The next step is to involve operators in reliability with inspections, proactive work identification, work prioritization, and planning. Then, if it looks good, a facility can move on to operator-involved maintenance, where operators actually carry out certain maintenance tasks in lieu of the traditional maintainer.
For those implementing operator-driven reliability as part of a lean manufacturing journey, you're probably calling this Total Productive Maintenance (TPM). To help avoid common pitfalls, here are seven reasons why TPM initiatives can sometimes fail.
1. Operations (Production) Management Does Not Own OEE
This is arguably the most important element. If the operations/production management team is not accountable for driving Overall Equipment Effectiveness, or OEE (availability x yield x quality), TPM doesn't work.
Lean and plant reliability management initiatives, in general, don't work when this is the case. Reliability and OEE aren't about "maintenance," and they never were. Operations must recognize how TPM drives reliability, how reliability drives lean and how lean drives profit. They should have a sense of urgency to get the operators involved in the TPM initiative.
2. The Team Is Not Educated on the "Whats" and "Whys" of TPM
As stated above, reliability, counter to popular belief, is not simply a synonym for maintenance. Maintenance is about restoring equipment to an operational state. Reliability is about avoiding the loss of function in the first place. For a maintenance team, which has historically defined itself as the "fix-it" guys, reliability challenges their self-perception. Psychology is strong stuff.
They think, "If things aren't failing, what's my value contribution?" Likewise, despite the obvious importance of involving operations in the reliability equation, operators sometimes have trouble seeing this. We need ownership from both sides.
3. Failure to Start with Operator-Involved Maintenance
Often, TPM initiatives are driven by maintenance departments, and they skip improving operations and operator-involved reliability. Leery operations supervisors and operators often see this as a ploy - maintenance is trying to get operations to do its job.
Even if the initiative is driven from above the maintenance manager, operations may tend to blame maintenance, claiming that they're trying to shirk their responsibility and pass it off. It's best to start by standardizing proper operations.
From there, involve operators in reliability by having them carry out inspections, get involved in setting work completion priorities and clean the equipment (so it's easier to inspect). Gradually ease into operator-involved maintenance, where they actually perform maintenance work.
4. Inspections Get Too Technical and Too Complicated Too Fast
Organizations are smitten by cool predictive maintenance technologies, such as vibration analysis, thermography, etc. As such, they often skip the foundational visual and gauge-based inspections and move too quickly into the high-tech stuff.
This doesn't work very well, particularly at the operator level. The organization winds up wasting great sums of money and time training operators on highly technical material. They get overwhelmed and discouraged.
It's best to ease into the highly technical monitoring, focusing most of your effort on the fundamentals. As a tip, make all of your inspections binary - yes or no. Even quantitative data can be treated this way. For example, "the temperature is between 130 and 135 degrees Fahrenheit - yes or no." Keep it simple.
5. TPM Deployment is Superficial
Often in plants, we see very superficial implementations of TPM. So rather than Total Productive Maintenance, we get "totally painted machines" (as I've heard fellow Reliable Plant columnist John Schultz say so many times).
Usually, these are short-term, "window dressing" initiatives that yield no lasting value and sour the organization, so that in the future, should you try in earnest to implement TPM, the organization pushes back, claiming, "We tried that TPM stuff, and it didn't work."
6. Inspection Results and Proactive Work Identification Goes Nowhere
It's counter-motivational for a team to put in place inspection and work identification processes at the operator level, only to have the results ignored. That's a fast way to kill a TPM initiative. Your operators will lose interest and either fail to complete the work or "pencil whip" the inspections.
Can you really blame them? Nobody likes to do work that is effectively meaningless. Make sure you have the back-end ability to act on the inspections and complete the proactive work your operators are identifying to avoid having your TPM program stall from frustration.
7. Misalignment in the Rewards Structure
For decades, we've had reward system problems and misalignment. Design teams are rewarded to achieve functional capability at the lowest purchase price; never mind the downstream problems it creates for operations and maintenance managers and the true life-cycle cost of ownership.
Production teams are rewarded to hit a production number, whether there is demand for the product or not, and without respect for the effect their actions have on asset health. Maintenance teams always have been rewarded for failure, not reliability.
They get extra pay when the equipment is broke (overtime) and "atta-boys" from management for coming in to fix it at inconvenient times (while getting paid overtime, of course). If you were being rewarded for failure, would you want reliability? Would you step up and volunteer for a 10% or 20% pay cut?
People don't pay nearly as much attention to what their leaders say with their words as to what they do with their actions. If the leadership team is saying they want reliability, but they're paying for failure, both extrinsically and intrinsically, you'll get failure - the system is broken and must be fixed. TPM can't live in a misaligned reward structure.
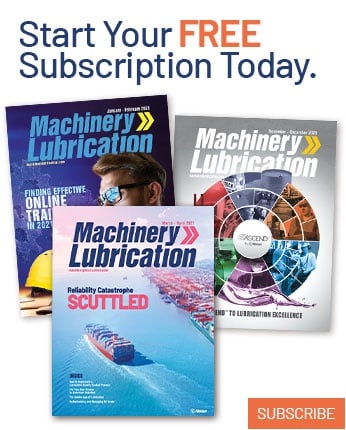