With the inauguration of the Juan Carlos I Supplier Park in October 1996, Ford's assembly plant in
This model has been successfully replicated since then at all of Ford's major assembly plants in Europe,
All of Ford's supplier parks in
In most of the cases, the supplier parks are linked to the Ford facilities by two separate delivery systems – an enclosed overhead conveyor system connecting to individual "drop" stations in the final assembly area of the respective plant, and/or a tunnel system that delivers parts directly into the plants' press and body shops. In some cases, drop-trailers are used for transportation.
Ford's priority for subassemblies from the supplier parks were for those with either long labor-intensive pre-assembly time, such as instrument consoles, wiring looms, steering wheel and airbags, or those that take up a lot of space next to the production line, as in the seats, fuel tanks and bumpers.
The suppliers are linked into the Ford plants' scheduling system, enabling parts to arrive not only just-in-time, but also in sequence, which means that each delivery reaches the assembly line at precisely the right time in the exact production sequence. These processes are controlled by Ford's central production control systems which are connected to the supplier parks via dedicated electronic data links. Ford informs the suppliers about the planned sequence of construction some days in advance. The order of production, i.e. the exact sequence on a given day, is determined by Ford's central production computer, which sends a message to the supplier about two to three hours before delivery is required. The trip through the conveyor to the assembly line takes 15 to 20 minutes on average.
"In time" and "in sequence" production obviates the need for hundreds of truck transports that would have otherwise been necessary every day in order to get parts from outside suppliers to the assembly plants.
"This is a big gain for the environment," said James Tetreault, vice president of manufacturing for Ford of Europe. "We are saving millions of truck-transport kilometers and liters of fuel, representing a significant emissions reduction."
In-sequence supply is also key to a continued reduction in the space required for storing single parts around the production lines of Ford's assembly plants. Thanks to the overhead-rail conveyance system, the packaging for the parts and components coming from the suppliers has been cut drastically. That lowers costs in areas, such as waste disposal, and also reduces the burden on the environment.
Ford's supplier park concept benefits quality as well. Proximity allows the plants to react jointly and even more quickly, to any concerns that might arise. These can be eliminated effectively without dealing with a backlog of already produced faulty components. That cuts all manner of auxiliary costs and reduces repairs. Most importantly, it is experienced by the customer in the form of greater and more consistent quality.
Through supplier parks, Ford has dramatically reduced the complexity of its in-house operations, cutting significantly the number of assembled parts to be handled by Ford workers.
The dashboard, for example, arrives in Ford plants as a single unit together with the steering wheel and the steering column. It was previously 300 separate items. The same is true of the front and rear suspension, the main wiring loom, and the door and side trim for the interior.
One of the best examples of the component manufacturing system is the seat supply process at the
The close connection between Ford and its suppliers is giving rise to a new form of partnership. The common use of social facilities and safety procedures emphasizes that. Ford is providing its paramedic services to the neighboring suppliers while the Ford fire brigades also cover the supplier parks.
Long before a new component can start coming off the production lines, the partners meet to plan efficient production methods in simultaneous engineering teams. Quality is enhanced with supplier involvement on the integration of the design of the parts with the assembly process.
"The success of our supplier parks is proof that total commitment and partnership between manufacturers and their suppliers can improve quality, benefit the customer and the environment and reduce costs," Tetreault said.
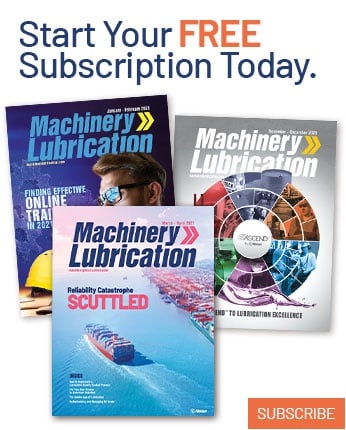