Every day it seems more and more manufacturers are discovering the enormous power of investing in reliability. Truthfully, where else can you get returns of 10:1, 20:1, 50:1 or more?
But, here’s the problem. As companies travel down the road to reliability, they quickly learn that there are no “silver bullets.” The fact is, it takes a significant amount of time and effort to be successful.
For starters, they find out that they need to do more predictive maintenance, more planning and scheduling, more failure modes and effects analysis, more root cause analysis. Furthermore, they realize they need to improve the craft skills of their workforce.
Plus, they learn that reliability is not just a maintenance issue – everyone is responsible for reliability. That means operations, procurement, engineering, leadership and maintenance all have to be engaged and working together toward the common goal.
So eventually, it all comes down to this: How in the heck can you get all of this reliability work done when you are already buried with existing work? That’s a good question. Keep reading for the answer.
The Truth About PMs
If you were to take a quick look at your maintenance backlog, what would you see? A long list of work orders that will take months to complete?
The reality is that most maintenance activities have just evolved over time. Very few programs have been engineered for true efficiency and cost-effectiveness. Consider what happens whenever a piece of equipment fails. The typical response is to add a preventive maintenance (PM) task such as more cleaning, lubrication or inspection.
Another failure? Add another PM.
Before you know it, so many PM activities creep into your system that it becomes a bottomless pit of work.
Full of Waste and Ripe for Lean
There is enormous potential for improving the speed, quality and cost of preventive maintenance by applying basic lean thinking.
The key is to look carefully at your PMs at the task level, especially work that is simply “the way we’ve always done it.” Now, let’s call it by a new name: waste.
What exactly is waste? Put simply for this discussion, it is any PM work that doesn’t add value in the eyes of your customer. What’s important to realize is that waste is the top factor that adds unnecessary time, cost and complexity to your workflow.
Therefore, your biggest challenge may be to recognize waste and not accept it as “the way we’ve always done it.”
Accelerate Reliability with Lean Tools
If you view your PM program through lean eyes, you will be surprised by all the work you do that is non-value-added. You see, you can spend plenty of time and effort getting really good at PMs that don’t add value. So, the real question to ask yourself is this: Does this PM task help us improve our manufacturing capacity and output? If the answer is no, then quantify the task and eliminate it.
The results can be tremendously liberating because now you have unlocked resources (time, money and manpower) that can be devoted to new reliability practices that really do add value, yet seemed impossible before.
Target the 60 Percent
In my experience analyzing maintenance work at all kinds of plants, I’ve found that, on average, 30 percent of all preventive maintenance activities do not add value and should be eliminated. What’s more, another 30 percent of these activities could be replaced with condition-monitoring technologies and the predictive maintenance approach.
In other words, more than half of all PM work could be stopped immediately – or replaced with predictive maintenance – without any consequences.
The Reliability Payoff
The good news is that PM evaluations routinely exceed a 10:1 return on investment. So, just by applying basic lean principles and lean tools to your PM program, you can harvest enough low-hanging fruit to get terrific leverage on your reliability efforts.
Best of all, it’s a great way to turn reliability into a self-funding program.
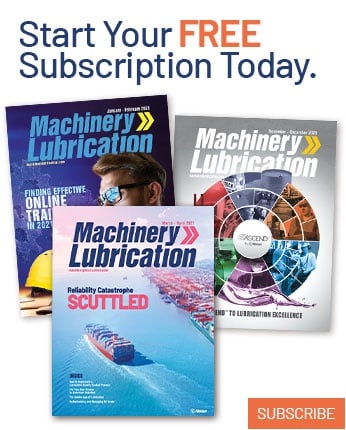