Ultrasound inspection offers a unique position for condition monitoring as both a "stand-alone" inspection technology and as an effective screening tool that can speed up the inspection process and help inspectors determine effective follow-up actions for mechanical, electrical and leak applications.
Whether you refer to proactive inspections as "predictive maintenance" or "condition monitoring," the goal is the same - to note a deviation from a normal or baseline condition in order to determine whether or not to take corrective action in a planned orderly manner and to prevent an unplanned incident.
The ideal end result is to maintain asset availability, reduce maintenance overhead and improve safety conditions. Not one technology can cover everything. The recommendation is to incorporate as many technologies as possible into inspection procedures to assure reliable results.
This paper will review the basics of ultrasound technology, what is new to the technology and how it is used for condition monitoring to locate safety hazards, reduce energy waste and improve equipment availability.
Photo 1. Ultrasonic instruments can help your maintenance organization become more proactive and accurate.
ULTRASOUND TECHNOLOGYAirborne/structure-borne ultrasound instruments receive high-frequency sounds produced by operating equipment, electrical emissions and leaks. These frequencies typically range from 20 to 100 kilohertz and are beyond the range of human hearing. The instruments electronically translate ultrasound frequencies, through a process called heterodyning, down into the audible range where they are heard through headphones and observed as intensity and/or decibel (dB) levels on a display panel. The newer digital instruments utilize data management software where information is data-logged on the instrument and downloaded to a computer for analysis. Some instruments contain on-board sound recording to capture sound samples for spectral analysis.
What makes airborne ultrasound so effective? All operating mechanical equipment, electrical emissions (arcing, tracking, corona) and most leakage problems produce a broad range of sound. The high-frequency ultrasonic components of these sounds are extremely short-wave in nature. A short-wave signal tends to be fairly directional and localized. It is, therefore, easy to separate these signals from background plant noises and to detect their exact location. In addition, as subtle changes begin to occur in mechanical equipment, the subtle, directional nature of ultrasound allows these potential warning signals to be detected early, before actual failure.
Most of the sounds sensed by humans range between 20 hertz and 20 kilohertz (20 to 20,000 cycles per second). The average human high-frequency threshold is actually 16.5 kHz. These frequencies tend to be relatively large when compared with the sound waves sensed by ultrasonic translators. The lengths of low-frequency sound waves in the audible range are approximately 1.9 centimeters (3/4 of an inch) up to 17 meters (56 feet), whereas ultrasound wavelengths sensed by ultrasonic translators are only 0.3 cm (1/8") up to 1.6 cm (5/8") long. Since ultrasound wavelengths are magnitudes smaller, the "ultrasonic environment" is much more conducive to locating and isolating the source of problems in loud plant environments.
The high-frequency, short-wave characteristic of ultrasound enables users to accurately pinpoint the location of a leak, electrical emission or a particular sound in a machine.
The basic advantages of ultrasound and ultrasonic instruments are:
-
Ultrasound emissions are directional.
-
Ultrasound tends to be highly localized.
-
Ultrasound provides early warning of impending mechanical failure.
-
The instruments can be used in loud, noisy environments.
-
They support and enhance other predictive maintenance technologies or can stand on their own in a maintenance program.
When used as part of a condition monitoring program, ultrasound instruments help improve asset availability and save energy.
Once established, ultrasound can be used as the first line of defense to:
-
quickly inspect equipment
-
screen out anomalies
-
set up alarm groups for detailed analysis and further action
With the most recent advances over the past few years, ultrasonic detectors have become much more sophisticated and have gone from just a listening device that is quite subjective to a system that can store test data, record sound samples and analyze both the data through data management software and the recorded sound samples with spectral analysis software.
With these new advances, using ultrasound to separate good operating equipment from bad is as easy as 1, 2, 3.
-
Listen and observe.
-
Note deviations and record the translated ultrasonic signal.
-
Analyze and review.
Let's examine the possibilities of what can be done to save time, locate deviations and save energy. First, listen to the translated ultrasound and observe the decibel level. Note any deviations from previous readings as you continue your route. Record the data and any sound anomalies. Then, analyze the data and sounds to consider if additional action is necessary. All of this can be accomplished very quickly.
Here are a few case studies of how ultrasound helped avoid equipment breakdown.
Figure 2. Spectrum of inner bearing.
COMPRESSOR VALVE LEAK DETECTION
With a shutdown scheduled with very little advanced notice, a major mining operation had to determine ways to reduce the manpower requirements on their preventive maintenance schedule. Normally, it changed out all of the valves on its large (2,000-horsepower) compressor, but the site decided to use ultrasound as a method of determining which valves to change, and thus reduce the manpower requirements. After checking the valves, it found that only a small fraction of the valves needed to be changed.
Figure 1. UE-UT reading on outboard and inboard oil pump bearings.
MAIN POWER TRANSFORMER ANOMALYA main power transformer for a large utility began to show signs of heating up with infrared scans on the top of the transformer near two of the three output insulators. It was decided to investigate the oil recirculating pumps to see if they were possibly the problem. These pumps had been in service for seven years and had an expected life of more than 10 years. An ultrasonic scan of both the inboard and outboard bearings on several transformer oil pumps of the same age found that most had readings of 20 to 30 dB. Twelve of the 14 pumps on the suspect main transformer had readings in the range of 50 to 70 dB. The increase of 30 to 35 dB in only these 12 oil pumps out of more than 100 oil pumps tested was considered to be very unusual, and needed further investigation.
These decibel readings on the oil pump inner and outer bearings give the ultrasound operator excellent information about what might be causing the higher temperature readings on the top of the transformer and subsequent high gas readings. They can be used to help evaluate risk of going to higher loads.
Figure 2 (on Page 40) is a time series image of the inner bearing wave file. It is very close to the pump outflow, and from the "spikes" that come considerably above the baseline, it is easy to see that there is a high probability that there is cavitation occurring at the pump output. This has initiated further action to determine if the high decibel readings were caused by the pumps being wired incorrectly, causing the pump to rotate backward.
FAULTY GEARSAn ultrasonic signal viewed through a vibration analyzer can help isolate faulty gears.
The time waveforms at below (figures 3 and 4) were taken on identical gearboxes in a tubing manufacturing facility. There are six gearboxes coupled together, each driving tooling that bends steel to form tubing. The inspector was out collecting data with a vibration analyzer and an ultrasound instrument when he came across the following gearboxes. A vibration time waveform was taken with an accelerometer. When listening to the gearboxes with the ultrasonic instrument, most of them had a hissing type sound. One gearbox had a ticking sound to it and was captured in a time waveform first using an accelerometer and then with the ultrasonic instrument. These were then compared to the gearbox right beside it. The time waveforms in figures 3 and 4 show the results.
By comparing the two time waveforms, a slight difference in the two gearboxes can be observed. Note the time waveforms that were captured with ultrasound in figures 5 and 6. The problem becomes more defined.
The ultrasonics time waveform shows the broken tooth or teeth in Gearbox A. By the use of ultrasonics, this problem was caught in an earlier stage.
Figure 3. This is the time waveform of Gearbox A using vibration.
Figure 4. This is the time waveform of Gearbox B using vibration.
Figure 5. This is the time waveform of Gearbox A using ultrasonics.
Figure 6. This is the time waveform of Gearbox B using ultrasonics.
Figure 7. This is the spectral image of arcing.
Figure 8. This is the time series view of arcing.
ELECTRICAL INSPECTIONUltrasound instruments detect ionization produced by arcing, tracking and corona, and can be used to locate problems in all voltages with the majority of applications in the mid- to high-voltage range. While infrared is typically used to locate electrical problems, there are "sound" events that could go undetected when relying on infrared thermography alone. Enclosed cabinets can be scanned, transformers can be probed and corona can be detected in high-voltage equipment. Sound samples can be recorded for analysis and spectral or time series views placed in reports.
The images at left demonstrate the effectiveness of ultrasound when used with infrared. An inspector who utilizes both ultrasound and infrared technologies was inspecting switchgear. Some of the doors could not be opened. There were no infrared ports on the closed cabinets and, therefore, this switchgear couldn't be tested with infrared. By scanning the door seams and air vents with the ultrasound instrument, the inspector heard a very distinctive arcing sound. He recorded the sound, and after the cabinets were opened, he took visual and infrared images. The results are displayed in figures 7 and 8.
The infrared image (Figure 9) shows that this failure condition could have resulted in flashover at any moment, which would have produced a catastrophic event.
Figures 9-10. The infrared image shows that this failure condition could have resulted in flashover at any moment, which would have produced a catastrophic event.
LEAK DETECTIONThe category of leak detection covers a wide area of plant operations. It can be looked upon as a way of keeping a system running more efficiently. Some plants include leak detection as part of an energy conservation program, while others perform leak detection for safety purposes or to reduce an environmental impact. No matter what, leaks can cost money, affect product quality and can wreak havoc with the environment.
The reason ultrasound instruments are so versatile is that they detect the sound of a leak and are not limited to just one type of leak. Leakage can occur in liquid or gas systems, pressurized and vacuum systems, internally (in valves or behind walls) or externally (through exposed piping).
For those instances where no pressure or vacuum can be created, an ultrasonic tone test can be used. An ultrasonic transmitter is placed on one side of a test item to flood an area with ultrasound. By scanning on the other side for sonic penetration, a leak can be located. As an example, this is used in the transportation industry to locate wind noise and water leaks around windshields.
The most common leak detection applications are used to save energy by locating compressed air and steam leaks. The U.S. Department of Energy has programs to help industry reduce energy loss through the Compressed Air Challenge, Steam Challenge and Motor Challenge. Learn more by visiting www.eere.energy.gov/industry/bestpractices.
Compressed air is one of the most costly utilities in plants today. The Department of Energy estimates that upward of 30 percent of all compressed air produced in the U.S. is lost to leaks. An ultrasonic compressed air leak survey can offer fast payback.
It is not uncommon to read of reports demonstrating savings in the tens of thousands and hundreds of thousands of dollars from compressed air leak surveys. A recent survey at a manufacturing plant is a typical example. This plant averaged an electric cost of $1.76 million to generate compressed air. The survey identified 3,561 leaks totaling 6,340 cubic feet per minute at an annualized cost of $597,000 of energy waste. A program of leak detection and repair can have a dramatic effect on the profitability of a company such as this.
Steam is another costly utility. Leaks in a steam system add to the energy cost. In fact, leaking steam traps not only waste energy, they can cause water hammer, which can damage steam system components and add to the operating costs. One steam trap can leak an average of 43 tons of steam per year. A steam leak and steam trap survey can provide substantial savings. One chemical company reported that the results of a steam trap survey in one of its plants demonstrated a savings of $1 million.
With escalating energy costs, the impact is affecting not only the bottom line but jobs. A recent National Association of Manufacturing newsletter reported that many companies are forced to cut jobs due to the high cost of energy. They mentioned that "energy prices have been a primary factor in the loss of 100,000 jobs in the chemical industry alone."
CONCLUSIONUltrasound condition monitoring provides many opportunities to improve asset availability, keep production on schedule and save energy. Applications for mechanical analysis, electrical inspection and leak detection cover just about all plant equipment. The basic ultrasonic instrument is relatively easy to use, while advancements in the technology have helped improve data management, analysis and reporting.
With escalating energy costs, ultrasonic technology can provide a cost-effective approach to reducing energy waste in compressed air and steam systems.
Alan Bandes is the vice president of marketing for UE Systems, a manufacturer of airborne/structure-borne ultrasound instruments. For more information, call 914-592-1220 or visit www.uesystems.com.
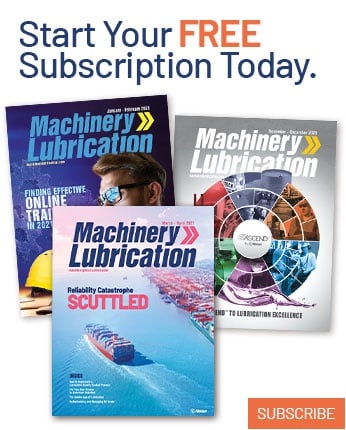