Dow Corning, the global manufacturer of silicon-based materials, is using a dynamic simulator, built and implemented by Invensys Process Systems, to train operators at its Barry, South Wales, production facility in the United Kingdom. It is anticipated that use of the simulator will result in significant savings in training and manpower costs, enhanced plant safety and increased productivity.
The Invensys Operator Training Simulator (OTS) was built using advanced DYNSIM and FSIM dynamic simulation technology from Invensys' SimSci-Esscor unit (www.simsci-esscor.com).
Silicon-based materials have been produced at Barry since 1952. The process involves combining silicon powder with methyl chloride to produce chlorosilane intermediates which are then purified in distillation columns before water is added to produce siloxanes. A final polymerization stage then converts the siloxanes into a range of silicon-based fluids, resins and rubbers for delivery to customers world wide.
Dow Corning is dedicated to continuous improvement, while recognizing its responsibility for the health and safety of its employees, the well-being of its neighbors and the protection of the environment. Its processes involve potentially harmful materials and require precise control and smooth operation to try to prevent accidents and to maximize the plant's profitability.
The Invensys developed simulator is designed to train new operators in the intricacies of the various unit processes and assist experienced operators in dealing with potential emergencies, in a manner analogous to the training of airline pilots without their having to set foot in a real aircraft. Based on a detailed study of the process, together with input from Dow Corning engineers and operators, it provides a high fidelity dynamic model of the distillation section of the manufacturing process.
The simulator allows operators to practice procedures such as scheduled shut downs and start ups which may only be required once a year. During each session, the instructor, who has a view of every part of the process, can cause any key component such as a pump to fail at a critical moment. The trainee operator, seated at a console identical to that in the actual control room, then has to deal with the consequences of the event, just as if it were occurring on the real plant. Dow Corning reports that trainee operators are soon drawn in by the realism of the system and quickly forget that it is only a simulation. "I learned more in two hours on the simulator than I did during two weeks in the plant," commented one operator.
Use of dynamic simulation for operator training doesn't just benefit the operators, however. Its benefits go straight to the bottom line and, particularly on new plants, can help to locate potential design and process errors and identify faulty control logic.
"Using the simulator, we expect that operators will be trained to run a new unit efficiently in four months, instead of the six months taken previously," explained Ross Davies, Dow Corning's training coordinator at the Barry site. "Untrained operators must be 'shadowed' by an experienced person for the duration of their training, so this effectively doubles the cost during the training period. Utilizing the simulator will reduce the training period and provide higher quality training and realism, thus increasing plant productivity significantly."
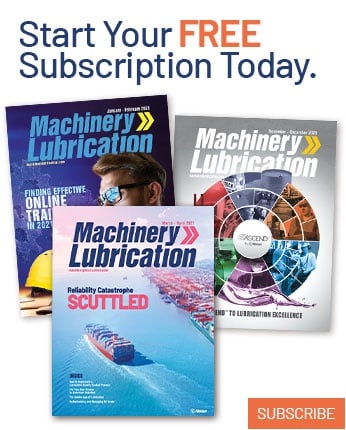