The energy and process efficiency of high-temperature industrial furnaces like those used in U.S. foundries can be improved by using oxy-fuel combustion.
Using oxy-fuel firing technology in high-temperature combustion has considerable energy, cost-saving and environmental benefits. This technology can reduce the amount of fuel needed in furnaces by up to 50 percent, in many cases. And, oxy-fuel firing can trim nitrogen oxide (NO x) emissions by as much as 90 percent in certain applications, as noted in a recent briefing by the U.S. Department of Energy (DOE) Industrial Technologies Program for a PPG Industries glass manufacturing plant that participated in a DOE Energy Savings Assessment.
The oxygen content of standard atmospheric air is about 21 percent (by volume); oxygen enrichment increases this percentage and results in more efficient combustion. Oxygen-enhanced combustion technology actually appeared on the scene several decades ago, but it was not widely used at the time because of technical and cost issues.
Today, however, as a result of technological improvements (PDF 1.83 MB) in several areas, oxygen-enriched combustion and oxy-fuel firing are again being viewed as sound ways to increase productivity while reducing energy use and environmental emissions. Download Adobe Reader.
New Life for Oxygen-Enhanced Technology
This technology can be applied in electric arc furnaces, like those used in the steel industry, as well as in blast furnaces to enhance coal combustion. Studies have shown that the technology can also be successfully employed in the aluminum, chemical, copper, glass, pulp and paper, petroleum, and power-generation industries.
Most industrial furnaces that employ oxygen or oxygen-enriched air (PDF 250 KB) use either liquid oxygen to increase the oxygen concentration in the combustion air or vacuum pressure swing adsorption units to remove some of the nitrogen and increase the oxygen content. Download Adobe Reader. Some systems use nearly 100 percent oxygen in the main combustion header; others blend in oxygen to increase the oxygen content of the incoming combustion air. Still other systems use auxiliary oxy-fuel burners in conjunction with standard burners, and some employ staged combustion and vary the oxygen concentrations during different stages of combustion. Other systems "lance" oxygen by strategically injecting it beside, beneath or through the air-fuel flame.
These are just some of the overall benefits of oxy-fuel firing:
- Increased efficiency . Flue gas heat losses are reduced because the flue gas mass decreases as it leaves the furnace. There is little or no nitrogen to carry heat from the furnace.
- Lower emissions . Certain burners and oxy-fuel-fired systems can achieve lower levels of NO x, carbon monoxide, hydrocarbons, and particulates.
- Improved temperature stability and heat transfer . Increasing the oxygen content allows combustion to be more stable and permits the higher combustion temperatures that result in better heat transfer.
- Increased productivity . Converting a conventional furnace can increase throughput for the same fuel input because of increases in the flame temperature and heat transfer to the load and reductions in the flue gas.
Learn more about the potential energy- and cost-saving benefits of oxygen-enhanced combustion technologies in these ITP resources:
- Oxygen-Enriched Combustion Performance Study (PDF 6.2 MB) Download Adobe Reader.
- Development/Demonstration of an Advanced Oxy-Fuel-Fired Front-End System (PDF 1.07 MB)
- Improving Process Heating Performance: A Sourcebook for Industry (PDF 1.2 MB)
And for more information, contact the EERE Information Center, 877-337-3463.
This article was reprinted f rom the Spring 2007 issue of Energy Matters .
Read More Energy Matters Articles on These Topics
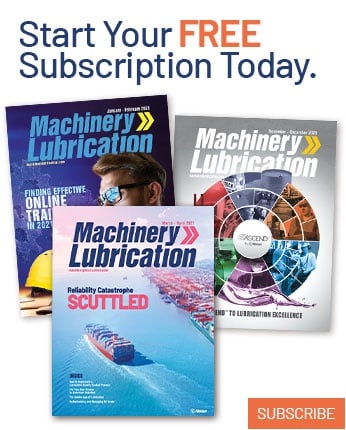