After visiting and working at numerous manufacturing plants across the United States this past year, I have come to the conclusion that we really don’t know how to use an andon light properly, much less know why we should use them. In most cases, the lights are pointed out as one of the indicators that the plant does know about lean and practices lean principles. In these same plants, I see other things.
I have seen andon lights turned on and stay green all shift long regardless of multiple problems occurring. (Could it be possible the management yelled about the line stops and flashing lights so much that everybody is now afraid to pull the cord?)
I have seen andon lights turn on but all the bulbs were burned out, rendering the light useless. (Maybe we should also work on our 5-S audit program, lack of gemba walks and poor Total Productive Maintenance program?).
I have seen andon lights flash and blink for hours but not one person comes running. (Why does the signal for help go unanswered and why don’t we look into the causes for the long delays?)
I have seen huge multi-stacked andon lights that nobody seems to remember why each color was needed. (How can we make the andon light system simpler?)
I have even seen andon lights used in shop floor pranks just to watch people frantically run around for the humor of the guilty light switch pullers. (Maybe we should read the story about the boy that cried wolf at our next shift meeting?)
Here is a simple visual signal that could improve awareness and responsiveness on the shop floor yet we don’t take the time to properly train and use this tool for its intended function. Just having andon lights is not an indication of being lean; it only helps make problems visible along with promoting the goal of FAST response.
I guess we have taken to heart what my old junior high football coach would regularly say to us on game day, “Boys, keep your jerseys tucked in and your socks pulled up. If you can’t play well, at least you are going to look like you can play well.”
About the author:
Mike Wroblewski started his lean journey with instruction in quick die change from Shigeo Shingo. Mike is president of Victory Alliance Technologies, a Greensburg, Ind., firm that specializes in lean implementation. He writes a blog called " Got Boondoggle?" featuring lean and Six Sigma topics. Mike can be reached by e-mail at mwroblewski@victory-alliance.com.
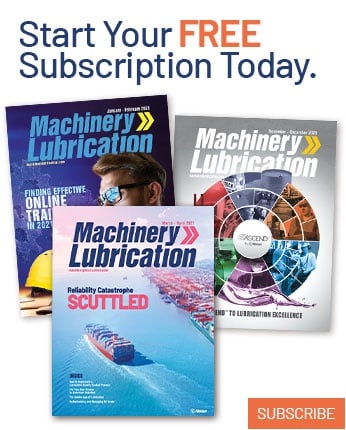