Lean manufacturing initiatives at Moyno Incorporated’s plant in Springfield, Ohio, have two objectives – to ensure the cost savings needed to remain profitable in a global economy and to retain highly skilled employees.
Moyno, a unit of Robbins & Myers Inc., is a leading manufacturer of progressing cavity pumps, multiphase fluid transfer systems, grinders and controls.
The 5-S efforts included in Moyno’s lean program involve five specific areas of focus: sort, set in order, shine, standardize and sustain. At the plant, 5-S is being implemented in six areas. Particular benefits have been seen in the chrome plating area, the small pump area and the office area.“The key to successful lean manufacturing implementation is strong management support,” said Ben Bullis, lean facilitator for Moyno’s Springfield plant. “It’s important to identify goals up front and then properly implement the required changes to address the root causes of identified issues that are impacting efficiency. Once issues are resolved, management conducts regular audits to ensure sustainability.”
In the chrome plating area, the 5-S team reorganized and added color-coded hangers and information signage to optimize communication. Equipment was moved closer to the work area to eliminate wasted time in transporting components. The team also eliminated unneeded equipment to free up space for future growth. To ensure sustainability, regular 5-S audits are in place.
In the small pump area, 5-S lean enhanced flexibility and improved throughput. By implementing cellular manufacturing, the team was able to eliminate unnecessary waste and improve efficiency. Moyno also worked with suppliers to switch to container packaging for additional efficiency improvements. Finally, a just-in-time inventory system was implemented to optimally align with customer delivery requirements.
5-S was also used to organize the office area to achieve increased productivity. An employee suggestion program was implemented throughout the facility.
“We’ve had excellent buy-in from employees, and everyone understands the importance of sustainability,” Bullis said. “We have been able to reduce time, waste and cost, which makes us much more competitive in the global marketplace.”
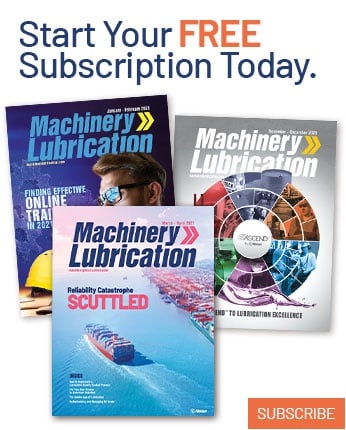