Assessments of plants' steam systems can identify opportunities for substantial savings; for example, a survey of the boiler, steam distribution and condensate systems of this Colorado refinery identified $1 million in potential energy cost savings a few years ago.
To help U.S. manufacturers reduce their energy use and operating costs, the U.S. Department of Energy ( DOE) conducted 200 expert Energy Savings Assessments (ESAs) of U.S. industrial steam and process heating systems in 2006.
The ESAs were conducted at energy-intensive plants in such industries as aerospace, aluminum, chemicals, electronics, food processing, forest products, glass, metal casting and steel. In each assessment, professionally trained ESA Energy Experts using DOE Industrial Technologies Program ( ITP) software tools worked with in-plant staff to evaluate the plant's process heating or steam system and identify opportunities for savings.
Potential annual energy cost savings for those 200 assessments totaled approximately $485 million. Implementing the energy-saving improvements recommended in the ESAs could trim the participating plants' yearly energy costs by an average of 7 percent. Even if your plant didn't schedule an ESA in 2006, however, or you haven't applied for one in 2007, you can still make use of ITP's many resources to start saving today.
To help you get started, here are the 10 most frequent ESA recommendations for improving process heating and steam systems, from a list of more than 40 compiled following the 2006 ESAs. Links to helpful DOE ITP Best Practices tip sheets follow each recommendation. The tip sheets contain more information and resources to help you optimize the energy efficiency, productivity, and competitiveness of your plant.
Top 10 Recommendations from the 2006 ESAs |
Some of the following documents are available as Adobe Acrobat PDFs. Download Adobe Reader. |
1. Improve boiler efficiency (steam)
|
2. Reduce steam demand by changing process steam requirements (steam)
|
3. Improve insulation (steam)
|
4. Reduce the oxygen content of flue (exhaust) gases (process heating)
|
5. Implement a steam trap maintenance program (steam)
|
6. Change condensate recovery rates (steam)
|
7. Modify the feedwater heat recovery exchanger using boiler blowdown (steam)
|
8. Properly insulate and maintain furnace structure or parts (process heating)
|
9. Add or modify operation of backpressure steam turbine (steam)
|
10. Implement a steam leak maintenance program (steam)
|
Additional Resources
For more information about how to improve your plant's process heating or steam system efficiency, see the following resources.
Improving process heating system efficiency:
- More process heating tip sheets
- Improving Process Heating System Performance: A Sourcebook for Industry ( PDF 1.2 MB) Download Adobe Reader.
- More technical handbooks, guides, and technical briefs on process heating
- Process Heating Assessment and Survey Tool ( software)
- Process heating assessment training
Improving steam system efficiency:
- More steam system tip sheets
- Improving Steam System Performance: A Sourcebook for Industry ( PDF 1.26 MB) Download Adobe Reader.
- More technical handbooks, guides, and technical briefs on steam systems
- Suite of Steam System Assessment Tools ( software)
- Steam system assessment training
For more information about ESAs, including those planned for 2007, visit the Save Energy Now Web site.
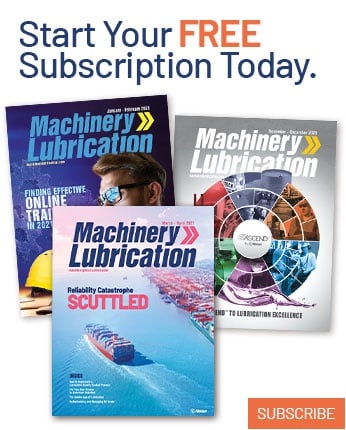