Manufacturers, chemical companies, restaurants, health care providers and others often ask whether the United States Occupational Safety and Health Administration (OSHA) approves certain gloves and other personal protective equipment (PPE) for specific applications. For example, is a certain glove OSHA-approved for exposure to bloodborne pathogens or handling different types of industrial chemicals? And if not, who is responsible for selecting gloves and other PPE that keep employees safe?
OSHA Guidelines
To answer these questions, OSHA does not certify any products. According to current OSHA regulations, the employer has the final responsibility for selecting gloves and other personal protective equipment.
OSHA, however, does issue guidelines to help employers establish a safe and healthy work environment for their employees. In the case of possible worker exposure to bloodborne pathogens, OSHA simply recommends the use of "appropriate gloves" without specifically requiring the gloves to be U.S. Food and Drug Administration (FDA) approved surgical or medical exam gloves.
Either of these types of gloves would certainly provide suitable protection. However, gloves should be selected for the specific application. If employees, for example, are cleaning animal cages in a lab, a heavier liquid-proof or chemical-resistant glove may be more appropriate.
Achieving appropriate protection against chemicals is even more complicated because of the great diversity of compounds and applications. OSHA inspectors will generally accept the employer's judgment in regard to personal protective equipment. In applications where the work is especially dangerous, the inspector might request documentation that the PPE is appropriate for the situation.
Most glove manufacturers and distributors, as well as many PPE suppliers, can make recommendations for the appropriate glove for a specific application. However, these recommendations are inevitably based on extrapolations resulting from standard laboratory test methods. Such test procedures may not adequately replicate the conditions in which the gloves are being used.
For this reason and because glove and PPE manufacturers do not have enough knowledge of or control over the conditions during end use, all recommendations are advisory only, with the manufacturers declining any liability. As stated above, current OSHA regulations indicate the employer has the final responsibility for selecting gloves and other PPE.
Glove Classifications
Users sometimes ask if a classification system exists for all types of gloves included in OSHA 29 CFR Part 1910, Item 1910.1389 Hand Protection. The answer is that OSHA has never tried to develop one classification system for all types of gloves in 1910.1389 Hand Protection or any other document since gloves can be classified in too many ways.
Several groups of glove types are listed below. You will notice how these categories overlap, which makes any classification scheme even more complicated.
Material
Nitrile
Neoprene
PVA
PVC
Natural latex
Butyl
Viton
Laminate
Urethane
Cotton
Nylon
Aramid (Kevlar)
UHMWPE (Spectra)
Leather
Service Life
Disposable (single use)
Light Duty
Heavy Duty
End Use
Industrial
Medical market
Critical environment (clean room)
Food handling
Household
Military
Emergency response
Protective Properties
Chemical resistant
Cut resistant
Abrasion resistant
Puncture resistant
Heat resistant
Cold resistant
Glove Re-use
Questions also arise regarding OSHA criteria for reusing gloves. At this point, no specific criteria exist for reuse since no universal answer is possible. For example, a glove that has a small cut in the protective film may be appropriate for use in some applications but not in others.
If the glove is being used to protect the worker from sharp objects, it could possibly be used again, assuming that a second sharp object is unlikely to hit the glove in the same place as the first cut. If the glove, however, is being employed to protect against liquid chemicals, then one small cut is too much and the gloves should be replaced.
In the case of potential hand contact with blood and other potentially infectious materials, OSHA guidelines are more precise:
- Disposable (single-use) gloves such as surgical or examination gloves shall be replaced as soon as practical when contaminated or as soon as feasible if they are torn, punctured or when their ability to function as a barrier is compromised.
- Disposable (single-use) gloves shall not be washed or decontaminated for reuse.
- Utility gloves may be decontaminated for reuse if the integrity of the glove is not compromised. However, they must be discarded if they are cracked, peeling, torn, punctured or exhibit other signs of deterioration, or when their ability to function as a barrier is compromised.
- If an employer in a volunteer blood donation center judges that routine gloving for all phlebotomies is not necessary, then the employer shall:
- Periodically re-evaluate this policy;
- Make gloves available to all employees who wish to use them for phlebotomy;
- Not discourage the use of gloves for phlebotomy;
- Require that gloves be used for phlebotomy when the employee has cuts, scratches or other breaks in his or her skin, or when the employee judges that hand contamination with blood may occur.
Glove Disposal
Glove disposal is often an issue and will depend upon how the gloves are used. If the gloves, for example, are contaminated with a toxic compound or biomaterial that is covered by any disposal regulations, the gloves must be handled in the same way as the toxic material itself.
If the gloves are not contaminated or have been properly decontaminated, either landfill or incineration is a satisfactory means of disposal of either supported or unsupported gloves. Since ordinary aerobic or anaerobic decomposition processes in gloves will not form any toxic products, gloves may be disposed of in any ordinary landfill. Glove breakdown in the landfill, however, will be very slow except for products made of cotton and natural rubber, which are more easily degraded by microbial attack.
A well-designed, properly operated incinerator will likely completely burn all types of gloves as well as any intermediate decomposition products formed during the process. The higher the temperature and the longer the exposure time, the more complete the combustion.
Any facility that must deal with very large quantities of gloves should consult the glove manufacturer for specific recommendations.
About the author:
Arleigh Hartkopf is the customer technical service manager for Ansell Healthcare. Headquartered in Red Bank, N.J., Ansell Healthcare is the leading provider of hand and clothing apparel, along with productivity solutions that enable companies to achieve and surpass their cost and productivity objectives. Working directly with plant personnel, Ansell uses its experience, knowledge and proven products to develop programs that guarantee results in the areas of safety and efficiency. For more information, visit www.ansellpro.com.
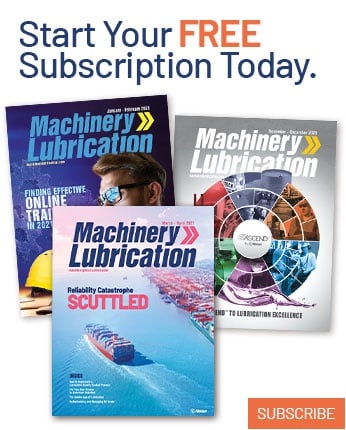