Management slogans often boil down to little more than platitudes in slick consultancy packaging. But some corporate lingo stands for more than a passing fad. “Lean manufacturing”, a shorthand for a commitment to eliminating waste, simplifying procedures and speeding up production, is one such concept.
Six Sigma, the quality-assurance principles that are often paired with lean efforts, is another. The principles and techniques that the two terms encompass have been shown to deliver impressive bottom-line results in industrial manufacturing.
To be sure, the taint of best-seller management slogans lingers over lean and Six Sigma, leading many executives to dismiss the terms as mere jargon or consultancy buzzwords.
“The western hemisphere is full of program-of-the-month syndrome,” says Anand Sharma, president and CEO of TBM Consulting Group, a U.S. firm that helps companies adopt lean and Six Sigma principles. “It’s more fashionable today to talk about ‘lean’ than to do it.”
But manufacturers that have gone beyond words to deeds and embraced lean and Six Sigma report tangible, sustained gains.
“This is not a program,” says Denny Van Zanten, manufacturing vice president at Pella, a major American window and door maker that first adopted lean methods 10 years ago and is still reaping the returns. “Lean is a part of Pella’s culture.”
Adds Stephen Printz, Pella’s chief information officer: “Here, lean is a way of life.”
Emerson Electric is another proponent.
“Lean is clearly a significant strategy for us,” says Steve Hamby, Emerson’s vice president of IT shared services. “It’s a concept, a strategy and a philosophy. This thing is real.”
Learning lean lessons
At the heart of lean manufacturing is a focus on the reduction of inventory and lead times. Production is driven by real customer orders, rather than forecasts that anticipate market demand. This means that demand “pulls” a product through production, rather than management forecasts “pushing” it onto the shop floor. Six Sigma, by contrast, is oriented to improving product quality and consistency by reducing the flaws that occur in manufacturing.
For many manufacturers, linking lean with Six Sigma is a perfect marriage, providing the tools needed to meet real demand with high-quality products in the shortest time possible.
“They are really complementary things,” says Bob Parker, research vice president at Boston’s AMR Research. “The whole is greater than the sum of the parts.”
Lean and Six Sigma have gained a following where other management cures have failed, largely owing to word of mouth and the demonstration effect of industry success stories.
“It starts with a CEO waking up in a cold sweat,” says Parker. “Maybe they know someone at GE and they’ve seen the amazing results.”
Internal pilot programs are also persuasive. A few divisions of U.S. manufacturer Emerson Electric began applying lean principles five or six years ago.
“Following that, as senior management saw different results at different locations, they began to raise lean’s visibility” within Emerson, says Chris Stephen, director of systems planning and e-business development. “They appointed a vice president at the corporate level with full-time responsibility to put together several plans and measurable results for lean.”
The impulse to adopt lean methods can also come from business partners.
After years of working with lean and Six Sigma principles, many companies realize that, to continue improving, they need to get suppliers and even customers involved — such as happened with Toyota.
“Companies get their suppliers into Six Sigma,” says Georg Reindl, Oracle’s European director of high-technology industry business. In Europe’s largest countries, he says, manufacturers “are all working in this direction and using lean.”
Once companies have adopted lean and Six Sigma principles, some benefits come quickly, others more slowly. But the beauty of lean manufacturing is its focus on continuous improvement, and, thus, on a steady flow of benefits. The most advanced users of the two techniques expand the concept well beyond the manufacturing process, and apply them to every corporate activity, even communications and processes involving suppliers. Here the focus is on a “lean enterprise” rather than simply on “lean manufacturing.”
Among the chief benefits are:
Cost efficiency: Many companies initially look to lean methods as a means to reduce manufacturing costs.
Indeed, an Economist Intelligence Unit survey of 83 manufacturing executives showed that 90 percent of respondents — the largest group — saw reduced costs as a goal of lean/Six Sigma programs (see Table 1).
But lean veterans warn that focusing solely on costs is shortsighted. The savings come, to be sure, but an exclusive focus on cost reduction can leave a manufacturer with unsustainable improvements.
“Companies that take a narrow approach to lean get some cost improvements,” says AMR’s
Parker, noting that some companies use lean as an alibi for layoffs or to squeeze lower prices out of suppliers. “But the results are not sustainable,” he warns.
A healthier approach is to treat lean as a stimulus to growth.
“The key to Pella’s success is our people,” says Van Zanten, noting that Pella’s headcount has grown significantly since embracing lean.
Rather than laying off factory staff as processes have become more efficient, the firm has expanded its product line to include doors. In fact, companies that have adopted the lean approach often find that their market share increases because quality and lead-time improvements give them powerful competitive advantages.
Inventory reduction: Carrying inventory costs a company in warehouse space, constrained capital and potential handling damage. Excessive inventory also slows down the manufacturing process and becomes a drag on lead times while reducing needed agility. Companies making smaller product batches are also more likely to spot and easily repair defects without disrupting production cycles. At Pella, as soon as the window maker began lean manufacturing in 1993, manufacturing costs dropped, inventory shrunk and there was more available space on the shop floor.
“We had fantastic results,” remembers Van Zanten, adding, “You can see the strong upward trend in our sales growth.”
Shorter cycle times: Through tireless elimination of waste in production, dedicated lean practitioners such as Emerson, Pella, Toyota and controls and tools maker Danaher are able to manufacture products more quickly.
“The shorter cycle times give you a lot more flexibility” to respond to market shifts, explains Parker.
Customer orders can enter the manufacturing process sooner, without having to wait for a planned lot, and materials progress through the production process faster, without waiting in lengthy queues at each workstation.
Greater flexibility: That flexibility is key in many industries today — from home appliances to large industrial equipment — where product life cycles are shrinking.
“Global companies need to become real-time enterprises,” notes Oracle’s Mr. Reindl. “If they don’t have lean processes in place, they won’t be able to meet market demands.”
Enhanced agility — the ability to respond almost immediately to customer demands — is a key benefit of a lean approach.
Challenges to lean efforts
Programs that deliver continuous improvement also require continuous effort, however, and companies should shed any illusion that reaping the benefits of lean/Six Sigma is easy. As with all change, achieving a transformation to lean manufacturing takes hard work, inspired leadership and indefatigable dedication.
A first challenge is to move beyond slogans to deeds, and actually implement lean principles. Only half the companies that say they are adopting lean and Six Sigma principles are actually doing so, estimates Sharma. A key test, he says, is to check the firm’s inventory turns. If a manufacturer turns its inventory only six times a year, or once every two months, the firm can hardly be called lean. Companies committed to lean methods are more likely to have an inventory turn of 10 or higher.
“To be responsive, you have to lower lead times,” Sharma adds.
Corporate inertia is another obstacle, particularly where shop-floor personnel cling to traditional notions learned early in their careers. It’s hard, for example, for the operator of an expensive machine to discard the notion that idle machinery loses money. After decades of getting the most production possible out of all machinery, workers have a hard time understanding how much a company loses when it produces products for which there is no demand.
There are conceptual challenges for management as well. Managers need to understand that the old measures of success — efficiency and utilization — have been supplanted by agility, increased inventory turns and reduced cycle times, along with top quality. The measures needed to effect this change in mind-set can upset many longstanding processes, including performance reviews and pay rates, and raise strong emotions. Indeed, half of the respondents to the Economist Intelligence Unit survey identified company culture as a key challenge for lean/Six Sigma, and 45 percent cited a lack of resources for staff training as a stumbling block.
The upheaval inherent in Lean/Six Sigma programs means that the engagement of senior management is required for successful implementation. Adequate resources must be allocated
to train employees, and resolve is also necessary to push through reorganization in production processes and inventory management.
“A lot of companies want to go down the lean path but they waver on the senior team commitment,” says Pella’s Printz.
Using technology to get lean
A final challenge comes in employing technology to create a rapid and efficient flow of information between all the parties in a supply chain. Such a seamless information flow is essential to reaping the benefits of lean/Six Sigma. IT allows lean manufacturers to stay in sync with suppliers, says Parker, while helping to tackle the unwieldy challenges of modeling, calibrating, operating and improving manufacturing.
“Technology can look forward to tell you how to smooth production and optimize customer service levels,” says Sharma.
IT can also help with “what-ifs” in, for example, reconfiguring a factory floor or determining the optimal location for inventory.
Especially at large organizations, where so many departments, plants and subsidiaries need to operate together to achieve a common goal, technology can help to keep everyone moving in step with, for example, flow scheduling.
“Information can help quicken and sustain the adoption of lean,” says Manish Modi, Oracle’s senior director of manufacturing applications development. “Technology truly helps you move to a make-to-demand model.”
A good technology backbone system acts as a repository for customer and production data and provides the key performance indicators that are used to measure success in both lean and Six Sigma initiatives.
Corporate business systems need to be flexible enough to allow the data flow to map closely to business processes; otherwise, errors and inefficiencies can creep in. Flexibility is also key to the “controlled experiment,” a core lean/Six Sigma principle that calls for testing a variety of possible outcomes to determine an optimal solution. If information cannot be captured accurately for such scenarios, the results may be distorted or completely useless. Advanced technology systems now include multiple business process flows that enable companies to run such tests.
These “best practice” business flows can inspire other companies to jumpstart their own process mapping.
For all the pluses, companies using technology to achieve Lean/Six Sigma goals need to heed two guidelines:
First, an emphasis on simplicity means that the adoption of lean methods does not necessarily entail higher IT spending. Emerson’s IT Shared Services department has been able, in fact, to use lean methods to reduce costly or unnecessary IT use.
Lean manufacturing aims to reduce transactions to a minimum, so it can eliminate needless transactions that raise reporting and labor costs — without adding value.
Second, it’s crucial that business needs, rather than technology, determine the actual map of information flow.
“You have physically to change your process first and then bring in the technology to help,” says Sharma. “You cannot depend on technology alone. Using technology as a panacea gets a lot of companies into trouble.”
Pella ’s Van Zanten concurs.
“Simplify the process first,” he recommends, “and then technology is a beautiful thing.”
SIDEBARS
The origins of “lean”
“Lean” was a Japanese invention, inspired by a plant tour of Ford Motors in the 1950s. After watching an American assembly plant build cars in a more efficient way than they used at home, two Japanese executives developed the Toyota Production System (TPS). This approach propelled Toyota from a modest domestic firm to a global car giant.
Indeed, while much of the car industry has suffered from a lackluster economy, Toyota saw its net income increase 23.2 percent in the half year to September 2003 from the same period the previous year — on a revenue increase of 8 percent.
“Today, even when everyone else is struggling, Toyota continues to make money,” says Anand Sharma.
Once TPS was well established within Toyota, the firm recognized that many potential gains would go unrealized if its partners weren’t also involved. So in the 1970s, Yoshiki Iwata and other lean pioneers from Toyota created Shingijutsu, a consulting company with the mission of bringing the TPS gospel to outside firms. As early as 1989, Shingijutsu worked with Danaher’s Jacobs Equipment Company brake plant and helped to establish it as the first facility in the U.S. to go lean. TPS eventually came to widespread notice in the US with the 1992 opening of a Toyota Supplier Support Center (TSSC) in the U.S. state of Kentucky.
In the years since TPS was developed, lean principles have expanded beyond Japanese car making to other industries and around the globe. In Asia, most multinationals are already involved in lean programs, and “there is a big uptake among indigenous” local manufacturers as well, says Brad Perkins, a senior director in discrete manufacturing industries at Oracle in Singapore.
In the U.S., carmakers have a lead, but other industries are waking up to the opportunity, says Manish Modi, Oracle’s senior director of manufacturing applications development.
U.S. manufacturing companies that had been firmly focused on other techniques such as just-in-time manufacturing were quick to adopt and rapidly refine lean manufacturing. Industry segments where margins are very thin, such as automotive and industrials, lead the way.
Six Sigma is often paired with Lean principles in manufacturing efforts to ensure flawless product quality and repeatable execution. It originated in the U.S. in 1986, when Bill Smith, a senior engineer and scientist at Motorola, devised a standardized way to count defects. The name is inspired by the Greek letter sigma, used to denote standard deviations in statistics. Six Sigma programs, employed by firms as diverse as GE, Allied Signal and Tyco, use detailed data analysis to improve all business processes, with the aim of achieving a defect rate no higher than 3.4 per million. Coupling lean and Six Sigma helps deliver value to customers in a repeatable manner.
The lingo of lean
A lot of lean vocabulary is derived from the Japanese language. You don’t need to use these
words to adopt lean methods, but knowing them can be helpful when working with consultants and partners.
Jidoka is a means of stopping production when flaws are detected. Sakichi Toyoda, the founder of Toyota, fathered the notion when he invented an automatic loom in the early 1900s. The loom stopped when any thread broke, letting a single operator oversee production on many looms at the same time.
Kanban is a card, sign or signal that triggers replenishment of a material when it is required to continue the production process. Kanban control ensures that parts are not made except in response to demand.
Kaizen means continuous improvement, or changing for the better. “Kai” means “to change” and “zen” means “for the good.” So during a “Kaizen event,” a team scrutinizes a manufacturer’s operations and then makes suggestions on how to improve them.
Poka-Yoke refers to a mistake-proofing procedure to prevent defects during ordertaking or manufacturing. It comes from “poka,” meaning “errors,” and “yoke,” the verb “to avoid.”
The seven wastes are the most common wastes found in physical production, catalogued by lean pioneer Taiichi Ohno, namely, overproduction ahead of demand, waiting for the next processing step, unnecessary transport of materials, overprocessing of parts due to poor tool and product design, keeping inventories of more than the absolute minimum, unnecessary movement by employees during work and production of defective parts.
Takt , derived from the German “der Takt,” meaning “beat” or “pulse,” is the rate of customer demand. A lean manufacturer’s goal is to be right on the takt time.
Table 1: Corporate goals for Lean/Six Sigma
(Multiple responses possible)
Manufacturing costs reduction 90%
Improving productivity 87%
Removal of waste 79%
Continuous improvement culture 74%
Customer satisfaction 69%
Yield improvement 67%
Improved capacity utilization 62%
Reducing labor costs 59%
Improving inventory performance 59%
Improved delivery performance 54%
Revenue enhancement 51%
Reducing supplier costs 36%
Enhanced stock price 28%
Source: Economist Intelligence Unit survey, December 2003.
Table 2: Challenges in implementing Lean/Six Sigma
(Multiple responses possible)
Company culture 48%
Lack of funds for staff training 44%
Lack of understanding of approach 34%
Investment/cost 31%
Lack of access to management information 27%
Lack of understanding of benefits 27%
Lack of top management support 26%
Lack of technology 19%
Nature of manufacturing facility 18%
Pressure to outsource 16%
Multinational sites 6%
Source: Economist Intelligence Unit survey, December 2003.
Ten tenets of lean manufacturing
If your company wants to get lean, what’s the best way to start?
Secure backing from the top
Before doing anything, get firm support from your company’s decision-makers. “If you are not Lean and want to get started, the top management team has to understand what they’re getting into,” says TBM’s Sharma. Adds Emerson’s Hamby: “You need a top-down approach, rather than a grass-roots effort.”
Roll up your shirtsleeves
Lean can produce dramatic improvements. But no one said it would be easy. “Many people are looking for a quick answer to a difficult problem,” says Sharma. “They don’t hear that they’ll have to do some work first.”
Communicate and educate
“We spend a lot of time communicating before, during and at the end [of a Kaizan event, when a team scrutinizes operations and then makes suggestions for improvements] to make sure everyone understands,” says Pella’s Van Zanten. “Communication is key. When we have a success, we really communicate it.” Adds Emerson’s Stephen: “You need a lot of education. Build awareness, train people and get some champions.”
Don’t skimp on training
Lean manufacturing goes against the grain of many manufacturing traditions. “Leave enough time to change the thinking within the company,” advises Parker. “Test and make sure there is a level of understanding. If [the staff doesn’t] get it on the first round of training, do another round. Make sure you have the culture turned around before going forward.” Remember that Lean changes more than just production processes; it can affect everything from personnel performance measures to how salespeople promise delivery dates to customers.
Apply suitable metrics
Re-jig how you measure success and failure. “Under the old cost-accounting system, your score was good if your most expensive machine was running 24/7,” notes Parker. Lean can’t succeed, he says, “if you don’t change the way people keep score.” The traditional measures of success — efficiency and utilization — need to be replaced with agility, lead time, inventory turns and quality across the board.
Help your partners
“If you don’t extend Lean beyond your four walls, you will have dissatisfied suppliers,” warns Oracle’s Modi. “Companies that are far reaching have educated their suppliers on lean.” In fact, the most successful lean companies involve their suppliers in product design in order to improve quality and simplify manufacturing. And they work together to improve communication methods and shorten lead times throughout the supply chain.
Think big
As a company shortens its production cycles, manufacturing experiments can be quick and painless. So an attempt to improve things can hold tremendous potential, and can be made without serious consequences — even if it fails. “When in doubt, be bold,” advises Van Zanten. “We set aggressive goals. You can’t just make minor tweaks.”
Shift the goalposts
“Don’t declare victory too soon,” recommends Sharma. Pella’s Van Zanten likes to remember how after a year of lean efforts, the CIO asked him for a progress report. “About 25 percent,” Van Zanten estimated. A year later, the CIO asked the same question, yet this time the response was 10 percent. The anecdote shows that lean manufacturing is like getting a new pair of glasses that help you continually to see new ways in which to reduce waste and improve business. “The more you do, the more opportunities there are that become visible,” adds Pella’s Printz.
Get the faith
“Continuous improvement (kaizen) is our way of life,” says industrial conglomerate Danaher, which has been a lean manufacturer since the 1980s. Only with focus and dedication can Lean/Six Sigma bring benefits to your company. “We are finding that customers who have adopted lean as a religion are seeing bigger benefits,” says Modi.
Prepare for the long haul
Lean doesn’t end after you reach your first set of goals, and it’s not a finite project with a beginning and end date. Rather it’s a way of business life that executives need to pursue continuously. “There’s a vigilance that has to be maintained from the executive suite,” says Parker. “You’re always looking for a better way,” adds Robert Azavedo, Oracle’s director of discrete manufacturing industries in Europe. “The journey never ends.”
Part I:
Survey respondent demographics
Number of completed surveys: 84
Location of head office
Western Europe 43%
North America 30%
Asia-Pacific 12%
Middle East/Africa 7%
Latin America 5%
Eastern Europe 4%
Company revenues in 2002
Less than $500 million 54%
$500 million to $1 billion 8%
$1 billion to $5 billion 17%
$5 billion to $10 billion 10%
More than $10 billion 12%
Job title
CEO/COO/Chief executive/Managing director 21%
CFO/Treasurer/Comptroller 11%
CKO/CIO/Technology director 7%
VP/Director of marketing or sales 8%
VP/Director of manufacturing 6%
VP/Director of supply chain, planning or operations 4%
VP/Director of logistics or customer service 2%
Research manager 2%
IT manager 2%
Other manager 19%
Other 17
Manufacturing industry sub-sector
Industrial products and components 61%
Durable goods 32%
Heavy equipment and machinery 7%
Part II: Survey results
What is your perception of lean/Six Sigma?
(Multiple responses permitted)
Lean/Six Sigma is great in principle but hard to achieve 35%
Lean/Six Sigma is a key competitive differentiator in the marketplace 35%
Lean/Six Sigma is similar to Business Process Re-engineering (BPR) 20%
Lean/Six Sigma is an important goal in the long term, but our near-term focus is to improve profitability 19%
Lean/Six Sigma is a realistic objective in one to two years 18%
I don’t understand the term 17%
Lean/Six Sigma is an empty slogan 8%
Other 5%
Is your company enacting a formal lean/Six Sigma program?
No, we have no formal program 42%
Yes, we have a formal and structured program 23%
No, but we have a program in the planning stages 15%
No, but we are enacting similar initiatives under a different name 20%
If you have a lean/Six Sigma program, how long has it been in operation?
Less than a year 29%
One to five years 63%
Five to ten years 8%
More than 10 years 0%
How extensively is your lean/Six Sigma program deployed?
Only sporadically 14%
At a process level 30%
At a function level 24%
Enterprise-wide 27%
Across the extended supply chain 5%
How extensively are Kaizen (continuous improvement) projects and events structured, planned and implemented?
Only sporadically 28%
At a process level 18%
At a function level 28%
Enterprise-wide 21%
Across the extended supply chain 5%
What are your company’s goals for lean/Six Sigma?
(Multiple responses permitted)
Manufacturing costs reduction 90%
Improving productivity 87%
Removal of waste 79%
Continuous improvement culture 74%
Customer satisfaction 69%
Yield improvement 67%
Improved capacity utilization 62%
Reducing labor costs 59%
Improving inventory performance 59%
Improved delivery performance 54%
Revenue enhancement 51%
Reducing supplier costs 36%
Enhanced stock price 28%
What metrics does your company use to assess the success of lean/Six Sigma?
(Multiple responses permitted)
Annual productivity (sales per employee) 54%
Annual profitability 54%
On-time delivery (OTD)
performance to promised date 51%
Annual inventory turnover 38%
Annual sales 33%
Other 31%
What metrics does your company use to assess the success of lean/Six Sigma?
(Multiple responses permitted)
Annual productivity (sales per employee) 54%
Annual profitability 54%
On-time delivery (OTD) performance to promised date 51%
Annual inventory turnover 38%
Annual sales 33%
Other 31%
In what areas does your company plan to launch lean/Six Sigma initiatives in the future?
(Multiple responses permitted)
Manufacturing 60%
Distribution and logistics 57%
Sourcing 45%
Finance and other back-office functions 36%
Product development 26%
Information systems 30%
Human resources 28%
Corporate communications and advertising 15%
Other 2%
What have been the major challenges to implementing a lean/Six Sigma program?
(Three responses permitted)
Company culture 48%
Lack of funds for staff training 44%
Lack of understanding of approach 34%
Investment/cost 31%
Lack of access to management information 27%
Lack of understanding of benefits 27%
Lack of top management support 26%
Lack of technology 19%
Nature of manufacturing facility 18%
Pressure to outsource 16%
Multinational sites 6%
About this white paper
This Oracle white paper was written in cooperation with the Economist Intelligence Unit. The Economist Intelligence Unit wrote an initial draft of the white paper based on a survey of senior executives in the manufacturing industry, input from Oracle executives and interviews with business leaders and experts on industrial manufacturing. Feedback from Oracle was included in a revised, final draft.
About Oracle
Oracle is the world’s largest enterprise software company. Its product line includes enterprise business solutions that extend support for Lean methods to all facets of internal operations and business interactions with supply-chain partners. For more information, visit our website at www.oracle.com.
About the Economist Intelligence Unit
The Economist Intelligence Unit is the business information arm of The Economist Group, publisher of The Economist. It is the world’s leading provider of country intelligence, with over 500,000 customers in corporations, banks, universities and government institutions. Our mission is to help companies do better business by providing timely, reliable and impartial analysis on market trends and business strategies. For more information, visit our website at www.eiu.com.
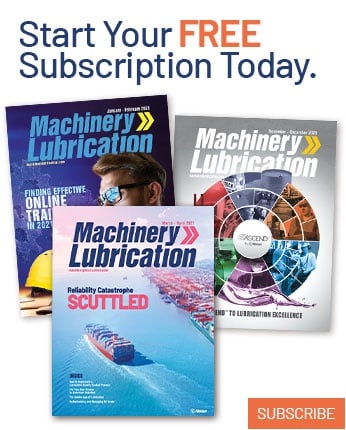