Why do we need formal scheduling? This is a legitimate question. If we have already established a maintenance planning process, shouldn't we have reduced job delays? Shouldn't we have gradually found out the tools and materials required by most equipment jobs? Shouldn't jobs with planned time estimates insure that craft personnel don't spend too much time on jobs? Why do we need to invest the additional time and effort to create a formal maintenance schedule?
Unfortunately, simply having maintenance planning without scheduling does not increase wrench time (time spent actually on jobs in the field). Delays occur not only during jobs, but between jobs as well. Planning an individual job to have the proper skills, instructions, materials and tools helps reduce delays during the execution of that job, but does not directly reduce any delays between jobs. You would think that if craft personnel execute individual jobs more quickly, they would execute more jobs overall. Nonetheless, actual experience shows that even with planning, wrench time does not improve much without formal scheduling.
Several main keys help explain this phenomenon. These keys involve the past experience of assigning work, the lure of urgent work and inadequate assignment methods.
First, many plants come from a background of having poor storerooms, inadequate bills of equipment, and little, if any, formally planned work. Supervisors under these circumstances developed experience knowing how many jobs a person might reasonably accomplish in a day. Against the obstacles of obtaining parts and other problems, it might take all day long to finish only one or two maintenance jobs. However, with improved storerooms, planning and other maintenance aids, we often find these supervisors still relying on their past experience and only assigning one or two jobs each day.
Second, the culture of maintenance remains in many plants to resolve plant emergencies and urgent work only. There is never much pressure to work the non-urgent maintenance tasks diligently to keep ahead of minor problems. These plants frequently have large backlogs of low-priority work, and the operators feel that maintenance assigns hidden priorities of "now, tomorrow or never." These plants see delays between jobs after they complete the emergency work. Even in plants that do not think they are merely doing urgent work, there is often a mind-set of not really having that much other work or a reluctance to assign yet another low-priority job after the troops have victoriously conquered the latest emergency.
Third, the true assignment practices in many places are heavily drawn toward either assigning one job at a time with the expectation that the craft personnel will come back for another job when finished or not assigning specific jobs at all with a misapplication of the notion of empowerment. Assigning a single job at a time ensures that peer pressure will wreak havoc with productivity. People who consistently finish jobs on time and go back for more work subject themselves to ridicule from slower people. At best, the most conscientious people are resentful that they do more work than others. In addition, never knowing what "the next job" will be stirs the imagination that the next job will be a worse job that the one in hand, which encourages slowing down.
Many plants have also taken empowerment to the extreme of allowing technicians to pick what they should be working on altogether. This practice brings out the worst of the second point about tackling only reactive work. We would be better off from a productivity standpoint telling the technicians what their assignments are and then empowering them to execute that work. These factors of relying too much on past experience to assign work, primarily focusing on reactive work and other inadequate assignment methods, work as powerful agents to keep wrench time low, even at plants with maintenance planning functions.
Fortunately, with this information guiding us, we see that we need some method to determine how much work we should execute. This method is formal scheduling. Instead of the question being, "Why do we need formal scheduling?" the question should be "How much work should we do next week?" The answer is best determined by having a formal scheduling method if we want to improve wrench time dramatically.
Doc Palmer is the author of the “Maintenance Planning and Scheduling Handbook.” He is a CMRP and has nearly 25 years of industrial experience as a practitioner within the maintenance department of a major electric utility. From 1990 through 1994, he was responsible for overhauling the existing maintenance planning organization. The resulting success played a role in expanding planning to all crafts and stations owned and operated by the utility.
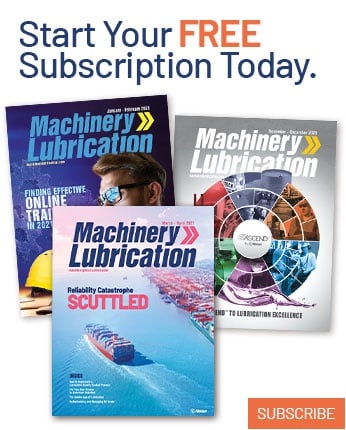