Twelve to 48 months ago, you started a reliability and maintenance improvement initiative, and now the cost crunch is on. We've seen heavy downturns in the housing and banking industries, and the crunch is now at your doorstep. Your company has decided to cut cost because sales are down and/or the price of your product is down. In this situation, you'll find out if your plant and company are serious or not about improving reliability.
Companies tend to cut cost short term, which, in many cases, increases the cost significantly over a two- to six-year period. This depends on how cost is cut. But typically (depending on current equipment condition), it takes 18 to 24 months for the short-term, erroneous cost cutting to show up as increased cost in the balance sheet, while equipment reliability usually takes nine to 21 months to show in production numbers.
If you are unlucky, costs are even higher two to six years from now and the same type of cost cutting takes place again with new management (the old managers may have been promoted because they did such a good job cutting cost for 12 months).
Which cost is cut?: When we decide to cut cost in a plant or company, panic spreads. Typically, the cuts hit, in order: 1) Any type of travel; 2) Training; 3) Unavoidable maintenance jobs (they get postponed); 4) External resources (usually hired to help improve and cut cost long term); 5) Overtime; 6) Hands-on external resources; and, 7 to etc.) Anything visible (books, filtered water, free hats, lunches, etc.).
An interesting note is that an extension of six hours to a shutdown due to poor planning may cost a plant $100,000, but it's seldom questioned. Meanwhile, book purchases are fiercely shut down. The difference? Books are a visible cost while the shutdown extension is a hidden cost.
To cut or not to cut?: Should we not cut cost? No, you should. My point is that focusing on cost itself rather than focusing on what drives cost will give you the wrong results such as short-term cost savings with a long-term cost increase.
Example 1 - Let's assume your size of plant should have 95 hourly maintenance people. Always be careful where these numbers come from, but let's assume the number is correct or at least believed to be correct. You have 110 people. It may seem logical to immediately reduce the hourly workforce. But, it's often the wrong thing to do. If you cut 15 people from your crew without changing the way you work BEFORE you do the cut, less preventive maintenance (PM) and corrective maintenance (CM) work will be completed. With less PM and CM, reliability will falter. The exception would be if your backlog is zero and/or the people you are about to lay off normally don't produce.
A commonly used misconception is that if we lay off people, the remaining employees will pick up the slack. The contrary is most commonly true due to worsening plant morale and a lack of incentive to pick up more work or do work better.
Instead, focus on the things that drive cost down in order to reduce the total workforce and other costs long term. Improved reliability will reduce the need for spare parts and CM work. With increased reliability, you can look at reducing the workforce by attrition.
Example 2 - The other desperate cost-cutting measure is to defer maintenance. What works against this logic is that a valid maintenance job can't be avoided; it can only be delayed. Unfortunately, a delayed maintenance job will 99 times out of 100 be more expensive if it is executed later rather than sooner.
Plant management never talks about deferring maintenance. That would be political suicide as soon as we have downtime. Instead, the talk centers around reducing overtime, contractors and people - as if we currently spend money on those items today as a luxury.
What do we do?: Cut cost the right way. Stick with your initiatives (assuming they are good). Increased reliability will drive down cost. You may have to slow down outside support and training, but don't stop it completely. Stopping an initiative completely will send the wrong message to the organization. If you stop it, your initiative will be seen as another management fad that failed.
Call your reliability process lean, Six Sigma, TPM, asset management, TQM or something else; you'll find that it comes back to the same things we discussed in the 1970s and earlier. Improved reliability and reduced costs come through the interplay of these words/actions: prevent, inspect, prioritize, plan, schedule, execute well, record, analyze and improve.
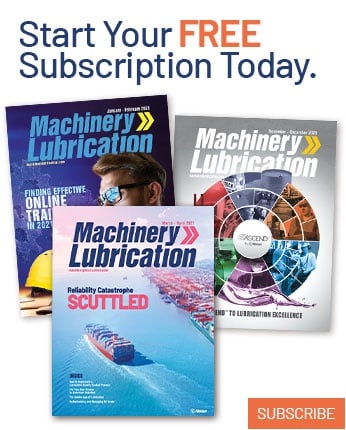