Lear Corporation, a leading global supplier of automotive seating systems, electrical distribution systems and electronic products, announced this month that lean manufacturing processes have resulted in major productivity improvements and cost savings.
Speaking at the Automotive Manufacturing Solutions (AMS) global conference October 3 in Dearborn, Mich., Tony Coomer, the company’s vice president of Advanced Manufacturing and Continuous Improvement – Seating Systems, said lean manufacturing techniques have been deployed throughout the company’s global manufacturing network.
“Lear’s commitment to ‘Total Lean Behavior’ produces high-quality products more efficiently,” Coomer said, adding that the Lear Manufacturing System (LMS) relies on employee involvement and a commitment to efficient product design. That is imperative since Lear employs 90,000 people at its 236 locations in 33 countries.
Implementation involves a focus on improving:
- work environment (housekeeping)
- overall quality
- plant layouts
- material flow
Lear employees are trained on LMS during a three-week workshop. The training is conducted at all Lear plants by a lean manufacturing leader, and employees receive LMS certification upon successful understanding of LMS principles and validation of model line projects which deploy LMS.
“Our training program is designed to develop synergy between plants, empower people to make changes, and create value for customers and shareholders,” Coomer explained. “It has enabled us to establish a common and consistent lean manufacturing strategy throughout the company.”
Product design is another key element in Lear’s Lean Manufacturing System. Product design teams rely on LMS principles to ensure products can be manufactured in a lean environment. Approximately two-thirds of product costs are locked into the initial design of the product, Coomer noted, so any effort to reduce cost after the initial design stage can only influence the remaining one-third of the product’s overall cost.
At one facility, for example, product design teams incorporating design for lean principles in a model year change realigned workstations, changed production flows and made other assembly line changes to boost productivity.
Additionally, improvements in the workplace environment (or “World Class Housekeeping” practices) have a major impact on productivity, quality, delivery, cost and employee morale. All sustainable improvement flows from this discipline and continuously reveals waste in the company’s manufacturing systems. This element is a lean cornerstone and must be maintained daily in order to maximize manufacturing systems as well as creating a safe work environment.
Coomer said that Lear’s focus on “quality at the source” ensures that problems are dealt with at workstations within each plant, preventing them from reaching Lear’s customers. Process changes have reduced cycle time at workstations and improved quality throughout Lear’s manufacturing environment, triggering, in some cases, significant decreases in defects.
Plant layout also plays an important role in Lear’s approach to lean manufacturing. Lear uses value stream mapping (VSM) to understand work flow and identify waste. In addition, extended VSM allows Lear to eliminate waste from the entire value stream – from supplier to customer. VSM encompasses items such as freight costs, inventory controls and production changes.
Attention to packaging, material flow and storage systems is another important cornerstone of Lear’s Lean Manufacturing System. By reducing unnecessary corrugated pads used to ship certain back panels, Lear reduced shipping costs for the panels by more than 30 percent. By switching from “expendable” to reusable containers for some metal parts, the company realized a first-year package cost reduction of nearly 40 percent and a program package-cost reduction of even more at one factory.
“Lean manufacturing creates value for the customer with a minimum amount of waste and a maximum degree of quality,” Coomer said. “The Lear Manufacturing System benefits our customers, our suppliers and the company itself.”
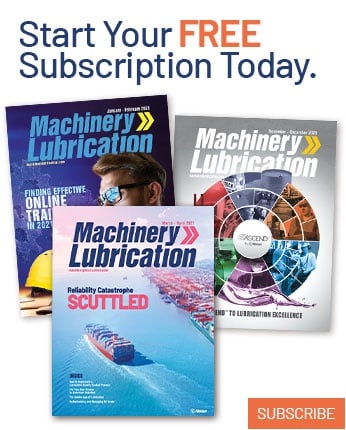