Condition-based lubrication of roller bearings depends on ultrasound data collection to warn when regreasing is required. Lube techs regrease bearings using an ultrasound sensor interfaced to a grease gun. The sensor provides a signal to the ultrasonic data collector, giving the technician both an audible and a digital guidance system designed to prevent damage from overgreasing. Some confusion about how much grease is enough still remains a question mark. Some advice:
- Send lube techs to an ultrasonic training class.
- Set alarms to relubricate at 8 to 10 dBµV over baselines established by a digital ultrasonic condition monitoring program.
- For consistency, use the same ultrasonic instrument for both condition monitoring and relubrication. Preferably, the ultrasonic device should provide digital measurement and listening capabilities. “Listen only” units are subjective and depend on the hearing capabilities of multiple users.
- Apply grease slowly while both listening and measuring. Your target is to return the dBµV values back to baseline.
- Grease … then wait. Don’t hurry at the expense of doing the job correctly. Allow the grease to work into the cage, rollers, and grease cavity. The bearing may initially go quiet, and then loud again as the grease is worked in.
The 8 to 10 dBµV rule works in most instances, however statistics are a poor substitute for common sense. Use these guideline in harmony with you company’s established greasing protocol to arrive at a unique procedure that suites your needs.Look at the ultrasonic signal in time domain. The bearing was loud with non-sinusoidal peaks. The moment of truth when the grease actually reaches the bearing is both audible and visible.Click Here to request an electronic copy of the sound file associated with this application.For more information, visit www.sdtnorthamerica.com.
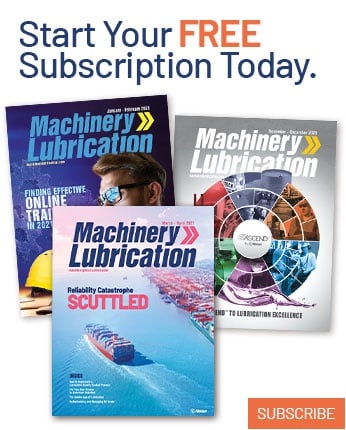