One of the keys for success for kaizen events is planning. All the tasks of setting the proper scope, selecting a good mix of team members, lining up support resources, getting the planned materials and tools, collecting all the relevant documents (standard work combination sheets, layouts, etc.) from the target area, organizing all the training materials, etc., can help determine the success or failure of any kaizen event.
But sometimes, such plans crumble when they hit the light of the real world. As stated best by General Binford Peay, U.S. Army Gulf War leader, “Planning is priceless. The plan itself is useless.”
Last week at the Batesville Casket Company, we completed an outstanding kaizen event in our Chihuahua, Mexico, plant despite the fact that our kaizen event was not even close to our original plan.
Let’s back up a bit. Last month, I traveled to our Chihuahua plant to accomplish a couple of items including setting the scope for a kaizen event with our plant leaders. We reviewed the target area, assessed the scope, calculated the expected results (target goals) and lined up resources, plus all the other planning tasks needed for a successful kaizen event. Everything was all set and ready to go, that is until the week before the event.
At the request of the plant manager, our target area was changed to a completely different part of the business to better support our strategic plans. Both events were seeking productivity gains and shop-floor space reduction; however, that is where the similarities ended.
On top of that, the goals for the new target area were more aggressive (instead of looking at just one line, we increased the scope to three different lines), but all we needed to do was provide a blueprint for the recommended changes.
So, what do you do to be successful? Cancel the planned event or go forward as originally planned? Put the new target area on deck for the next scheduled kaizen event in order to completely plan it out? Switch gears and go full speed ahead with the new event without the benefit (luxury) of time to plan it all out?
We chose to adapt to our changing environment, switch gears and focus on the new target. Instead of canceling our previously planned event for the week, we just postponed it a month. With some fast planning, we altered the make-up of the team, quickly lined up some resources and boldly moved forward.
Last week during the kaizen event, we continued the same motto of “plan, then adapt”. Instead of just providing the blueprint (layout and line balance), we experimented with some layout changes that did not required air or electric modifications on the first night.
Based on this success, we convinced our guidance team to allow us to go forward with the real move. By mid-week, we moved two lines overnight and started them up on time and running to takt time the next day. The third line required additional experimentation that postponed the actual move until Friday.
The end result for all the team’s hard work and flexibility was a 40 percent reduction in floor space and a 30 percent productivity improvement.
Kaizen planning is important; however, our dynamic work environments demand that we are more flexible. The leadership skills required to be successful are the ability to plan quickly and being able to adapt once our plans come in contact with the real world.
About the author:
Mike Wroblewski started his lean journey with instruction in quick die change from Shigeo Shingo. Mike is currently the lean sensei at Batesville Casket Company in Batesville, Ind. He also writes a blog called “Got Boondoggle?” featuring lean and Six Sigma topics. Check it out at http://gotboondoggle.blogspot.com/.
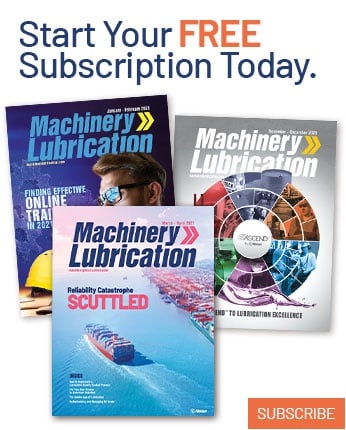