An innovative, alternative warehouse-design concept developed by a
“To our knowledge, this is the first implementation of non-traditional diagonal aisles anywhere,” Meller said. “We are very excited.”
In 2006, Meller and Gue announced two novel designs – the optimal cross aisle design and the fishbone aisles design – as alternatives to conventional warehouse layout in which storage racks are laid out to create rows of parallel picking aisles with one or more cross aisles in the middle. The researchers’ alternative designs included V-shaped diagonal cross aisles that improved order-picking travel times by 10 to 20 percent.
The layout at Generac is almost a direct implementation of one of those designs. Brian Randleman, logistics manager at Generac, led the project.
“We had a clean-slate opportunity for our warehouse in Whitewater, and I had just learned of their work in Modern Materials Handling magazine,” Randleman said. “I contacted our director of operations, and he was positive on the idea. His team ran some numbers to prove the benefit, and three months later we had drawings in our hands.”
“For most managers in the logistics industry, implementing this kind of design is a little scary,” Gue said. “Everyone wants someone else to be the first adopter.”
The warehouse in Whitewater stores finished electrical generators and transfer switches before they are shipped to customers all over the country. Randleman said the decision to implement diagonal aisles was part of a broader strategy to make some bold changes in logistics at Generac.
“For what we do, the layout really works well,” Randleman said. “We have racking in the middle section, between the diagonal aisles, and floor storage below the diagonals. That gives us the flexibility to adjust to changing operating conditions in the future.”
Workers have responded positively to the new design, Meller said. When they first proposed the designs, there were numerous objections from practitioners. Some of these objections involved “the way we’ve always done it” mentality, but others were related to safety, an obviously important consideration. Meller said Generac installed safety mirrors at key intersection points to help workers navigate the layout safely.
In addition to improved material flow and reduced travel distances, Generac has realized some unexpected benefits. For example, workers no longer turn 90 degrees to enter the picking aisles. The 45-degree turns can be done at greater speed without comprising safety.
Gue and Meller said that announcements of other implementations and new research results are forthcoming.
“The implementation at Generac is a real boon for us,” Gue said. “Now we can point to them and say, ‘See, this really can be done.’”
Headquartered in
Meller is the James M. and Marie G. Hefley Professor of Logistics and Entrepreneurship and also director of the University of Arkansas Center of Engineering Logistics and Distribution.
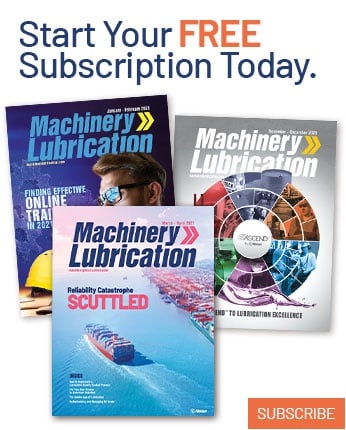