Worthington Industries Inc. on August 27 announced the first-year results of its safety management program, Safe Works, which include a 44 percent reduction in serious injuries (OSHA Days Away, Restricted or Transferred), 22 percent reduction in total injuries (OSHA recordable) and 31 percent reduction in number of workers’ compensation claims, which resulted in $1.2 million in workers’ compensation cost savings. All results are compared to the prior fiscal year.
“We believe that our company-wide goal of zero injuries is not just a goal to work toward, but is attainable,” said John P. McConnell, Worthington Industries chairman and chief executive officer. “A safe workplace and workforce speaks to the heart of our philosophy – that employees are our most important asset. Fewer injuries also positively contribute to the company’s bottom line through lower workers’ compensation costs and increased productivity and quality as a result of fewer disruptions to production.”
Zero DART injuries was achieved at 21 percent of the company’s manufacturing facilities during the year, which ended May 31. Eight facilities exceeded the milestone of one year with zero DART and zero recordable injuries. On average, Worthington Industries’ DART rates are more than 64 percent lower than industry average and recordable injury rates are more than 52 percent below the industry average.
Since 2001, WI has revitalized safety practices to strengthen the company’s safety culture and reduce injuries. During the past six years, these efforts have lead to significant results, including a 54 percent reduction in OSHA recordable injuries and a 57 percent decrease in OSHA DART (Days Away, Restricted, Transferred) injuries. A 63 percent reduction in number of workers’ compensation claims during this time period also resulted in several million dollars in workers’ compensation cost savings.
The company’s Safe Works safety management program is a centrally governed, locally managed initiative that involves each employee in the safety process. “Most people believe safety is a top-down initiative, but we don’t feel that way. Everybody benefits from a safe workplace and an ongoing safety improvement process and everybody should have a voice in how it works,” said George Stoe, Worthington Industries executive vice president and chief operating officer.
The Safe Works initiative provides standardization and sharing of company-wide best practices, while allowing facilities to address localized needs and concerns. Voluntary employee safety councils lead their own facility’s safety process, including managing the company’s voluntary behavior-based reinforcement program, Business Risk Improvement Techniques for Everyone (BRITE), which focuses on developing safe behaviors and preventing injuries through positive reinforcement. Employees are also directly involved in the safety improvement process through personal protective equipment (PPE) trial programs, creating their own safety training videos and continuous improvement efforts.
“We are pleased with the first-year results of Safe Works. With the continued dedication of our employees and facility leaders, we expect to continue building a sustainable safety culture in our company,” said McConnell.
About
Worthington Industries is a leading diversified metal processing company with annual sales of approximately $3 billion. The Columbus, Ohio-based company is
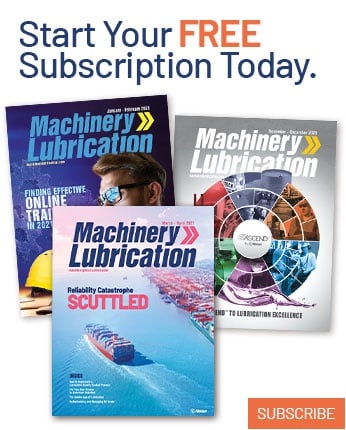