One of the best aids in sustaining a daily 5-S process is found in the 5-S Assignment Chart. This assignment chart lists all the 5-S tasks to be completed in a zone (designated area) along with the frequency the task should be done (daily, weekly, monthly), the person’s name responsible for completing the task and listing of the tools needed for each task (broom, towel, etc). All you have to do is post this assignment chart in the zone to help insure the tasks get done. Sounds simple enough, right?
Like most concepts I have learned in lean manufacturing, it goes much deeper than what we originally think. That holds true for even the simple 5-S Assignment Chart.
For one, the posting of the 5-S assignment chart, or for that matter, any other document, sign, work instruction, standard work sheet or preventive maintenance task list, itself does not insure that the tasks are completed or followed as described. You learn that rather quickly after the initial excitement of the newly posted item turns towards the mundane. We sometime fall into the trap that anything posted is important therefore everyone will follow it. Not true. Just look at speed limit signs as an example.
So how do you use a 5-S Assignment Chart successfully?
Here are just a couple of ways I found that work.
1) In the first column, organize alphabetically by name, the person responsible followed by the task, frequency and tools assigned to them. Typically, we list tasks first which makes it more difficult to see who is responsible and harder for the person responsible to find their assigned task. Make it easy (more visual) for each person to find their own tasks.
2) Cluster all the tasks for each employee together if they have more than one task assigned to them. Again, makes it easier to find all your assignments.
3) Have all the team members divide up tasks and who is responsible. In most cases, a leader normally just assigns who gets what task and some people don’t like the results. A team approach on this point gets better buy-in.
4) Under frequency, be more specific. Don’t just say weekly, specify the actual day of the week, i.e.Tuesday.
5) In addition to assigning specific days, make frequency visual. For example, use a column for each day of the week adding a symbol on the assigned day for each task. If the task is daily, put a symbol in every column of the week for that task and put it in color.
6) Assign a daily task(s) to every person. The 5-S process works best if done daily so base your task listing with daily assignments.
7) Keep assignments simple. Assigned tasks should be completed in a daily five-minute period.
8) Have each employee sign off individually (and daily) after completing their task. This, by itself, is not the complete answer however it is better than having someone else (a zone leader or supervisor) signing off for all tasks.
9) Have the zone leader or supervisor (as part of their standard work) check and review each day that the tasks for that day were successfully completed. Their job is to coach and support employees. If a task was not complete, ask the person responsible “Why not?” and “What can I do to help you get it done?”
10) Use the best management tool, the power of “Leading by Example”. Every leader should have a daily assignment and complete them daily.
11) Rotate the task assignments often. Share the burden and eliminate the boredom.
About the author:
Mike Wroblewski started his lean journey with instruction in quick die change from Shigeo Shingo. Mike is president of Victory Alliance Technologies, a Greensburg, Ind., firm that specializes in lean implementation. He writes a blog called " Got Boondoggle?" featuring lean and Six Sigma topics. Mike can be reached by e-mail at mwroblewski@victory-alliance.com.
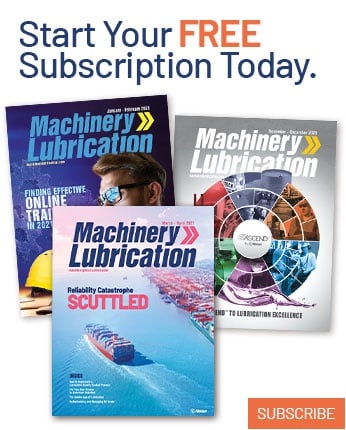