While on a gemba walk, I saw a section of the warehouse that was neat, clean, organized and free from the piles of inventory awaiting disposition that typically would be stacked up in this location. After seeking out the team leader of the area, I complemented him on the organization and improvement to the flow of these parts. Of course, he was happy I noticed.
I asked him what were the countermeasures used to make the improvement. He said that a special tour was coming through today and he had all the parts moved outside into several empty trailers. Yes, it took several semi-truck trailers. By hiding the parts outside, the tour path was quickly cleared and the results were impressive looking.
I am sure his manager passed on the message that the tour was forthcoming and to make sure the area was tour ready. This team leader naturally did what he thought was the best and quickest action – just hide it.
Although I find that the “just hide it” countermeasure is an extremely popular one, it is one method that I strongly argue against! The entire activity is muda (waste) from buying, renting, securing trailers to loading, stacking, unloading items in and out of the trailers. Not to mention that we may need some of these parts for production during the hiding process. This creates additional muda to search for the parts and retrieve them including moving other parts around to get to the parts we need. What about potential damage to these parts causing us to delay customer orders, scrap or rework parts, reorder parts, expedite parts, air ship them in and out to the customer? What about missing parts as a result of doing a fantastic job of hiding them? Of course, our burden of paperwork, tracking and reporting just increased. All for what? Just to make our plant look good for a tour.
It is also a clear indicator that we have a long way to go on our lean journey. By hiding our problems, we create muda and, more importantly, we ignore the real problems. It is better to make the problems more visible and deal with it even at the expense of “looking good” for a tour.
About the author:
Mike Wroblewski started his lean journey with instruction in quick die change from Shigeo Shingo. Mike is president of Victory Alliance Technologies, a Greensburg, Ind., firm that specializes in lean implementation. He writes a blog called " Got Boondoggle?" featuring lean and Six Sigma topics. Mike can be reached by e-mail at mwroblewski@victory-alliance.com.
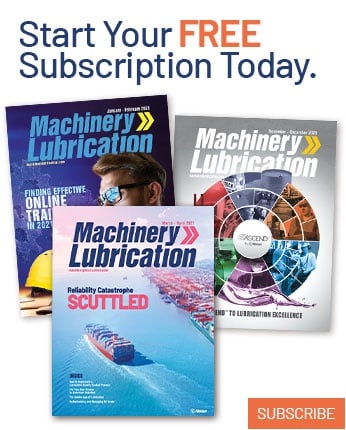