Computer numerically controlled (CNC) milling machines and machining centers have brought about the need for more capable and universal milling cutters. The development of more advanced milling tools over the past few years is a response to this requirement.
In the past, a dedicated or special tool was in many cases the only efficient solution for many applications, especially as batches were large. Today, when more flexibility in production is needed, new milling cutter concepts are providing broadly capable tools. Modern tool design and manufacturing have made it possible to realize sophisticated tool concepts that utilize CNC machine tools, increase production output and make the machining process more reliable.
Breaking the Mold
Standardizations in technology are, of course, crucial to manufacturing because, through them, we speak the same language and know the limits that apply. But there are instances when standards actually break the pace of development. It then becomes necessary to escape from the constraints that hinder the introduction of better solutions. One such instance is the development of milling tools.
Milling cutters and inserts used to be defined by ISO standards and offered users interchangeable tools from different tool suppliers. But having to comply to standards imposed limitations on the milling cutters and inserts. ISO codes prescribe shape, thickness and inscribed circle of cutting inserts, as well as indicate the size of insert-holding cartridges and wedge clamps, along with the tool bodies that hold them. With only a limited scope in insert grade, hone and chip-breaker design, tool suppliers and users adhering to ISO standards faced serious technological and performance limitations.
In contrast to ISO-style milling tools, today’s milling tool concepts provide tool developers with the freedom to use new cutter and insert designs. These can be optimized to provide better all-around capability for CNC machining. Machining security, accuracy, surface finish, capability for different cutting paths, removal rates, tool overhang and high-speed machining are issues that can be tackled better through new cutter concepts.
Today’s concept milling tools, optimized for operations and materials, are widely accepted throughout industry. Approximately 80 percent of all the milling tools supplied from Sandvik Coromant, for example, are CoroMill cutters. These remove metal several times faster and with smaller and more suitably directed cutting forces than would be possible with any ISO-standard cutter. With only a fraction of the typical run-out of ISO cutters, concept cutters consistently hold closer component tolerances and also develop less (and more favorable) cutting-edge wear. Axial and radial run-out is at a minimum, and this means better cutting-edge accuracy for improved surface finish, tighter part tolerances and longer tool life. They also distribute machining loads evenly to cut faster with less noise, vibration and wear.
These modern concept tools also provide the technology for high spindle speeds, fast-feed milling and hard part machining, as well as expanding opportunities for dry milling. CoroMill design features make the concept tool leaner in design, needing a minimum of setting and maintenance. Rigid and accurate cutter bodies are machined from pre-hardened steel with inserts located accurately in milling cutters that provide choices of different tooth pitches to suit applications.
Truth and Consequences
The consequences of using outdated milling tools can be substantial to machining economics as well as production security. Machine shops that carry and use milling cutters that are not part of more recent concept developments are losing out to a notable degree in their capability to be competitive in manufacturing. Investing in sophisticated machining centers and other rotating-spindle machinery for milling but not continually updating the milling tools and inserts is only going half the distance.
With the advance in cutting tool technology and CNC machining capability, there is a growing potential for manufacturers who have up to now been using outdated dedicated milling cutters, boring tools or special tools. Often, these tools are specifically designed or applied for certain cuts on a component or a family of components. This has meant that when it comes to rotating tools in machining centers, a separate tool is needed for each dimension on a component.
The use of specifically dimensioned tools goes back partly to when milling and boring operations were all performed in milling machines or special-purpose machinery with limited axis-capacity. Particularly when it came to internal machining, a tool had to be made available for each diameter, face, chamfer and groove – even when the variation was only a matter of a few millimeters. Some limited flexibility could sometimes be built in through the use of adjustable insert seats in cartridges.
With the wider availability of multi-axis CNC machining centers, tool movement is no longer a limitation. In effect, it provides the possibility of using one tool for several, if not all, of the different cuts needed. The ease of programming various tool paths, and using methods such as ramping and circular interpolation, means that a flexible, more widely capable tool can be applied, with dimensional variations on the component only being a simple program adjustment.
Added Production Time with Fewer Tools
A European off-road vehicle manufacturer benefited through the application of modern concept milling cutters in an FMS line consisting of horizontal machining centers. The line machines different types of housings for axles for wheel loaders. As part of a major efficiency project aimed at improving performance in the manufacture of components for powertrain assemblies, one particular objective was to improve machining of side housings through increased productivity.
Previously, the FMS line used special boring tools to machine the various sizes of the cast-iron side housings. Each component has several different internal diameters and faces that are machined. In the machining analysis that took place, it was recognized that concept cutters could replace several of the previous boring tools by not being specific to bore sizes, etc. A smaller-diameter long-edge cutter could, for instance, be used to interpolate, and thus machine, a range of bore sizes. All that is needed for a different dimension to be machined is a program change. The cutters are, as such, universal for various dimensions and operations.
Operators also see the new level of process security as a big advantage in their work, as well as the ease and reliability with which tool setting and maintenance is carried out. Insert clamping is easy with the center-screw used in the CoroMill cutters. The right torque is achieved through the accompanying torx key. This is a small but significant point toward achieving process security.
The results of the machining upgrade with CoroMill concept milling cutters, with Coromant Capto integrated couplings, included a reduction in machining cycle time of 25 percent, the reduction of the number of tools by 50 percent and a higher process security level. The new machining method has also reduced component setups in the machine. It is estimated that another 10 percent of production time has been made available through the machining improvements.
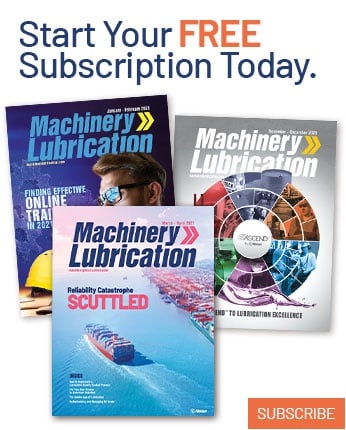