A series of promising new technologies in steam generation could reduce U.S. industrial steam system operating costs by more than $10 billion annually, saving 185 trillion Btu per year. At the same time, the technologies would curb environmental emissions by nearly 2.7 million metric tons of carbon equivalent annually.
The new technologies are bundled in a unique, interconnected boiler system known as "Super Boiler." Combining innovations in combustion, heat transfer and recovery, vessel engineering, and controls in a highly efficient steam-generation system, the Super Boiler has a 50 percent smaller footprint than conventional boilers and minimal environmental impacts.
These innovations began in 2000 with a research and development partnership consisting of the U.S. Department of Energy's (DOE) Industrial Technologies Program (ITP), the Gas Technology Institute, Cleaver-Brooks, Southern California Gas Company and several others (please see the sidebar below). Now, the Super Boiler project is well on its way to demonstrating a first-generation Super Boiler that integrates several novel technologies to achieve extraordinarily high efficiencies (greater than 94 percent) and low emissions (less than 5 parts per million by volume (ppmv) of nitrogen oxides).
Time for a New Steam Technology
Today, both the potential and the need for a cost- and energy-saving Super Boiler technology are especially great. U.S. industry currently uses more energy for steam production than for any other single purpose, and it costs about $18 billion or more annually just to feed the boilers that generate the steam. But despite its major role in energy consumption, industrial steam generation technology has not progressed significantly since the end of the 19th century.
Now, however, industry has an important window of opportunity as an aging stock of industrial boilers nears retirement. The U.S. manufacturing sector uses more than 33,000 boilers with capacities greater than 10 million Btu per hour (MMBtu/hr). The largest block of those boilers was purchased in the 1960s, and more than 80 percent were purchased before 1978. About 60 percent of them are concentrated in just five industries: paper, chemicals, refining, food and primary metals.
This Super Boiler Conceptual diagram shows key design innovations, such as a transport membrane condenser, compact humidifying air heater, and staged/intercooled combustion system.
Designed for Super Efficiency
The boiler geometry incorporates a two-stage firetube design that is both compact and highly efficient. Key innovations include a transport membrane condenser (TMC) and a compact humidifying air heater (HAH) to extract sensible and latent heat from the flue gas for increased energy efficiency, compact convective zones with intensive heat transfer, and a staged/intercooled combustion system for ultra-low emissions.
This unique boiler design, which incorporates high-intensity heat transfer using extended surface firetubes, exhibits confirmed heat transfer coefficients approximately 18 times higher than those of plain firetubes. In laboratory tests, the technology reduced nitrogen oxides (NO x) to as low as 3 ppmv while maintaining carbon monoxide levels below 10 ppmv across the firing range. Excess air is maintained at 3 percent or lower, for improved efficiency in comparison to low-NO x burners that employ flue gas recirculation or high amounts of excess air.
The Super Boiler installation team for the demonstration project at Specification Rubber Products included (L to R) Bob Tucker, ADCO Boiler; Dexin Wang, Gas Technology Institute (GTI); Gerd Janssen, GTI; Bob Spiegel, Cleaver-Brooks; Tony Fischer, Specification Rubber; and Tom Nyman, Cleaver-Brooks.
From Demonstrations to Markets
Commercial prototype designs for both single-stage and two-stage boilers scaled up to 11 MMBtu/hr (300 horsepower) have been completed, and demonstration testing has begun. Current field tests at Specification Rubber Products in Alabaster, Ala., are encouraging; using a single-stage, 300-horsepower, gas-fired Super Boiler with TMC/HAH heat recovery, tests are confirming a 94 percent fuel-to-steam efficiency.
Further tests are also scheduled for Clement Pappas & Company in Ontario, Calif., using a two-stage unit. A TMC/HAH retrofit will also be tested on a conventional boiler in Utah. At the same time, laboratory development continues on an ultra-clean, dual-fuel capability for the Super Boiler.
Once energy cost savings are successfully demonstrated, Cleaver-Brooks plans to market a new line of high-efficiency, low-emissions industrial firetube boilers. At present, both the one- and two-stage boiler designs are being considered.
The one-stage boiler has a capability for oil backup firing and so can address a larger market. The two-stage intercooled boiler is not currently equipped for liquid fuel firing, so its market is limited mainly to California. However, plans are under way to develop a backup oil firing capability for the two-stage intercooled boiler, which will greatly expand its potential market. Plans are also under consideration to expand and apply Super Boiler innovations to watertube boilers, alternative fuels, and nonboiler heat recovery applications.
For more information, see ITP's Super Boiler fact sheet ( PDF 1.19 MB). Download Adobe Reader. For updates on technology demonstrations planned for 2007, visit the ITP BestPractices Web site. You may also contact the EERE Information Center online or by calling 877-337-3463.
Prototype "Super Boiler" uses a two-stage, firetube design that is compact and efficient.
Super Boiler Project Partners
- DOE Industrial Technologies Program
- Gas Technology Institute
- Cleaver-Brooks Inc.
- GTI Sustaining Membership Program
- Pacific Northwest National Laboratory
- Southern California Gas Company
- Utilization Technology Development Company
- California Energy Commission
- South Coast Air Quality Management District
- California Air Resources Board
- Specification Rubber Products
- Clement Pappas & Company
For more information, please contact Bob Gemmer, DOE Industrial Technologies Program, or call 202-586-5885.
About the author:
This article was supplied by the U.S. Department of Energy’s Industrial Technologies Program. It first appeared in the Summer 2006 issue of Energy Matters from the DoE. For more information, visit www1.eere.energy.gov/industry/.
Read More Energy Matters Articles on These Topics
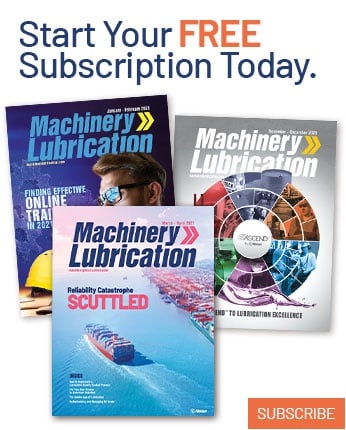