When corporations and/or individual plant sites considered potential areas for reducing costs in the past, they often focused on price concessions from their respective suppliers. While converting to less expensive alternatives usually provided an immediate cost benefit, the changes implemented sometimes had a negative, long-term impact on the manufacturer's cost of doing business.
This scenario tended to have a domino effect as companies pressured their suppliers to reduce prices on products that already had tight profit margins. Suppliers responded by providing less expensive items that often did not have the performance characteristics required for the tasks.
These less expensive — and sometimes inferior — products had the potential to result in increased injuries, misapplication, non-compliance, slower throughput and increased product usage over time. The added direct and indirect costs negated any short-term cost reductions.
The Personal Apparel Assessment (PAA)
Manufacturers can positively impact their bottom line costs by conducting a Personal Apparel Assessment (PAA), which focuses on seven key disciplines and 35 best practices to determine potential areas for cost improvement. These disciplines include cost performance, injury reduction, productivity improvements, standardization, SKU reduction, training and controls. The objective is to create a more consistent, compliant and cost-effective personal protective equipment (PPE) program.
The success of this type of program will depend on the manufacturer's ability to track the results on an ongoing basis. Financial models have been developed to quantify, measure and document those results once the PAA has been completed and the recommendations implemented. This type of measurement will allow the manufacturer to gauge the program's success and verify true costs savings.
To conduct a thorough assessment, the manufacturer should align itself with a partner that has the ability to provide the necessary resources, quantifiable documentation and follow up capabilities to ensure successful results. The measurement and improvement process should not end once the recommendations from the PAA are implemented. Follow up to analyze any changes that occur within the organization and to assure that new products and ideas are properly introduced is just as important as conducting the initial assessment.
The Assessment Process
Conducting a PAA goes beyond examining applications and providing product recommendations. It involves developing a complete understanding of the various job requirements, identifying critical issues, analyzing application processes and any variables that may exist, and reviewing operating procedures and the effect they may have on employees. Providing true solutions that will positively impact the work place will be impossible without a thorough analysis of the entire process.
A successful assessment will require the support of key functions within the organization, including finance, operations, procurement, safety and, where applicable, union representatives. In most cases, each of these departments has its own initiatives. The assessment will help each department determine which disciplines and their associated best practices represent the greatest opportunities for cost savings.
Cost Performance
Measuring the cost performance of a manufacturer's PPE products is critical to controlling the company's expenses. The objective is to identify optimum product solutions and implement best practices that will maximize performance. Employees must be asked for their input so the assessor can gain insight into the total process and how PPE products are used.
It will also be important to benchmark the manufacturer's present PPE product costs. This benchmark will allow the manufacturer to use the financial models that will be put into place to measure the results of the recommendations that are implemented and to compare costs. The manufacturer will then be able to document the actual cost savings that result.
Injury Reduction
The Occupational Safety and Health Administration (OSHA) recently issued a report indicating that 70 percent of the workers that experienced hand injuries in manufacturing operations were not wearing gloves. Hand injuries among the remaining 30 percent occurred because hand protection was inadequate, damaged or misapplied.
The objective of any PPE program is to provide solutions that significantly reduce recordable and non-recordable hand injuries and their associated costs. Wearing PPE is often a personal thing as far as employees are concerned. The OSHA study seems to indicate that many companies are not providing PPE products that are acceptable to employees and provide the levels of protection needed for specific jobs. The direct (medical expenses) and indirect (lost time, decrease in productivity) costs resulting from hand injuries can be enormous. Analyzing this discipline and implementing best practices provide manufacturers an opportunity to reduce injuries and related costs.
Productivity
Manufacturers often find it difficult to determine the effect of change on productivity. Whereas productivity gains may be very positive in one department, they may create significant bottlenecks in other areas of the operation. Because of these inconsistencies, this discipline and its associated best practices probably represent the greatest opportunity for operational improvement. The more units that go out the door, the greater the potential for reducing the cost of each unit of manufactured product.
Again, one of the keys to measuring productivity gains is to have a financial model that can capture and quantify the results of changes that are implemented. Significantly reducing downtime and rework/spoilage and improving labor efficiency and output will result in measurable productivity gains and greatly reduced costs.
SKU Reduction
Organizations that have the ability to minimize the number of stock-keeping units (SKUs) can directly and positively impact their working capital. An SKU reduction can be achieved by eliminating redundant and/or duplicate products currently in use at a single or multiple sites. Eliminating redundant products and the time required to order and stock these products will result in a more efficient supply chain management system.
SKU proliferation may occur because multiple personnel have the authority to approve the use of new products. The best practice of giving only one or two managers the authority to approve new suppliers or products will help eliminate product proliferation.
Standardization
Every organization wants to create a safer and more consistent environment for its workers. Standardizing the products used throughout a plant and across multiple sites will help reduce the likelihood of non-compliance.
To promote standardization, the organization must determine the optimum product for a specific job and then assure this product is used for all similar applications throughout the plant and across multiple facilities. Tool crib/stores managers should produce a report detailing glove styles and usage by department and share this information with their counterparts as a best practice.
By standardizing products across similar applications, an organization can achieve a net reduction in its carrying costs and the cost of capital. Standardization could also lead to a more consistent level of performance and reduce the risk of injuries.
Training
Worker education is a vital component within every department that is involved in the manufacturing process. Whether workers are wearing gloves, apparel or eyewear or working with hand tools, training will significantly impact how well a job is performed. Training also directly correlates to the other disciplines discussed in this paper.
Educational tools and resources should be easy to use and available to all employees. These tools may be as simple as departmental glove boards or access to material safety data sheets that instruct workers on the proper use of protective devices.
Training should be offered for cross-plant education and best practice implementation. Some companies, for example, have been successful in creating Web-based training, which is available to employees at multiple sites.
Training is a continuous process that must be administered for new employees as well as those involved with any process of product changes. Instituting an ongoing training program will reduce operation risk for employees and the overall organization.
Controls
The controls discipline tends to represent the greatest opportunity for directly impacting costs. Optimizing the way PPE is dispensed, used and disposed of is critical if an organization is going to achieve its cost reduction mandates. Employee participation and compliance directly influence waste reduction and costs
Spoilage, waste, misapplication and non-compliance all result from not having the proper control mechanisms in place. Well-defined policies and procedures should be implemented, with employees educated about the company's goals.
Instituting best practices such as examining product usage and determining whether a product is being used to the end of its expected life, isolating abnormal usage areas and conducting audits will help assure that control measures are successful. Manufacturers should work with their PPE provider partners to identify the most effective control mechanisms.
A company, for example, may replace an old procedure with a new one, such as instituting a sign-out process for obtaining new gloves or apparel. Manufacturers may opt to install automated dispensing equipment or initiate laundry programs. Recycling is another alternative for potentially reducing waste and costs. A PPE provider partner can recommend recycling operations that will purchase used Kevlar, which is broken down and used in other products.
Continuous Improvement
The PAA will identify a manufacturer's strengths and areas that represent the best opportunities to reduce costs as they relate to the seven key disciplines. Implementing the recommendations and testing the new products and or processes are the next steps. As mentioned earlier, having the ability to quantify the results is critical to determining the program's success.
To remain competitive, manufacturers must continually evaluate their processes and implement improvements that can be quantified and documented. This will only be possible if the appropriate financial models are in place. It is important that manufacturers align themselves with a partner that has a proven track record and can provide the support required to foster a successful long-term PPE program.
About the author:
Mike Kimberley is the director of strategic account development at Ansell Healthcare. Headquartered in Red Bank, N.J., Ansell is a leading provider of hand and clothing apparel, along with productivity solutions that enable companies to achieve and surpass their cost and productivity objectives. Working directly with plant personnel, Ansell uses its experience, knowledge and proven products to develop programs that guarantee results in the areas of safety and efficiency. For more information, visit www.ansellpro.com.
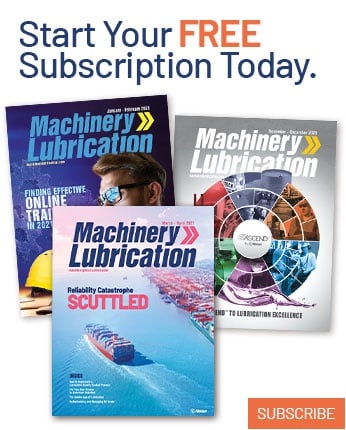