A good example of effective federal and state collaborations can be found in a new program in which U.S. Department of Energy (DOE) Qualified Specialists work with Purdue University's Technical Assistance Program (TAP) Energy-Efficiency Services and Indiana's Workforce Innovation in Regional Economic Development (WIRED) initiative to increase industrial energy efficiency. The new worker training and certification program will benefit up to 28 manufacturers in North-Central Indiana in the very first round of activities.
TAP Energy Efficiency Services is introducing the Energy Efficiency Practitioner Certification Program in the 14-county WIRED region through a competitive solicitation for applications from regional manufacturers. Each manufacturer selected can send up to five employees through the program free of charge, thanks to funding from WIRED.
The new training and certification program should be especially useful to facility engineers, plant managers, end users, purchasing agents, decision makers, and other professionals who use or purchase energy in their respective plants. Purdue TAP also hopes to make the program available statewide later in the year on a fee-for-service basis.
Certifying in-plant practitioners of energy efficiency
The program is designed to make manufacturers more knowledgeable about energy-efficient industrial processes, provide technical assistance, and build skills among manufacturing employees. It should also help to create a new network of energy-conscious firms in the region that are increasing their productivity and profits through more efficient use of energy.
On-site training will be provided by instructors from TAP Energy Efficiency Services and TAP's Manufacturing Extension Program (MEP) Center, which is an affiliate of the U.S. Department of Commerce's National Institute for Standards and Technology (NIST) MEP. Off-site workshops on evaluating industrial process systems for improvement opportunities will be conducted by numerous Qualified Specialists in the DOE Industrial Technologies Program (ITP).
All the training modules have been developed by DOE, industry trade groups, manufacturers, engineering firms, or Purdue faculty and staff. Many of these modules will provide trainees with continuing education units they can use in obtaining or maintaining their professional accreditation.
As part of a seven-and-one-half-day certification course that takes a system-wide approach to energy efficiency, trainees will select three or more off-site, one-day BestPractices workshops on optimizing various industrial systems. These include fans, compressed air systems, motors, pumps, process heating systems, steam systems, and more. During the first day of their on-site training, participants will also make use of DOE's Quick Plant Energy Profiler (Quick PEP) software to get a feel for the best opportunities for savings in their plants.
The 28 companies will be selected from among all applicants by TAP and WIRED reviewers. Three energy-intensive industry groups in the north-central WIRED region are the focus of the first solicitation: transportation-related manufacturers, including automakers and related suppliers; primary metal manufacturers; and fabricated metal products manufacturers. Firms in other industries could also apply.
Required for certification: An energy-saving project
To be certified, trainees must identify and implement an on-site energy efficiency project. A Qualified Specialist will spend about half a day at each plant that sent a team of trainees through the course. The Qualified Specialist will help trainees identify potential projects, rank them in terms of priorities, and develop an implementation strategy for at least one project.
At the end of the training period, each company represented in the program will have 12 months to implement an actual energy efficiency project. It will also have a specified amount of time to monitor, measure, and verify the energy savings resulting from the project and convey the results to TAP and WIRED.
This requirement virtually guarantees both reductions in energy use and increases in profitability in the region. Estimates indicate that this manufacturing-intensive part of the state could be spending more than $100 million on natural gas and $150 million on electricity each year. The first 140 employees or so who take the course are likely to not only save energy and dollars in their own plants but also help spread the word to other firms they deal with in the course of their business operations, thus propagating the benefits of the program.
For more information, contact Ethan Rogers, Manager of Energy Efficiency Services, Purdue Technical Assistance Program, earogers@purdue.edu. And for more information about a joint project between DOE Industrial Assessment Centers and the MEP, see a related story in the Spring 2007 issue of Energy Matters.
Read more Energy Matters articles on these topics:
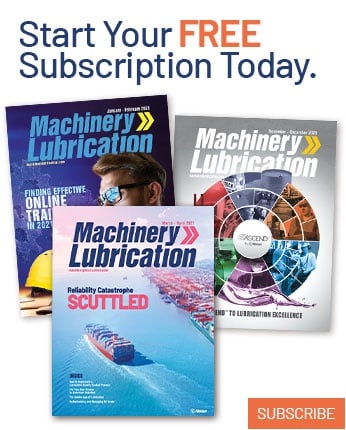