of motor management programs. It should include selecting motor systems for evaluation for immediate energy improvement opportunities within the company’s financial constraints. For assistance, use the technical resources for fan, pump, motor, and compressed air systems on DOE's Industrial Technologies Program Web site.
Reliability-Centered Motor Management Team
Select a team to develop the RCMM program and to be involved in the RCM and maintenance effectiveness review processes. Include both in-house and external stakeholders in the motor management program, such as these:
-
R&M managers
-
R&M technicians
-
Utility or energy managers
-
Purchasing
-
Operations managers
-
Information technology specialists
-
Associated vendors
-
Others, as necessary.
It is important for this team to meet regularly, such as once a month, after the program begins. As the program matures, team meetings could be held quarterly.
Case Study: Automotive Transmission Manufacturer
A good example of this kind of program is taking place in Indiana. An Indianapolis-based transmission manufacturer has been implementing a motor management program since 2001, focusing on condition-based inspection, testing, vendor storage, motor repair practices, and root-cause analysis. The RCMM team consists of internal personnel and skilled tradespersons as well as a contracted electric motor repair facility. At the monthly team meetings, the repair facility reports volume and repair cost reductions and makes recommendations for improving the reliability of motors that have been repaired. The internal tradespersons conduct root-cause analyses and “repetitive failure analyses” that include investigations of instances in which equipment fails more than once in a given period.
When initial testing and inspection began, the program’s repair and replacement costs increased as equipment with poor levels of reliability were identified and corrected. Once the dust settled, staff determined that there were 720 average repair-or-replace decisions per year affecting electric motors. Focusing on just three of the seven key performance indicators, they reduced the number of repair-or-replace decisions to slightly more than 120 per year, the majority being minor repairs. The impact on overall equipment availability has been measurable, and the cost per unit manufactured has dropped significantly.
Warranty Recovery Opportunities
Most companies forget to investigate warranty recovery opportunities in failed equipment. The average motor repair vendor warranty is one year; however, many repair shops increase their competitiveness by offering warranties as high as five years. New, premium efficient, electric motors have warranties ranging from five to seven years.
One reason that both new and repair facilities are willing to offer these warranties for motors is that many companies do not track warranty opportunities. In a large number of facilities, the missed opportunities add up not to thousands of dollars but to hundreds of thousands or even millions of dollars in unclaimed warranties. It is a good idea to track warranty dates in computerized maintenance and management system programs or using third-party software to gain quick access to records; this ensures that your company is taking full advantage of warranty opportunities.
Final Considerations
A growing number of utilities and industrial companies are focusing on the number one R&M improvement opportunity: electric motors. These companies find that improving electric motor systems through partnerships, equipment storage, best motor management practices, repair standards, and robust maintenance programs have reduced overall energy use and increased competitiveness and profitability.
In this time of rising energy costs, corporate fiscal issues, and the need to improve competitiveness and capacity, establishing a motor system maintenance management program can be one of the most substantial improvements a company can make. The best time to start is now.
About the author
Howard W. Penrose, Ph.D., is the president of SUCCESS by DESIGN, a reliability and maintenance services consultant and publisher. He has 25 years of experience in the R&M industry, from the shop floor to academia, manufacturing, and the military. Dr. Penrose was an adjunct professor of industrial engineering at the University of Illinois at Chicago and served as a senior research engineer at the UIC Energy Resources Center. He has been active in IEEE as vice chair and chair in various chapters, and is presently on the IEEE DEIS board of directors. He is a DOE MotorMaster+ Certified Professional, a Certified Maintenance and Reliability Professional, both a NAVAIR and NAVSEA RCM specialist, and the founding director of the Institute of Electrical Motor Diagnostics. He is also the author of two books on motor management and reliability and a member of the National Writers Union and the International Federation of Journalists.
Please contact Dr. Penrose with questions about this article.
This article appeared in the Summer 2008 issue of Energy Matters, a publication of the U.S. Department of Energy.
Read More Energy Matters Articles on These Topics
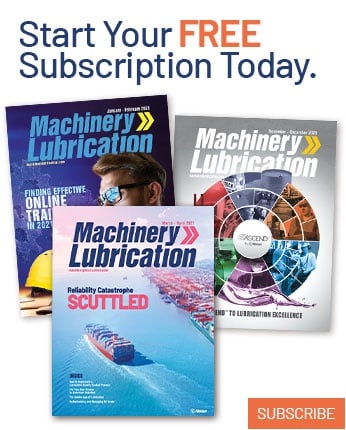