The primary product of DuPont's Titanium Technologies (DTT) business is titanium dioxide (TiO2), a white pigment used in the paper, plastics and coatings markets. In the
Dupont's NPEP Goal
DTT set a National Partnership for Environmental Priorities (NPEP) goal to reduce the generation rates of dioxin and dioxin-like compounds (D&DLC) at its three
NPEP Project Implementation
TiO2 is produced via chlorination of titanium-bearing iron ores, followed by oxidation, purification and finishing steps. Dioxin compounds are created as an unintentional byproduct formed during the chlorination step. DuPont's research and development organization did extensive research on the methods of reducing D&DLC compounds. Most were accomplished via source reduction. Longer-term, additional process changes with capability for even further reductions were studied and are in the process of being implemented.
One technology that DuPont TT studied/evaluated during the 2001-2005 period involved heating and separating the iron chloride to form metallic iron and chlorine. The heat of the process would simultaneousy destroy the D&DLC compounds. Another technological concept was to use filter bags impregnated with catalyst to react D&DLCs in a gas stream. While these options initially appeared to be viable and attractive, the source reduction strategies were ultimately deemed to be more sustainable.
The dioxin reductions were achieved via similar programs at all sites. There were parallel and phased efforts throughout the program. The essence of the technical effort over the period was to modify certain raw materials to reduce the organic D&DLC precursors that were fed to the process. Other technical programs involved controlling the process in a way that inhibited the reactions that produce D&DLCs. The basic premise was to reduce the oxygen, chlorine and organic reactants from the area of the process that forms the D&DLCs. Nearly all of the programs in the minimization effort were aimed at source reduction rather than end-of-pipe treatment. This remains true today as DTT seeks dioxin reductions greater than the 50 percent already achieved, eventually working toward a 90 percent reduction by 2007/2008 and additional reductions beyond that.
Hurdles Faced
After making the decision to focus on source reduction strategies, the main hurdle was designing the process changes appropriate for each of the TiO2 sites. While the sites had many similarities, there also were notable differences at key points in the process. Many of the changes introduced additional cost because of the need to modify equipment. Some other modifications tightened the acceptable ranges for running the process equipment, requiring additional process controls. Additional process controls, in turn, required increased training of operators and mechanics. Others involved permit modifications for changes in process emissions. One of the common changes for all sites involved revising specifications for one of the raw materials to reduce organic precursors that were being introduced to the process. To ensure that this raw material was within the new specification, numerous samples had to be collected and analyzed. The sampling and analytical program not only increased cost, but it also created a demand on site technical resources to assess and interpret the analytical results.
Waste Minimization Results
DuPont exceeded its original goal. D&DLC compounds were reduced at DuPont's United States TiO2 sites from 229 pounds to 85 pounds (63 percent) during the 2001 to 2005 period. Its two international sites in
From a cost standpoint, most of the changes made resulted in increased cost to DuPont. Some of the changes required capital investment in new equipment but resulted in reduced costs due to improved process yields.
According to a company release, “The payback is that we feel a high level of satisfaction internally by achieving a significant reduction in dioxins and improving HH&E. We are also proud of the fact that much of our success was achieved via science and technology that we had little understanding of four or five years ago regarding dioxins.”
Lessons Learned
Fundamental science and the use of Six Sigma tools were very important to the company’s success. The number of analyses that had to be done to understand baseline conditions and further to categorize reduction success or non-success was a huge eye-opener. During the program, and as it continues today, thousands of analyses had to be performed. Starting with a superior laboratory and the better analytical sensitivities therein proved to be a wise choice as analytical sensitivities and regulatory standards evolved.
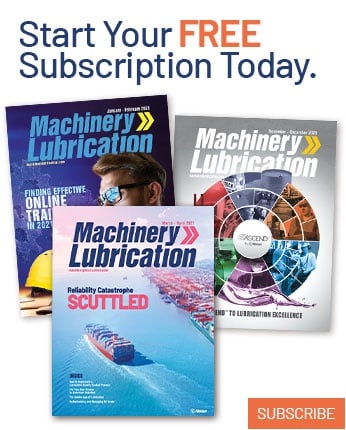