Many people have an incomplete understanding of the power of a lubricant analysis program for mechanical systems. Some refer to it as the oil analysis program, but this removes a portion of the focus from the greases employed. These people tend to think of the lubricant analysis program as merely a way to determine if the oil needs changing or if the drain intervals can be safely extended. This is an inadequate comprehension of the power of lubricant analysis. Even more confusing is the decision matrix by which a particular machine is earmarked for inclusion in the analysis program. Most of the time, little to no thought is given to the assets included in the program. It's usually the combination of "we've always tested it" and "it's big, so it gets tested". Rarely can someone display the methods used to determine if lube analysis should be performed on the machine.
These attitudes are fairly pervasive and, as a result, asset health, reliability and profits suffer. This article will examine some of these issues.
Let's take a moment and discuss the purpose of lubricant analysis and how machines should be chosen for inclusion in an engineered lube analysis program. The purpose of such analysis, as with any inspection technique, is to collect data pertaining to the health of the system by detecting the presence of a failure mode or a condition that may lead to a failure mode. We are talking about lubrication, why bring in terms like failure modes? Remember, a lubricant has a specific function, it experiences functional failures and, as such, has failure modes with symptoms. The lubricant also can affect (and be affected by) other system components. Given this, the lubricant must be analyzed as a component of the system, just like the bearings and gears the lubricant services. The lubricant must be analyzed within the context of the system it services, as systemic changes can be detected as changes in the lubricant itself.
A comprehensive lube analysis program can alert you to three different sources of changes that occur in a lubricant system.
One is a change in the lubricant's chemical condition. Viscosity changes, oxidation and additive depletion are common indicators of chemical changes.
A change in the condition of the physical parts that the lubricant services produces wear particles. These particles can be seen in a representative sample of the lubricant. You can detect wear mechanisms such as abrasion, adhesion and corrosion, indicating severe defects in the gears, bearings and/or seals of a system.
You can also detect the ingression of outside solids, liquids or gases (known as contamination) in the sample. The presence of contaminants is typically a function of two things: poor storage and handling techniques on the part of people servicing the reservoirs and compromised shaft/housing seals, usually as a result of improper installation.
Chemistry, wear and contamination are the big three when it comes to lubricant analysis of mechanical systems. Staying on top of these will result in much useful information about asset health. Dropping even one of them will result in an incomplete picture of the system's condition. Now, let's discuss how we select the assets that receive lubricant analysis. It seems there are as many methods for deciding this as there are assets. Some people only do lube testing on "the big stuff". Some only perform analysis on the reservoirs with more than "X" gallons in them. Sometimes, they choose only the reservoirs with special lubricants.
None of these plans take into account the factor that should play the deciding role in an asset's inclusion in an inspection program … criticality. The point of a comprehensive maintenance strategy is to mitigate as much risk as economically feasible from the operation, thus increasing the conditional probability of reliable operations. Two key components of that strategy are a thorough evaluation of the relative importance of each asset/machine in the operational chain and the failure rate(s) of those machines. The combination of these factors is referred to as asset criticality. Criticality is the equalizer that sorts the essential from the non-essential. It should reflect more than just the opinion of operations. You must also consider purchasing, engineering, environmental, safety and health effects. Not taking these into consideration will result in the wrong machines getting included in the program and the important ones being left out.
Understanding the real purpose of lubricant analysis and how to quantitatively analyze asset criticality for program design may change your outlook on how the analysis program is designed and administered at your facility. Remember, maintenance strategies are engineered through an analysis of the likely failure modes and measured failure rates, not discovered through trial and error.
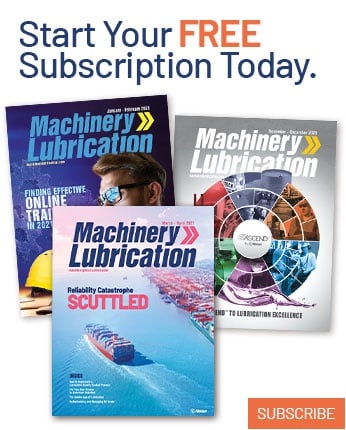