In the Reliability Forum department of Reliable Plant, suppliers provide their insights to a question posed by editor Paul V. Arnold. This issue, the question went out to bearing manufacturers:
“If you could give one piece of advice that would increase our readers’ bearing life and/or performance, what would it be, and why?”
TimkenThis reply comes from Ravi Bhatia, the vice president of engineering for the Timken Company’s Industrial Group.
“Focus on the basics! Industry’s relentless pursuit for uptime may well have an adverse impact on the service life of anti-friction bearings. But by adopting preventive maintenance practices, assuring proper lubrication, and understanding and implementing sound bearing fitting and setting techniques, you can greatly increase their useful life.
“First, lubrication is key. Choose a lubrication system and quality lubricant. Essential to the function of all rotating or reciprocating parts, especially bearings and gears, lubricant film separates contact bearing surfaces under stress and provides essential protection from corrosion and wear. In the case of an oil splash or circulating oil system, the added benefit is heat transfer.
“Too often, plants experience unnecessary downtime and aggravation because of improper lubrication. An inadequate lube supply gives rise to additional friction and heat generation, leading to excessive wear and/or premature bearing fatigue damage. Excess lubrication, particularly at high operating speeds, may generate more heat from churning, which causes the lubricant to deteriorate chemically. This also leads to bearing damage.
“With proper application and a regular maintenance schedule, you can avoid bearing damage from lubrication problems. To ensure proper lubrication:
- Follow set guidelines created by the equipment builder for each application.
- When applying grease, force it between the bearing rolling elements and cage (or retainer) to assure an adequate fill and that the critical raceway surfaces are properly lubricated.
- Pay attention to when a bearing needs relubrication.
- Watch equipment gauges for early indications of a problem, such as fluctuating and/or unusually high temperatures.
- Listen for noise or unusual vibration.
- Watch for lubrication leaks.
- Consider regular lubricant sampling and look for evidence of contamination.
“Second, proper adjustment is critical to superior bearing performance. Fitting or setting up a bearing with excessive or insufficient internal clearance or, in certain instances, too high a preload can lead to premature damage and shortened bearing life. Besides downtime and costly repairs, poor bearing fitting and setting may affect more than the bearing. It also affects the operation and service life of additional components.
“Following the manufacturer’s guidelines for fitting, setting and regular maintenance are the best forms of problem prevention. If short on time, correct a pair of tapered roller bearings set with excessive looseness by advancing the adjusting device or removing shims. On the other hand, a bearing adjusted too tight may cause heat-related damage and need replacement. Good bearing fitting and setting procedures must be accurate, repeatable and verifiable after assembly. They also must take into account other component parameters to optimize system performance.
“Proper lubrication and maintenance and handling practices are critical. Failure to follow installation and maintenance instructions can lead to equipment failure and create a major safety risk.”
For more information, visit www.timken.com.
SKFThis reply comes from Daniel R. Snyder, the director of applications engineering for SKF USA Inc.
“Major bearing manufacturers spend significant time and resources developing bearing designs, manufacturing processes and prediction tools to meet customer requirements both for original equipment manufacturers and end-users.
“In spite of this, bearings still fail. Experience has shown these failures are attributable to the equipment being used differently than originally anticipated by the OEM or improper installation of the equipment. Thus, the best way to maximize bearing service life is to understand the operating conditions to which the equipment was originally designed, use a high-quality bearing supplier, and make full use of available condition monitoring equipment and mounting tools to minimize mounting problems.
“Additionally, a good predictive maintenance program that includes root cause analysis goes a long way to increase uptime for even troublesome applications.”
For more information, visit www.skf.com.
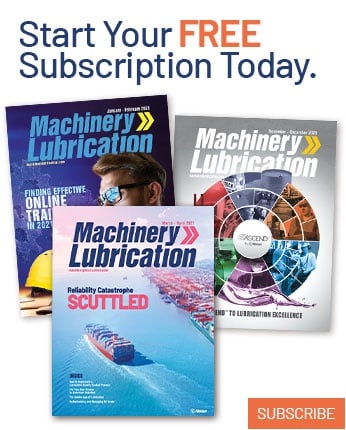