The first all-new 2007 Tundra full-size pickup rolled off the assembly line at Toyota Motor Manufacturing Texas Inc., or TMMTX, on Friday, November 17. The line-off of the new Tundra marked the official grand opening of the $1.28 billion
"The full-size pickup truck market is, by far, the single-largest opportunity for Toyota's future growth plans in the U.S.," said Don Esmond, senior vice president of automotive operations, Toyota Motor Sales U.S.A. Inc. "Thanks to this highly efficient plant, the on-site suppliers and all the team members, we plan to take full advantage of that opportunity. The new Tundra will arrive in showrooms in February. Our production and sales goals are ambitious, yet realistic, and reflect our confidence in the product."
If the class-leading new 2007 Toyota Tundra is the largest, most sophisticated and most powerful half-ton pickup truck ever built, it's only fitting that the factory where it is first assembled is the most advanced that
Location
The TMMTX plant is located on the 2,000-acre site of the former Walsh-Small Ranch, said to be the oldest cattle ranch in
An important component offered by the
To accomplish this, the plant is near two major Interstates, 10 (east/west) and 35 (north/south), which connect it to the nation's interstate highway system. It is also immediately adjacent to a pair of competing rail lines. This gave
Team members
The second critical factor for choosing
Groundbreaking
With the necessary conditions of land, transportation and workforce addressed, and the city selected,
This was an enormous task, considering the 6.5 million cubic yards of dirt moved, the 250,000 yards of concrete poured (enough to pave a two-lane highway 53 miles long), the 15,000 tons of steel erected and the 10 acres of railway siding installed.
At a total cost of $1.28 billion, the result is 2.2 million square feet, or 46 acres, of main factory built to construct the 2007 Tundra from scratch, starting from coils of steel rolling into one end of the building and ending with gleaming, powerful trucks rolling out the other. The plant contains stamping, welding, paint, plastics and assembly facilities where TMMTX team members can build Tundras at a rate of up to about 750 per day.
On-site suppliers
On-site and fully integrated with the main plant are separate production and assembly facilities for 21 individual parts and component suppliers. That means that an additional 1.8 million square feet were constructed to house their operations and an additional 2,100 workers. There are many advantages to this arrangement, not the least of which is logistics costs. Traditionally, auto suppliers are located in the
Co-location also speeds communications. TMMTX and its on-site supplier partners can quickly react to and solve problems as they arise. It's also better for the environment, reducing over-the-road trucking and resulting emissions. Finally, the on-site suppliers invested an additional $300 million at the site, a further economic development boost for the community.
Seven of the 21 on-sight suppliers are minority-owned, including six new joint ventures between San Antonio-based businesses and traditional
Production process
Building Tundra is a highly choreographed process. First, Toyota Motor Sales (TMS) places orders. They create long-range forecasts so manufacturing can order parts, and production-controllers can tell plants what exactly to build. In a process called "sequential build," each bare chassis comes down the line and has a paper manifest attached, that shows what type of parts the truck needs, much like a recipe. This requires a sophisticated parts-delivery system to ensure that parts are getting to the line to match the vehicles. Having the seat company on site, for instance, means that the seat company will get a list of the exact vehicles to be built that day and in the order in which they'll be built. The finished seats are shipped to the plant and loaded onto the assembly line in the proper order. Team members verify that the seat is correct.
TMMTX operations will ramp up in steps. Beginning back in September, the plant began pilot versions of the truck. This phase was designed to make certain
• that all the production equipment works as it was designed to work
• that all manufacturing processes all work as they should
• all team members are properly trained
• and that all the parts fit together correctly on the truck.
The TMMTX factory floor features a blend of automation and manpower. In the welding and painting areas of the plant, robots do much of the work. Nearly 400 handle painting and welding, making those areas about 90-percent automated.
Even where manpower is primarily used, a variety of "assist devices" help assembly workers lift and move heavy, bulky items such as seats and doors. Using this creative combination of muscle and machine, it takes about 24 hours going from raw, coiled steel to finished, painted, rolling and running state-of-the-art pickup.
Environmentally advanced
In keeping with its state-of-the-art technology and processes,
Water, in fact, is an important consideration in this area of
In addition to conserving resources and preventing emissions, the
For instance, scrap steel will return to the steel mill, scrap plastic will be shredded and returned to a pellet manufacturer. Even the amount of packaging of new parts – packaging that might ordinarily be thrown away – has been minimized. Substituting wooden pallets with plastic will also make a difference. Wood breaks up and wears out, then must be disposed of in a landfill, while plastic can be used over and over again for a much longer period of time.
"TMMTX is a not only a brand-new plant for a brand-new truck, it's
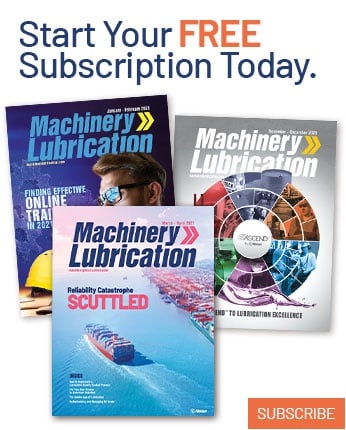