Welcome to the Exclusive Series
In the Windy City of Chicago, the 2024 Reliable Plant Conference provided a place where experts and beginners alike could find a safe haven to explore topics that have been top-of-mind for industrial facilities across the globe and unlock new skills to take their personal skills and facility practices to the next level.
Among them was Dr. Jody Parsons, a Certified Executive & Leadership Development Coach, who led his own session titled “From Task Manager to Effective Leader: The People Business Paradigm. " This session sought to attract leaders from every industry and help them unlock the skills necessary for employee development with their own teams.
Dr. Parsons’ session became a widely talked-about event, uncovering the crucial need for more training and learning opportunities when it came to industry leadership and employee development.
Now, Dr. Parsons invites you to join him in his new 3-part interview-style series as he engages with industry leaders across multiple sectors – who also attended the Reliable Plant Conference – to examine the unique challenges and successes often experienced when elevating employee leadership and reliability skills.
Prioritizing the Personal and Technical
Issues that directly affect plant reliability matter. Downtime, inefficient practices, misunderstandings, and ineffective communication can bring production to a halt. When production stops for any reason, a facility’s bottom line is gravely impacted.
As a result, reliability leaders must pay close attention to their processes, hardware, software, maintenance programs, and the longevity of their critical assets. This importance was highlighted on the exhibition floor at the Reliable Plant Conference, where vendors and end-users alike buzzed with energy and excitement about the possibilities the new ideas, methods, and tools being shared could bring to their own facilities.
But what about leadership practices?
Fortunately, many sessions offered at the Reliable Plant Conference encouraged participants to lead in innovative ways. Just as Reliable Plant leaders focus on the technical aspects of their work, there is also a great necessity to focus on the leadership aspects of the work.
Behind every process, technology, and maintenance issue, there is a person. And that person deserves more attention than the process. The question then becomes, “Why is it more difficult to implement leadership aspects than to implement technical aspects?” It is past time for industry leaders to have a dual focus on not only the tools and processes that make the work possible but also the people responsible for them.
Challenges and Triumphs of Leadership Implementation
To understand more about the challenges and triumphs of simultaneously implementing technical and leadership aspects from the Reliable Plant Conference into their facilities, I set out to make a three-part series that interviewed two industry experts to get their stories – Kevin Keith is a Lubrication Specialist for Blue Buffalo in Richmond, Indiana, and Erik Forbus is a Maintenance Planner and Schedule for Cardinal Corporation in Waxahachie, Texas.
In the first leg of our journey, I sought to uncover the power and potential of ideas and why it seems that, despite our best efforts and intentions, even the most compelling ideas for change can fail to make any headway in the facility.
JODY: You go to a conference, you get inspired, and you find yourself thinking, “I can use this!” But then you get home to your facility and find the daily grind is right there waiting for you, and suddenly, it seems like the good ideas and inspiration fade. What keeps you from implementing the ideas that excited you?
KEVIN: It depends on whether you have buy-in from coworkers and other maintenance techs, management… really anyone involved in the implementation of a new idea. Everyone has to be committed. It just takes one person saying, 'No.' Implementing a new idea is all about gathering buy-in from management and coworkers. What prevents people from buying in is fear of change or the thought that “this is the way we’ve always done it.” Or they don’t see the long-term benefit.
ERIK: I've been to three different types of leadership training. Some were good, but I was working with like-minded people, so our goals already aligned. But, at Reliable Plant, I was interacting with technicians on their level and taking notes, which is more efficient than the top-down approach. Through that, I found that there is resistance to bringing in a new path of direction. [To overcome this,] I have to give information, data, and real work experiences.
JODY: The technical aspects of your work that relate to Reliable Plant products may be easier to launch than leadership aspects. Why do you think that is?
KEVIN: Everyone likes the new “better” technology. But they need to realize that getting a new product in the door is all about cost. Everyone has to see the immediate benefit, and you have to be able to produce results. An idea doesn’t cost money to implement, but a product does.
ERIK: New toys are a lot cooler than what we used to use. Digital vs. analog is exciting. Whereas, with soft skills, people get used to a culture, a rut, a way of doing things because that's how it has always been done. The hardest part, especially in maintenance, is to show relatable success. If you can put a part on and push start, the machine runs - that’s a success. You may get the same results from other measurable data. The machine starts, the machine runs, success. Ideas take time for the benefits to show.
JODY: What makes implementing leadership concepts difficult?
KEVIN: You have to have buy-in. If even one person isn’t on board, we have to meet that person where they are to find out what's wrong and uncover their reservations.
JODY: During many sessions at the Reliable Plant Conference, we worked on Employee Engagement, Giving Feedback, and Asking Great Questions. Of these three, which do you feel like you naturally have the greatest amount of success with?
ERIK: I learned a lot from these sessions, and they showed me there is a difference between being a "task manager" and an "effective leader." I faced some ugly truths about team members being engaged, disengaged, and actively disengaged. I took this back and had great follow-up conversations with my boss about these concepts. It's difficult not to be hard on yourself, but he helped me see how far I've come as a leader and how our culture has changed for the better - which is hard to measure.
Stay Tuned for Part 2
In part one of my three-part series, we've laid the groundwork by covering the foundational elements of the ideas that take form through collaboration and how leadership attributes – such as soft skills – can be tricky to implement, no matter how valuable they are to plant reliability.
In part two, we will take a deeper look into what it means when team members are engaged, disengaged, and actively disengaged with their work and how this can not only have devastating effects on achieving the vision and missions of our companies but also our facility's reliability.
Stay tuned – part two is just around the corner.
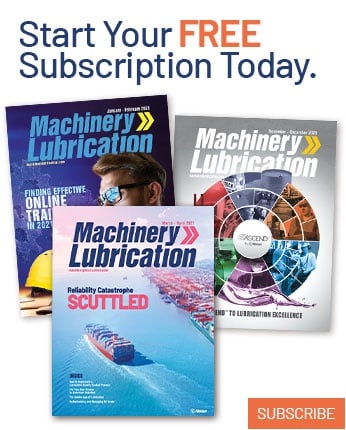