After rambling on in the last column about what wrench time is and how to measure it, I want to reinforce how hard it is to believe wrench time could be so low. The more we understand how hard it is to believe, the more we see why the opportunity is hidden.
Thirty-five percent is a typical wrench time for a maintenance workforce. Many managers find it hard to believe that a workforce's productivity could be so low. Some time ago, Danny Mallard provided me with a numerical scenario of how hard it seems it would be to intentionally try to achieve a wrench time as low as 35 percent. Mallard is a maintenance manager at Jacksonville Electric Authority's Northside Generating Station, an electric power plant.
Consider an average technician throughout an average day (Figure 1). Beginning a 10-hour maintenance shift, the technician first took 30 minutes to get started in the morning. This was essentially a check-in time where the crew met and the technician had a cup of coffee or two. The supervisor gave the technician several assignments and then the technician got busy. Yet, during the course of the day, the technician came back several times to the supervisor for various instructions and to clarify a point or two on the work. This time, receiving instructions took a total of 45 minutes. In addition, the technician spent 30 minutes during the day waiting at the tool room to check out some special tools. The technician also spent 30 minutes waiting at the storeroom obtaining parts. To move around the plant site, the technician spent 45 minutes of the day traveling.
So far, these times might not seem too unreasonable, but next consider breaks, lunch and check-out times. Instead of two 15-minute breaks, the technician took a total of 90 minutes in breaks (a whole extra hour) and 30 extra minutes for lunch. The technician also took 90 minutes for showering and otherwise preparing to go home at the end of the day. With all this wasted time (390 minutes), the technician had only 210 minutes left out of the 10-hour shift (600 minutes) for work. This time arrangement netted the technician a 35 percent wrench time and 65 percent delay time.
Can you believe it? Does it hit too close to home? The technician seems to have gone out of his way to avoid wrench time and still achieves what is thought to be an industry average rate. Incredible as it seems, the typical wrench time reported in industry ranges between 25 and 35 percent.
While some technicians at each plant are in more productive situations than others, studies show that overall productivity measurements are in this range. A few minutes here and there add up to a productivity problem with significant delays. In spite of the notion that wrench time could not possibly be so low, Mallard's plant conducted a wrench time study and found the average wrench time to be . . . 35 percent.
So, we see that the reality of wrench time can be surprising and yields an opportunity for improvement. Effective planning and scheduling addresses this opportunity in maintenance.
Figure 1. Is this really an 'extreme' scenario of delays?
Doc Palmer is the author of the “Maintenance Planning and Scheduling Handbook.” He is a CMRP and has nearly 25 years of industrial experience as a practitioner within the maintenance department of a major electric utility. From 1990 through 1994, he was responsible for overhauling the existing maintenance planning organization. The resulting success played a role in expanding planning to all crafts and stations owned and operated by the utility.
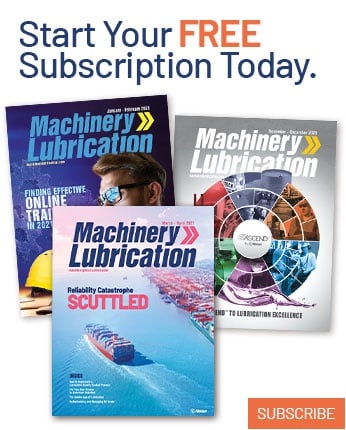